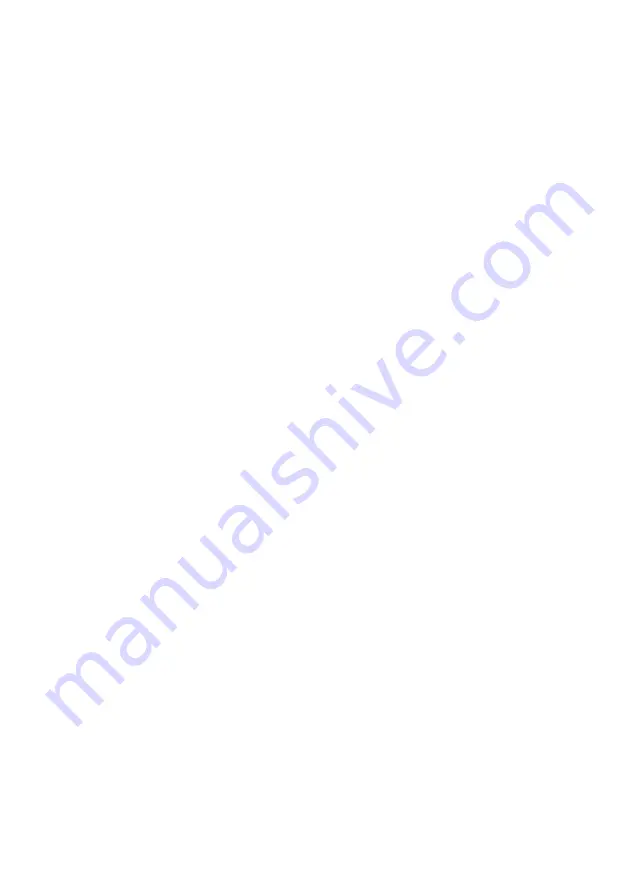
16
6.2 Introduction to Flux Cored Arc
Welding (FCAW)
How it Works
Flux-cored arc welding (FCAW) uses the heat
generated by a DC electric arc to fuse the metal
in the joint area, the arc being struck between a
continuously fed consumable filler wire and the
workpiece, melting both the filler wire and the
workpiece in the immediate vicinity. The entire arc
area is covered by a shielding gas, which protects
the molten weld pool from the atmosphere.
FCAW is a variant of the MIG/MAG process and
while there are many common features between
the two processes, there are also several
fundamental differences.
As with MIG/MAG, direct current power sources
with constant voltage output characteristics are
normally employed to supply the welding current.
With flux-cored wires the terminal that the filler
wire is connected to depends on the specific
product being used, some wires running electrode
positive, others running electrode negative. The
work return is then connected to the opposite
terminal. It has also been found that the output
characteristics of the power source can have an
effect on the quality of the welds produced.
The wire feed unit takes the filler wire from a
spool, and feeds it through the welding torch,
to the arc at a predetermined and accurately
controlled speed. Normally, special knurled feed
rolls are used with flux-cored wires to assist
feeding and to prevent crushing the consumable.
Unlike MIG/MAG, which uses a solid consumable
filler wire, the consumable used in FCAW is of
tubular construction, an outer metal sheath being
filled with fluxing agents plus metal powder.
The flux fill is also used to provide alloying, arc
stability, slag cover, de-oxidation, and, with some
wires, gas shielding.
In terms of gas shielding, there are two different
ways in which this may be achieved with the FCAW
process.
•
Additional gas-shielding supplied from an
external source, such as a gas cylinder
•
Production of a shielding gas by decomposition
of fluxing agents within the wire, self-shielding
Gas shielded wires are available with either a basic
or rutile flux fill, while self-shielded wires have a
broadly basic-type flux fill. The flux fill dictates the
way the wire performs, the properties obtainable,
and suitable applications.
Gas-shielded Operation
Many cored wire consumables require an auxiliary
gas shield in the same way that solid wire MIG/
MAG consumables do. These types of wire are
generally referred to as ‘gas-shielded’.
Using an auxiliary gas shield enables the wire
designer to concentrate on the performance
characteristics, process tolerance, positional
capabilities, and mechanical properties of
the products.
In a flux cored wire the metal sheath is generally
thinner than that of a self-shielded wire. The area
of this metal sheath surrounding the flux cored
wire is much smaller than that of a solid MIG/MAG
wire. This means that the electrical resistance
within the flux cored wire is higher than with solid
MIG/MAG wires and it is this higher electrical
resistance that gives this type of wire some of its
novel operating properties.
One often quoted property of fluxed cored wires
are their higher deposition rates than solid MIG/
MAG wires. What is often not explained is how they
deliver these higher values and whether these
can be utilised. For example, if a solid MIG/MAG
wire is used at 250 amps, then exchanged for a
flux cored wire of the same diameter, and welding
power source controls are left unchanged, then
the current reading would be much less than 250
amps, perhaps as low as 220 amps. This is because
Summary of Contents for BOC RAPTOR 160 MIG
Page 31: ......