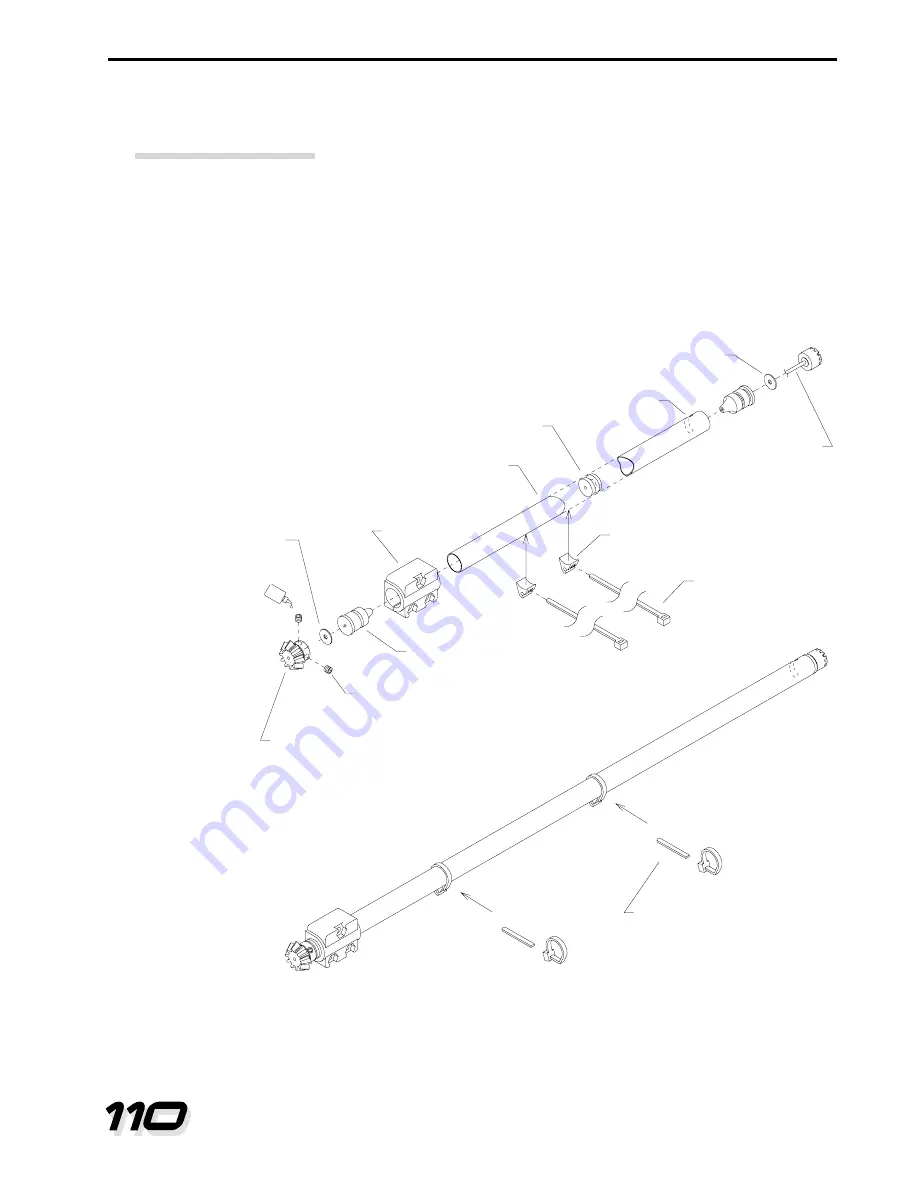
T
ail Boom
The tail boom on the
Model 110
helicopter is an aluminum tube that extends rearward
from the body, and terminates in the tail rotor assembly. A wire drive shaft runs down
the length of the tail boom, and transmits power from the main rotor shaft to the tail
rotor and
Arlton Gyro
stabilizer. The tail rotor incorporates specially designed, high
efficiency swept rotor blades (patented) which greatly reduce the mechanical
complexity and power consumption of the tail rotor.
Construction Manual
Tail Boom
LITE MACHINES
10-1
#1 teflon washer
#1 teflon washer
Slot
Center bushing
Tail boom
Tail mounting
bracket
Threadlock
Front pinion gear
6-32 x 3/16”
setscrew
End bushing
Nytie
Pushrod guide
Tail rotor
drive wire
Back end
Cut excess
Front end
Figure 10-1.