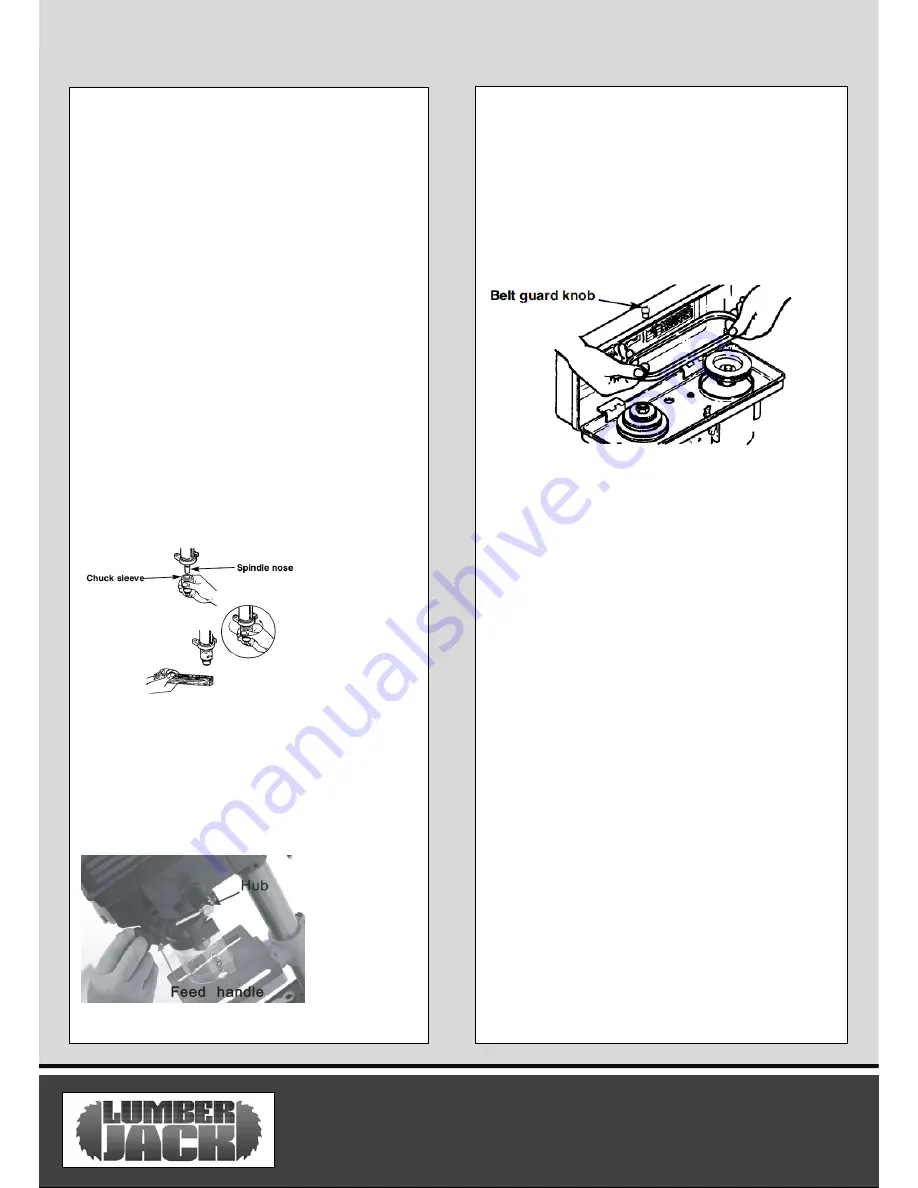
DP13-580B 09
Installation the chuck & arbor
1. Locate the chuck in the box of parts.
2. Tighten Philip’s head screws of the chuck
guard to quill shaft.
3. Clean out the tapered hole in the chuck, also
clean the spindle nose with a clean cloth. Make
sure there are no foreign particles sticking to the
surfaces. The slightest piece of dirt on the
spindle nose or the chuck will prevent the chuck
from seating properly. This will cause the drill to
“wobble” .
NOTE:
If the tapered hole in the chuck is
extremely dirty, use a cleaning solvent on a clean
cloth.
4. Push the chuck up on the spindle nose as far
as it will go.
5. Turn the chuck sleeve clockwise and open the
chuck jaws completely.
6. Lightly tap the nose of the chuck with a piece
of wood to insure the proper seating of the
chuck on the spindle.
Installation the feed handles
1. Locate the three feed handles among the
loose parts.
2. Screw the feed handle tightly into the
threaded holes in the hub.
Installing the belt guard knob
1. To attach the belt guard knob, use the knob and
a pan head screw from the loose parts bag. Insert
the pan head screw into the belt guard and screw
knob. Tighten.
WARNING! :
To
avoid possible injury, keep the
guard in place and in proper working order while
operating.
Tensioning the belt
NOTE: The drill press is shipped with the belt installed,
but it should be properly tensioned before use.
1. Lift the guard from the right side and keep it
opened.
2.
Release the belt tension lock handle located on
the right side of the drill press head. Pull the right
side of the motor towards the front to relieve the
spring tension of the belt. Tighten the belt tension
lock handle.
3. Choose the desired speed for your drilling
operation, and move the belt to the indicated
position. Refer to the chart on the inside of the
belt guard.
4. Loosen the belt tension lock handle and move
the right side of the motor backwards to apply
tension to the belt.
5. Tighten the belt tension lock handle.
NOTE: The belt should deflect approximately 1/2”
by applying finger pressure at the mid-point of the
belt between the pulleys.
6. Close the belt guard.
7. If the belt slips while drilling, readjust the belt
tension.
ASSEMBLY INSTRUCTIONS
Summary of Contents for DP13-580B
Page 21: ...DP13 580B 19 Parts Diagram...
Page 22: ...DP13 580B 20 Parts Diagram...