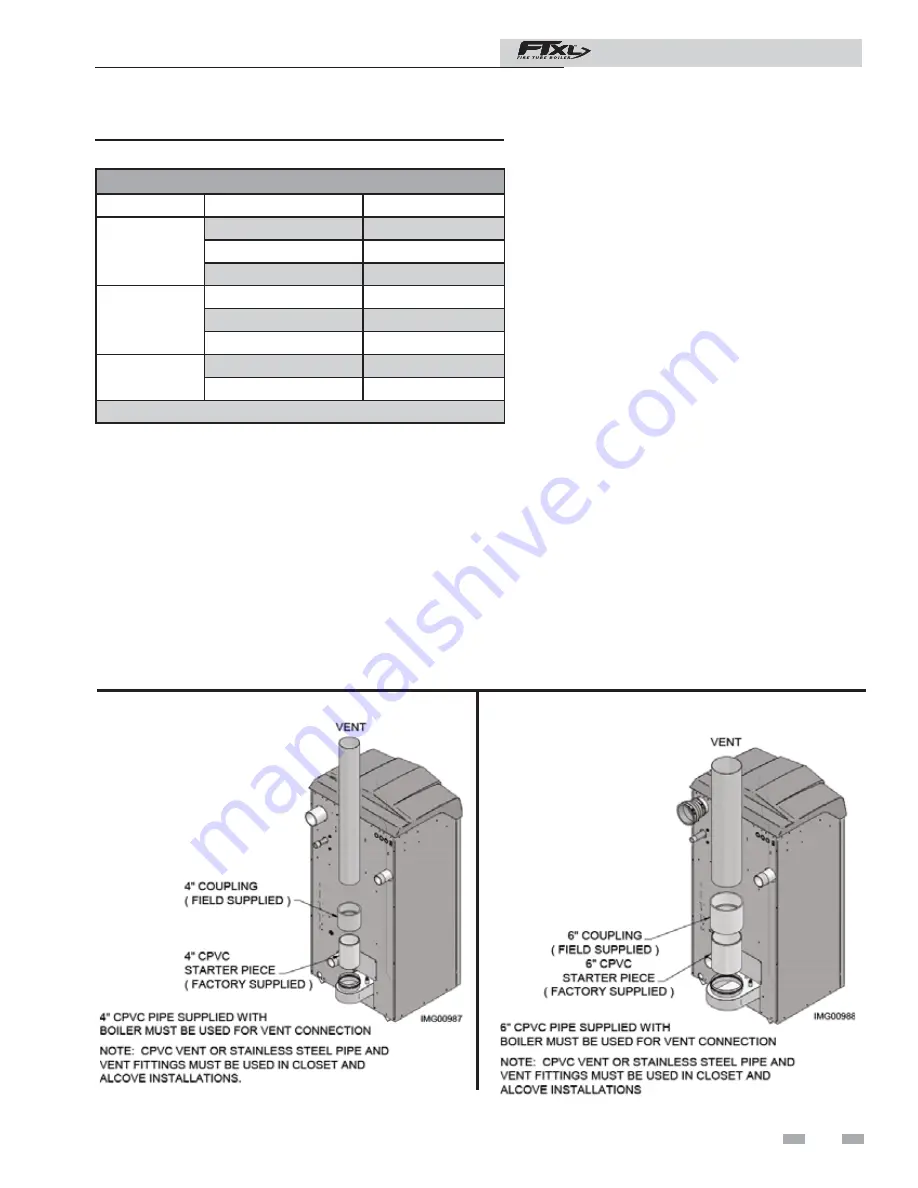
21
3
General
venting
(continued)
5. Dry
fi t vent or air piping to ensure proper fi t up
before assembling any joint. The pipe should go
a third to two-thirds into the fi tting to ensure
proper sealing after cement is applied.
6. Priming
and
Cementing:
a.
Handle
fi ttings and pipes carefully to prevent
contamination
of
surfaces.
b. Apply a liberal even coat of primer to the fi tting
socket and to the pipe end to approximately 1/2"
beyond the socket depth.
c. Apply a second primer coat to the fi tting
socket.
d. While primer is still wet, apply an even coat of
approved cement to the pipe equal to the depth of
the
fi tting socket along with an even coat of
approved cement to the fi tting socket.
e. Apply a second coat of cement to the pipe.
f.
While the cement is still wet, insert the pipe into
the
fi tting, if possible twist the pipe a 1/4 turn as
you
insert
it.
NOTE:
If voids are present,
suffi cient cement was not applied and joint could
be
defective.
g. Wipe excess cement from the joint removing
ring or beads as it will needlessly soften the
pipe.
Table 3E PVC/CPVC Vent Pipe, and Fittings
Approved PVC/CPVC Vent Pipe and Fittings
Item
Material
Standard
Vent pipe
PVC Schedule 40, 80 ANSI/ASTM D1785
PVC - DWV
ANSI/ASTM D2665
CPVC Schedule 40, 80 ANSI/ASTM F441
Vent fi ttings
PVC Schedule 40
ANSI/ASTM D2466
PVC Schedule 80
ANSI/ASTM D2467
CPVC Schedule 80
ANSI/ASTM F439
Pipe Cement /
Primer
PVC
ANSI/ASTM D2564
CPVC
ANSI/ASTM F493
NOTICE: DO NOT USE CELLULAR (FOAM) CORE PIPE
NOTE:
In Canada, CPVC and PVC vent pipe, fi ttings and cement/
primer must be ULC-S636 certifi ed.
1. Work from the boiler to vent or air termination. Do not
exceed the lengths given in this manual for the air or vent
piping.
2. Cut pipe to the required lengths and deburr the inside
and outside of the pipe ends.
3. Chamfer outside of each pipe end to ensure even
cement distribution when joining.
4. Clean all pipe ends and fi ttings using a clean dry rag.
(Moisture will retard curing and dirt or grease will prevent
adhesion.)
Figure 3-3 Near Boiler PVC/CPVC Venting - Models
725 - 850
Figure 3-2 Near Boiler PVC/CPVC Venting - Models 400 - 600
Installation & Operation Manual