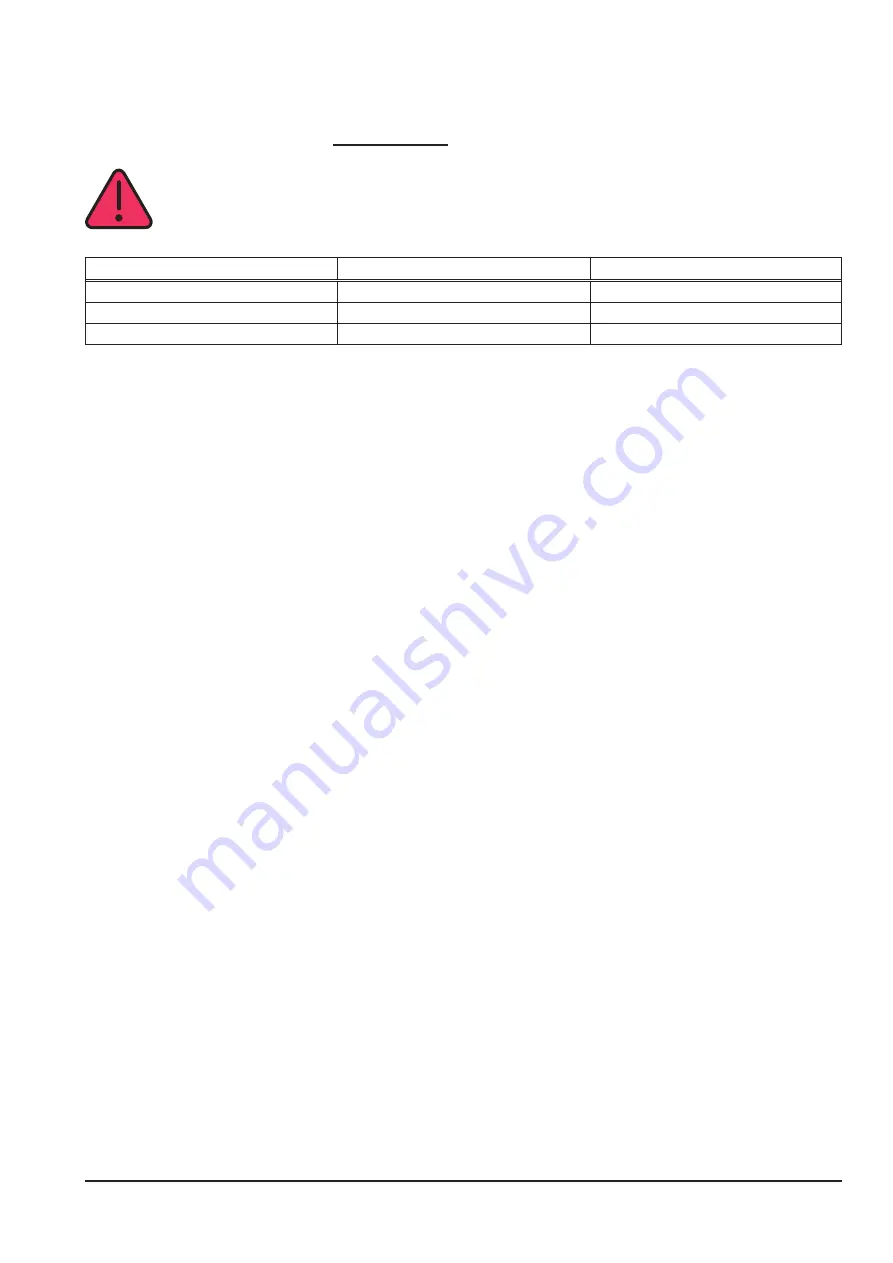
page 27
Change from pc-board DRV0x toe DRV1x
Since week 18 2017 the new DRV boards are used in the MicorMIG series. To ensure the multivoltage function
and generator useage, not only the hard and software of the DRV were changed, also the software of the MAPRO
board (version 2.02 for Master and Process firmware) needed to be changed.
That is why the new DRV boards are
NOT compatible
with the MAPRO software 1.xx.
If a “old” DRV0x board needs to be replaced by a “new” DRV1x board, it is absolutely necessary that
the MAPRO needs to be updated to minimum version 2.02!!!
previous board
replaced by
new part no.
DRV03
DRV13
981.1219.0
DRV05
DRV15
650.5645.5
DRV07
DRV17
650.5647.5
Summary of Contents for MicorMIG 300
Page 1: ...Service Manual MicorMIG 909 2130 1 10 ...
Page 35: ...page 35 ...