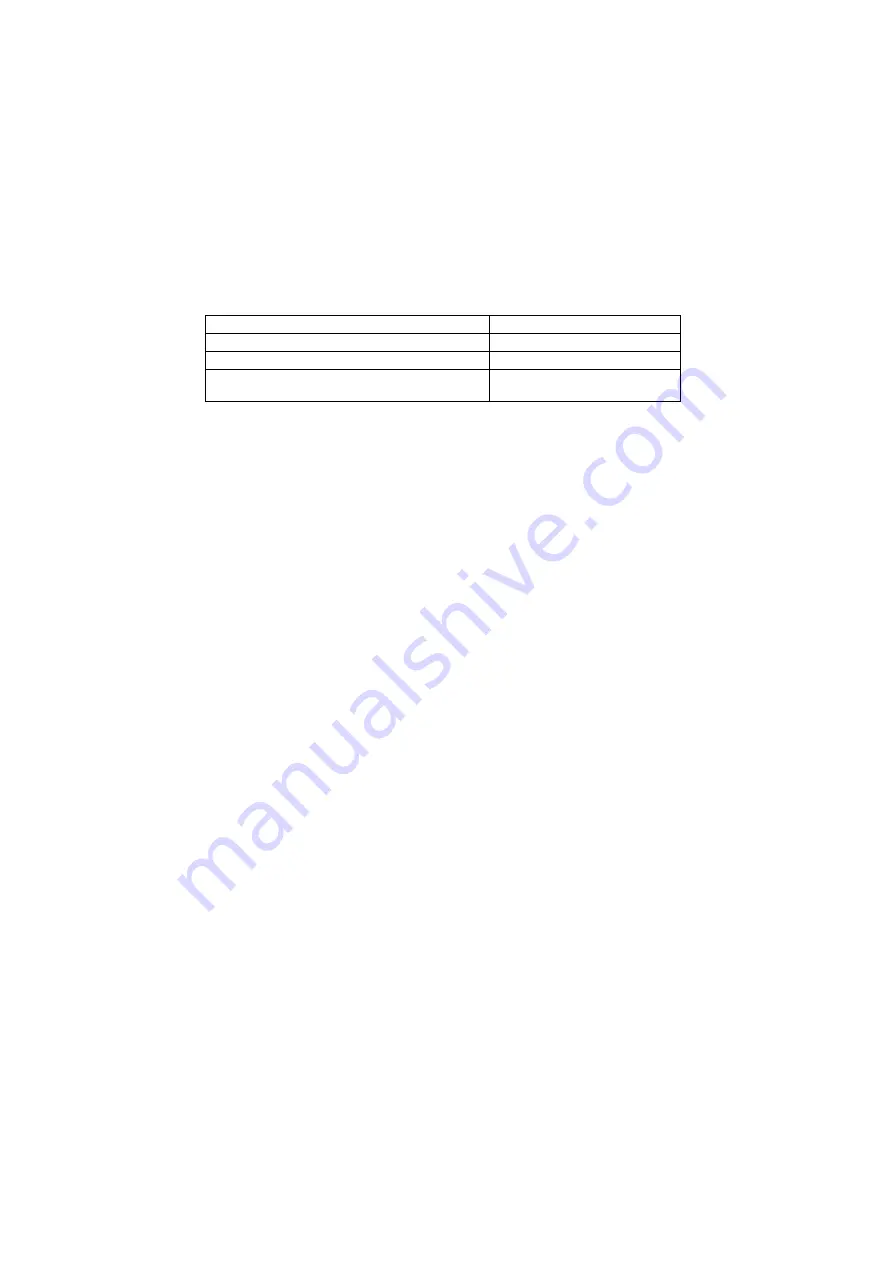
14
In order to ensure the proper, ecological and fuel–efficient functioning of Bio-max Plus
boilers, it is recommended to use pellet fuel satisfying the requirements of standard PN–EN
ISO 17225–2:2014–07.
Certified fuels from reliable sources are recommended. The fuels used should be of an
appropriately low humidity and have a low content of volatile substances. Minimum fuel
quality requirements have been presented in the following table.
Table No. 3. Minimum fuel quality requirements
Humidity content (in working condition)
≤
12%
Ash content (in working condition)
≤
0.5%
Calorific value
> 17 MJ/kg
Fuel class
C1 according to EN 303-
5:2012
When adding fuel to the tank it is necessary to pay particular attention to mechanical
contaminants (e.g. stones), which could damage the ancillary devices of the boiler (the
burner, feeding mechanisms, automatic ash removal system) and lead to failures for which
the equipment manufacturer shall not be held liable.
4.5. Connection to the central heating water system
Bio-max Plus boilers are factory–fitted with externally threaded stub connectors: a
supply stub connector, a return stub connector, a drainage stub connector and a safety stub
connector (the diameters of stub connectors for various boiler power ratings have been given
in
Table No. 1
). These stub connectors and their corresponding joints are used to connect
the boiler to the central heating system in the appropriate manner (so as not to mix up
“supply” with “return”, for example).
Connections must be made in accordance with the design and currently valid regulations, as
appropriate for the specific system type (i.e. open or closed).
−
Before connecting the boiler, it is necessary to thoroughly clean the system of all
possible contaminants (dirt, rust, etc.).
−
Do not use any magnetisers in the system.
−
Cut–off valves should be installed between the boiler and the central heating
system in order to enable dismantling of the boiler without it being necessary to
purge the whole system of water.
−
In order to protect the boiler against excessively low heating water temperatures
at the heating system return (below 45°C), which could lead to its premature
corrosion, it is required to install a three–way or four–way mixing valve and/or a
boiler feed pump.
−
Ensuring proper circulation in the central heating system will make it possible to
achieve a difference in temperature between supply and return of less than or
equal to 15°C.
−
Water filters should be installed at the heating water return from the central
heating system.
−
Boilers with a power rating in excess of 100 kW must be fitted with a parametric
water level sensor. Depending on the type of sensor, this should be installed on
the boiler in accordance with the attached instruction manual.
Summary of Contents for BIO-MAX PLUS
Page 8: ...8 Figure No 2 Component elements of the boiler Figure No 2 Component elements of the boiler...
Page 9: ...9...
Page 10: ...10 3 2 Technical parameters Figure No 3 Boiler installation dimensions...
Page 16: ...16 Figure No 7 Wiring diagram ecoMAX860P Standard and ecoMAX860P Touch...
Page 29: ...29...