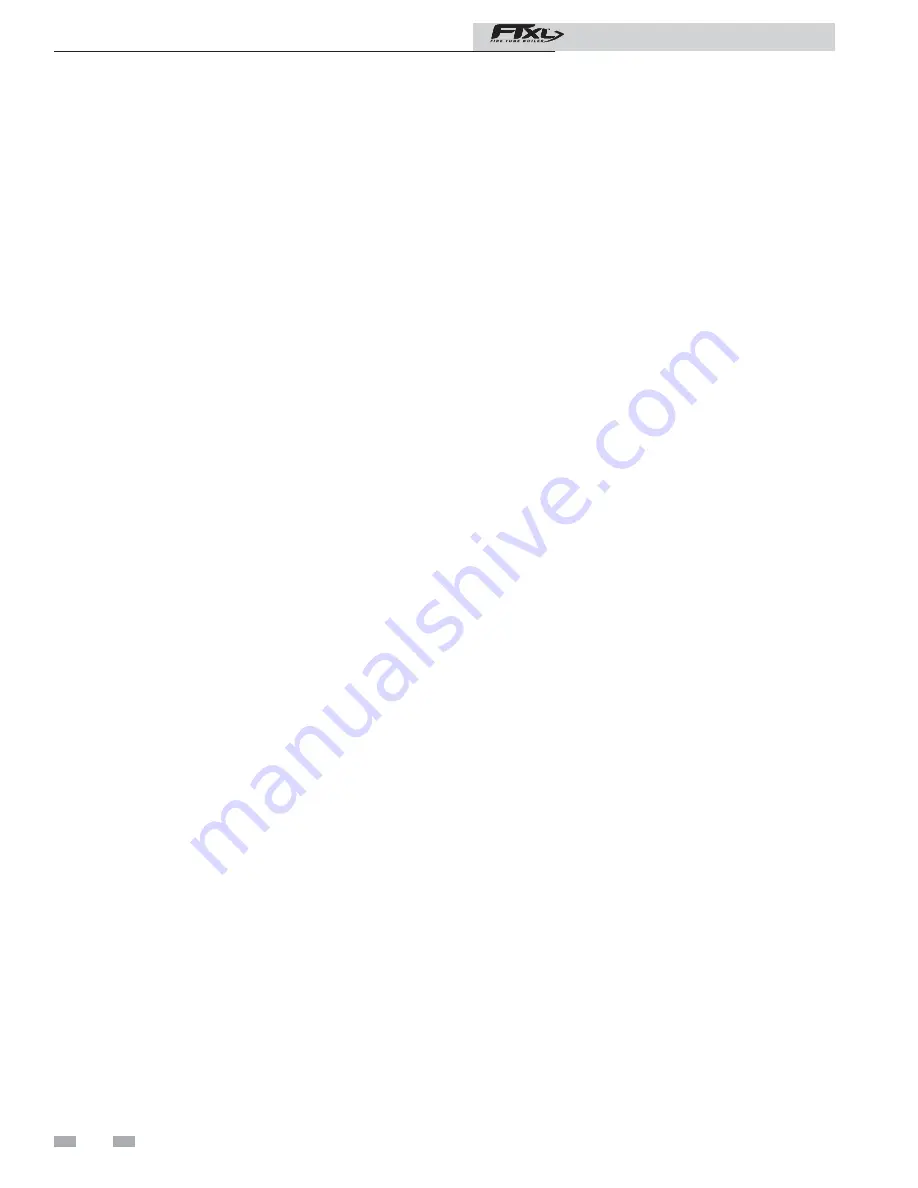
4
The FTXL - How it works...
1. Stainless steel heat exchanger
Allows system water to fl ow around specially designed tubes for
maximum heat transfer, while providing protection against fl ue gas
corrosion.
2. Heat
exchanger
top
plate
Removal of the top plate allows access to the combustion chamber
and tube sheet.
3. Blower
The blower pulls in air and gas through the venturi (item 5). Air
and gas mix inside the blower and are pushed into the burner, where
they burn inside the combustion chamber.
4. Gas
valve
The gas valve senses the negative pressure created by the blower,
allowing gas to fl ow only if the gas valve is powered and combustion
air is fl owing.
5. Venturi
The venturi controls air and gas fl ow into the burner.
6. Flue gas sensor (limit rated)
This sensor monitors the fl ue gas exit temperature. The control
module will modulate and shut down the boiler if the fl ue gas
temperature gets too hot. This protects the fl ue pipe from
overheating.
7. Boiler outlet temperature sensor (limit rated)
This sensor monitors boiler outlet water temperature (system
supply). If selected as the controlling sensor, the control module
adjusts boiler fi ring rate so the outlet temperature is correct.
8. Boiler inlet temperature sensor
This sensor monitors return water temperature (system return). If
`selected as the controlling sensor, the control module adjusts the
boiler
fi ring rate so the inlet temperature is correct.
9. Temperature and pressure gauge (fi eld installed, not
shown)
Monitors the outlet temperature of the boiler as well as the
system water pressure.
10. Electronic LCD display
The display features a high resolution liquid crystal screen, four (4)
buttons, and a navigation dial. A serial and USB port support
additional communication with the control.
11. Flue pipe adapter
Allows for the connection of the PVC vent pipe system to the
boiler.
12. Burner (not shown)
Made with metal fi ber and stainless steel construction, the burner
uses pre-mixed air and gas and provides a wide range of fi ring rates.
13. Water outlet (system supply)
A 2" or 2-1/2" NPT (depending on the model) water connection that
supplies hot water to the system.
14. Water inlet (system return)
A 2" or 2-1/2" NPT (depending on the model) water connection that
returns water from the system to the heat exchanger.
15. Gas connection pipe
Threaded pipe connection of 1". This pipe should be connected to
the incoming gas supply for the purpose of delivering gas to the
boiler.
16. SMART SYSTEM Control Module
The SMART SYSTEM Control responds to internal and external
signals to regulate the blower, gas valve, and pump functions to meet
heating demand. An optional remote connectivity allows boiler
settings to be monitored and modifi ed when connected to the
internet.
17. Manual air vent
A manual air vent is used to remove trapped air from the heat
exchanger
shell.
18. Air intake adapter
Allows for the connection of the PVC air intake pipe to the boiler.
19. High voltage junction box
The junction box contains the connection points for the line voltage
power and all pumps.
20. Boiler drain connection
A 1" NPT drain connection is provided for easy access in the
event the boiler needs to be drained .
21. Low voltage connection board
The connection board provides easy access for connecting
external low voltage devices.
22. Low voltage wiring connections (knockouts)
Conduit connection points for the low voltage connection
board.
23. Condensate trap
The condensate trap is sized for a 1" PVC outlet connection
pipe.
24. Bezel (hinged)
Provides access to the gas train, heat exchanger, and display.
25. Ignition electrode
Provides direct spark for igniting the burner.
26. Flame inspection window
The quartz glass window provides a view of the burner surface
and
fl ame.
27. Gas shutoff valve (Models 500 - 850 only)
A manual valve is provided to isolate the gas valve from the
boiler.
28. Relief valve (fi eld installed, not shown)
Protects the heat exchanger from an over pressure condition.
The relief valve provided with the unit is set at 50 PSI.
29. Flame sensor
Used by the control module to detect the presence of burner
fl ame.
30. Line voltage wiring connections (knockouts)
Conduit connection points for the high voltage junction box.
31. Front panel
Removable panel to gain access to the internal components.
32. Power switch
Turns 120 VAC ON/OFF to the boiler.
33. Pump relay board
The pump relay board is used to connect the boiler, system and
DHW
pumps.
34.
Transformer
The transformer provides 24V power to the integrated control.
35.
High limit sensor (housed with the outlet temperature
sensor)
Device that monitors the outlet water temperature. If the
temperature exceeds its setting, the integrated control will break
the control circuit, shutting the boiler down.
36.
Low water cutoff probe (LWCO)
Protects the heat exchanger from overheating, by ensuring
adequate water is supplied to the boiler. In the event of
inadequate water levels, the boiler will shut down.
37.
Stainless steel fl ue collector
Flue gas and condensate enter the stainless steel fl ue collector
through the fi retubes. A 1" drain connection allows condensate
to
fl ow through the collector into a condensate trap for
disposal.
38.
Reset switch
Reset switch for the low water cutoff. Hold the switch for 10
seconds to reset.
39.
Test switch
The test switch permits manual triggering of the LWCO safety
circuit to test the contacts and evaluate the integrity of the
circuit. Hold the switch for 10 seconds to test.
40.
Combustion measurement port
A port near the fl ue vent which provides access for a combustion
analyzer
probe.
41.
Burner plate (not shown)
The burner plate attaches the blower to the burner and the heat
exchanger. Removal allows easy access to the burner for
inspection or replacement.
Installation & Operation Manual