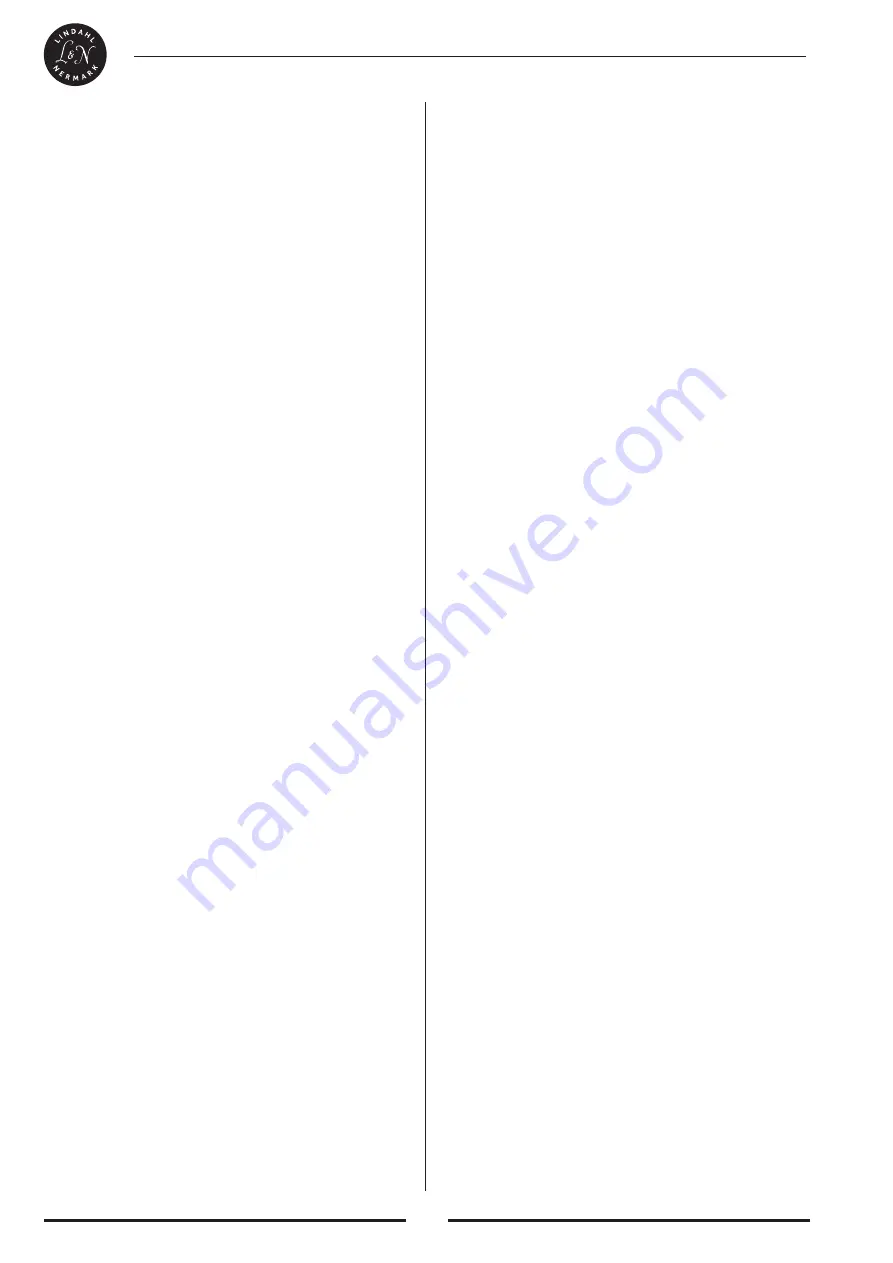
12
MAIN STRUCTURE
1. MOTOR is insulation of class B with motor frame being made
by aluminium or iron casting.
2. WHEEL COVER is made of steel plate. It is used to prevent
splashing of sparks and to connect eyeprotectors.
3. GRINDING WHEELS
4. SWITCH
5. PLUG & WIRE is of three wicks with one is ground wire.
6. CAPACITOR
PRECAUTIONS ON USING BENCH GRINDERS
1. Disconnect power supply plug before replacing wheels or
covers.
2. Replace cracked or damaged wheels immediately.
3. Always use guards and eyeshields.
4. Ensure tool rests and eyeshields are properly adjusted.
5. Do not over tighten wheel nut.
6. Adjust distance between wheel and tool rest to maintain 1/6”
(1.6 mm) or less separation as the diameter of the wheel decre-
ases with use.
7. Use grinding wheel suitable for the speed of the grinder.
8. Ensure grinding wheels rotate freely before switching on
power.
9. Stand beside the bench grinder when switching on the power,
do not stand in front of the grinder.
10. Allow a new grinding wheel to rotate for one minute prior to
use to ensure it is in good condition.
11. Don’t operate the grinder with the wheel guard off.
12. Don’t use the grinding wheels for cutting purposes.
13. Do not overload the grinder.
14. Use a wheel dresser to remove burrs from the grinding wheel.
15. Maintain a distance brtween the spark breaker and the grinding
wheel of less than 1/16” (1.6 mm).
ASSEMBLY
Assemble the eyeshielAds, spark breakers and tool rests using the
screws, etc. provided. Be sure to position both the tool rests and
spark breakers no more than 1.6 mm (1/6”) from the edge of the
grinding wheel.
OPERATION
1. After switching the grider on allow it to reach full speed before
commencing grinding operation.
2. The eyeshields are able to be adjusted and should be positioned
to allow the operator a clear view of the work through the shi-
elds.
3. The appropriate adjustments fo the tool rests will provide the
correct working angle for effieient grinding. As the diameter fo
the grinding wheel is subject to wear, it will be necessary to re-
adjust the tool rests positions to maintain the correct gap of less
than 1.6 mm (1/6”) with the edge of the grinding wheel.
REMOVING OR CHANING THE GRINDING
WHEELS
To renew or change the grinding wheels, follow this series of
steps:
(a) Disconnect the power supply cord.
(b) Remove the outside covers, left and right.
(c) Holding the grinding wheel firmly, remove the nut and flange
from the shaft with a spanner.
Note that the left wheel nut has a left hand thread and the right
wheel nut has a right hand thread.
(d) Remove the old wheel and replace it with the new wheel.
(e) Reassemble the flange, nut and outside covers.
(f) Allow the grinder to run for one minute to ensure the grinding
wheel is not out of balance before commencing any grinding
work.
Summary of Contents for 20181-0116
Page 1: ...B nkslipmaskin Bench grinder LSG 150 H LSG 200 H LSG 250 H 20181 0215 20181 0116 20181 0413...
Page 2: ......
Page 6: ......
Page 25: ...21 LSG 150 H LSG 200 H...
Page 26: ...22 LSG 250 H...
Page 27: ...23 LSG 150 Hexploded diagram...
Page 29: ...25 LSG 200 Hexploded diagram...
Page 31: ...27 LSG 250 Hexploded diagram...
Page 35: ......