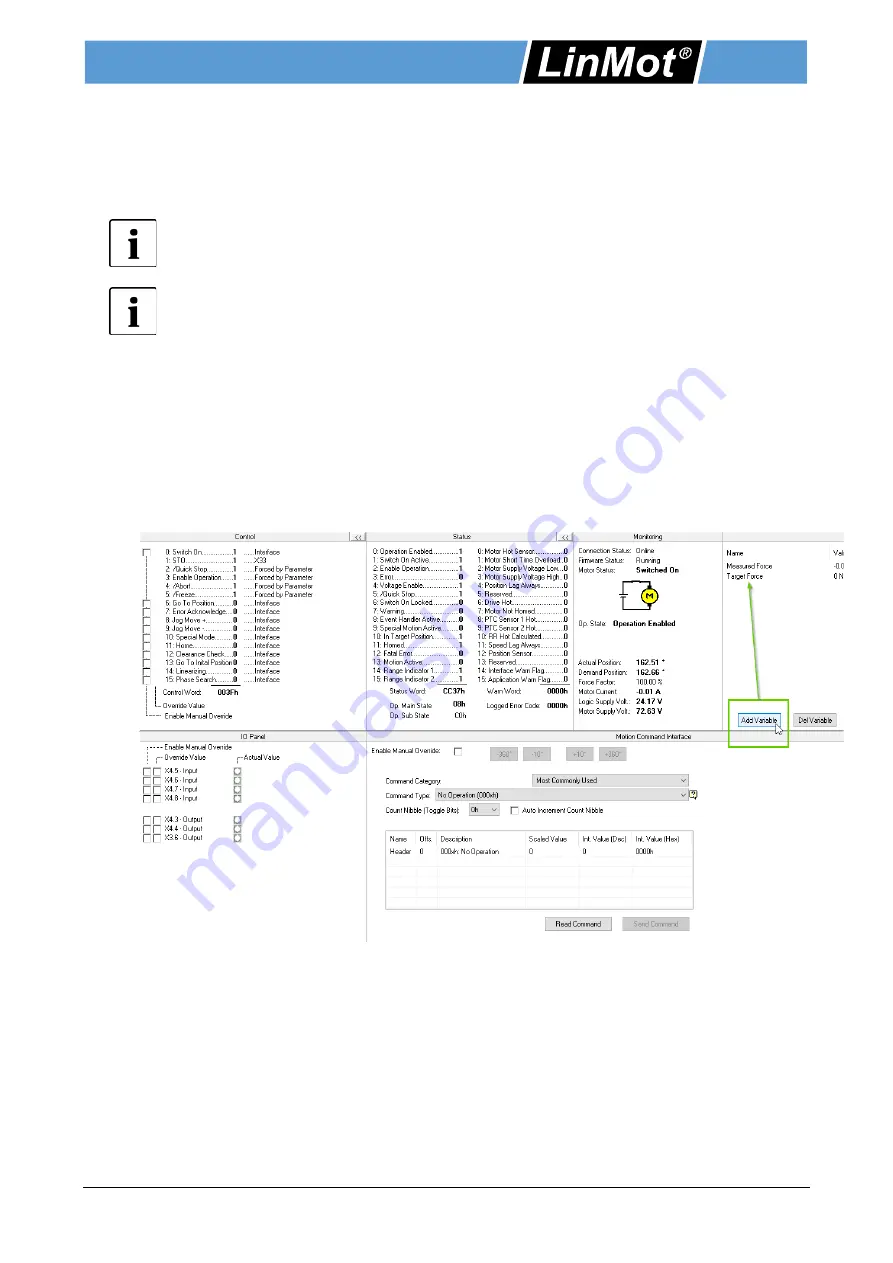
Installation Guide Linear Rotary Motors
ENG
NTI AG / LinMot
PR02-38
Page 27 / 39
Parameter tree: Force Control Parameters
The parameters for the torque/force control loop are set here. A PID controller, a few feed forward
parameters (FF parameters) and a parameter for limiting the maximum control current (Force Ctrl Max
Current) are available for this purpose.
Recommendation:
To begin with, work with a pure I-controller to prevent the motor from oscillating during torque
control.
Limit the maximum control current in order to avoid damage if incorrect handling occurs
during commissioning.
6.8.3 Initial Test of a Torque Measuring Shaft / Force Sensor
It’s recommended to proceed an initial test of a sensor using the LinMot-Talk Variable before entering
operational state.
1. Log into the drive using LinMot-Talk software and open the control panel.
2. Switch on the motor (e.g. rotary motor) using the ControlWord (Switch On). The motor will stay within
position control mode.
3.
Using the button “Add Variable” add the variables “Target Force” and “Measured Force” (MC SW
Force Control).