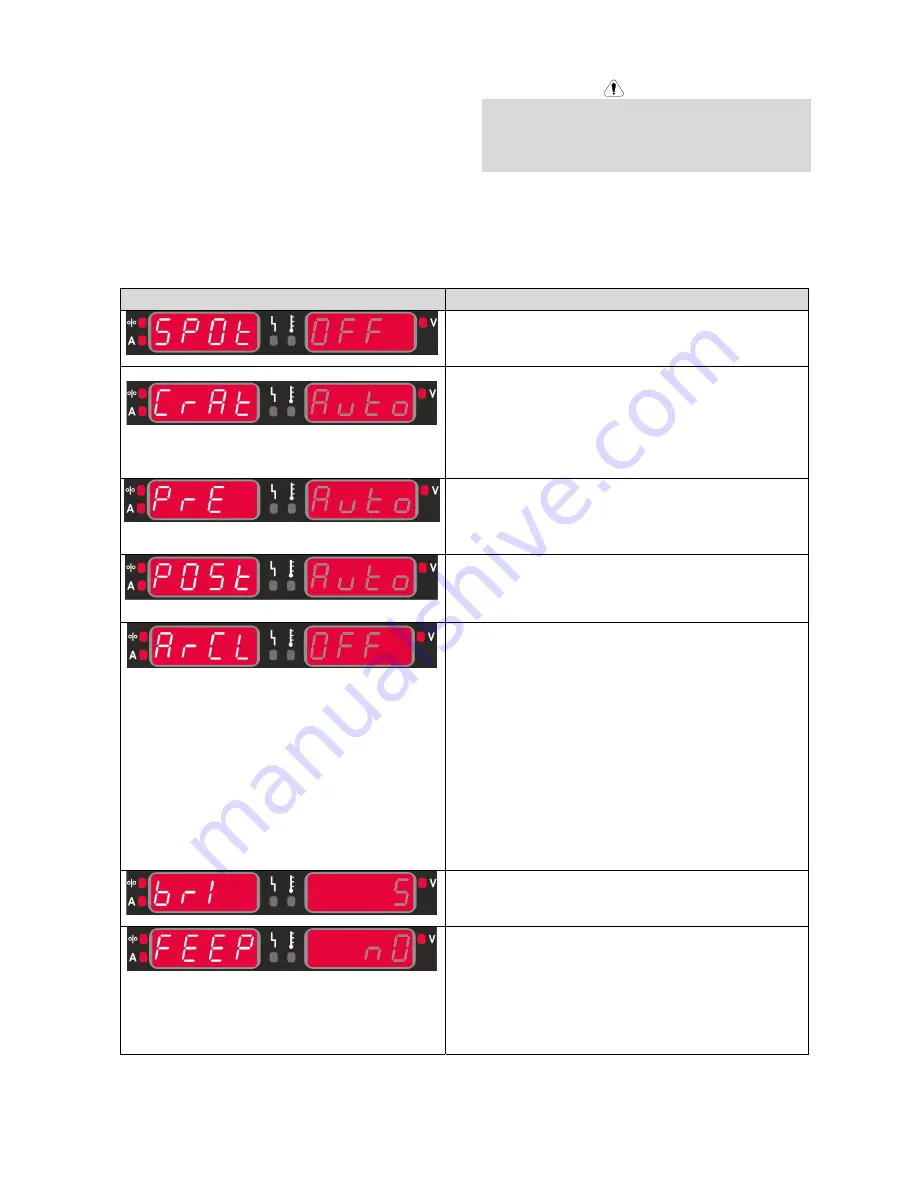
English 9 English
Configuration Menu:
To set the parameter of Confguration Menu:
Press the Left Button [26] and the Right Button [25]
simultaneously to get the access of menu.
Turn the Left Knob [23] to choose the parameter.
Press the Right Button [25] to confirm the selection.
Turn the Right Knob [24] to choose the value of
parameter.
Press the Right Button [25] to confirm the selection.
Press the Left Button [26] to back to the previous
menu and confirm the chosen value.
WARNING
To exit the menu with changes saved, press the Left [26]
and the Right [25] Buttons simultaneously.
After one minute of inactivity the Menu without saving will
also exit.
Table 4. The default settings of Configuration Menu
Parameter
Definition
Spot Timer
– adjusts the time welding will continue even if the
trigger is still pulled. This option has no effect in 4-Step Trigger
Mode.
Crater Procedure
– turn ON/OFF the Crater Settings
Procedure:
ON (factory default) – Crater can be adjusted. The Crater
Settings Procedure is assigned to the Right Button. During
adjusting Crater, the LED Indicator [25] lights.
OFF – The Crater Settings Procedure is OFF. After press the
Right Button, The Crater Settings Procedure is ignored.
Preflow Time
– adjusts the time that shielding gas flows after
the trigger is pulled and prior to feeding.
Factory default, Preflow Time is set at 0 seconds.
Adjust range: from 0,1 seconds to 25 seconds.
Postflow Time
– adjusts the time that shielding gas flows after
the welding output turns off.
Factory default, Postflow Time is set at 0 seconds.
Adjust range: from 0,1 seconds to 25 seconds.
Arc/Loss Time
– this option can be used to optionally shut off
output if an arc is not established, or is lost for a specified
amount of time. Error 269 will be displayed if the machine times
out. If the value is set to OFF, machine output will not be turned
off if an arc is not established nor will output be turned off if an
arc is lost. The trigger can be used to hot feed the wire
(default). If a value is set, the machine output will shut off if an
arc is not established within the specified amount of time after
the trigger is pulled or if the trigger remains pulled after an arc
is lost. To prevent nuisance errors, set Arc Start/Loss Error
Time to an appropriate value after considering all welding
parameters (run-in wire feed speed, weld wire feed speed,
electrical stick out, etc).
OFF (0) to 10 seconds (default = Off)
Note:
This parameter is disabled while welding in Stick, TIG or
Gouge.
Screen Brightness
– enables setting the displays brightness
level. Adjust range from 1 to 10, where 5 is default.
Feedback Persist
– determines how feedback values are
displayed following a weld:
"Off" (factory default) – last recorded feedback values will
blink for 5 seconds following a weld, then return to present
display mode.
"On" – last recorded feedback values will blink indefinitely
following a weld until a Control or button is touched, or an
arc is struck.