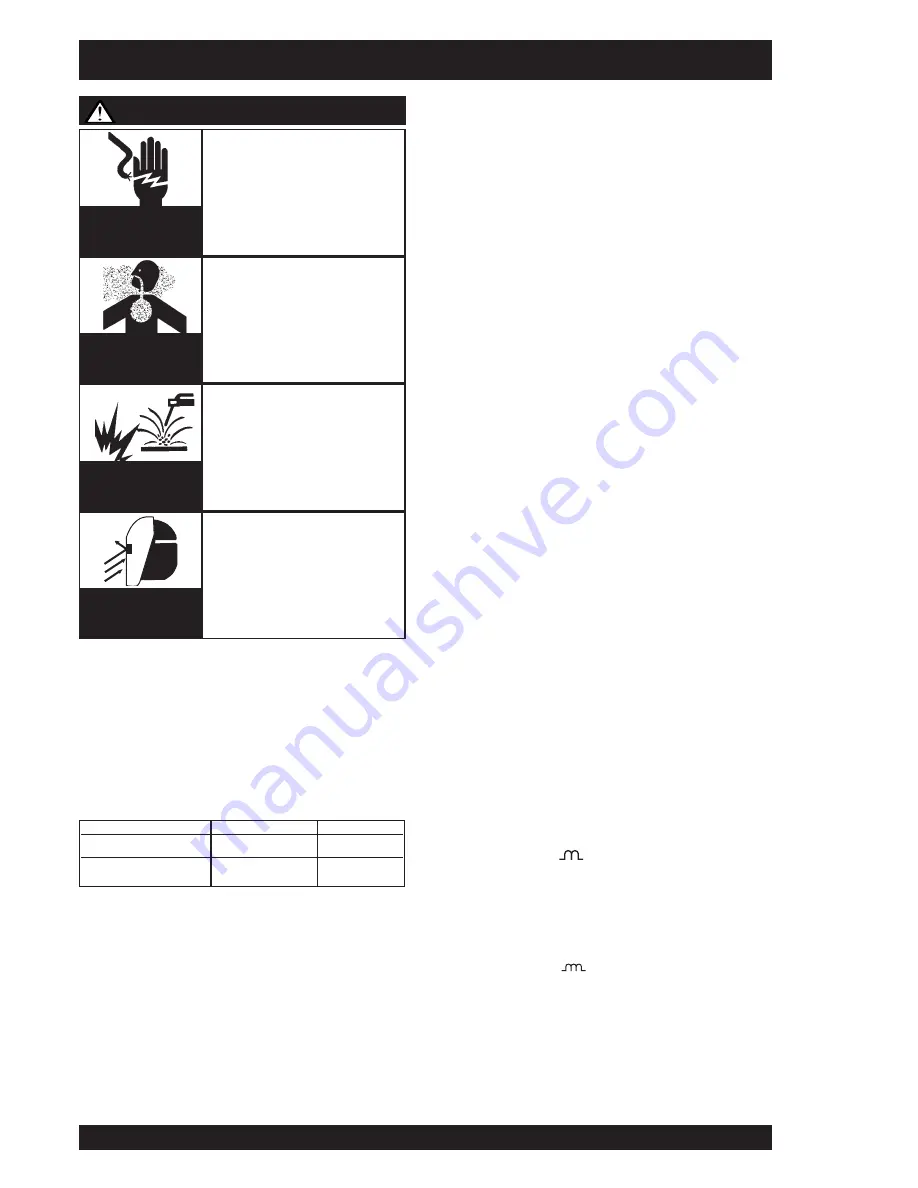
Page 10
REDI-MIG 455 Remote
IMA 603
2.1 Duty Cycle
The machine is rated at the following duty cycles:
(1)
Based on 10 min. time period (i.e., for 60% duty cycle, it is
6 minutes actual welding and 4 minutes with no welding
output, but with the input power remaining on keeping the
cooling fan operative.)
2.2 Control Panel
a)
Power Switch
The mains power switch is a two position toggle switch and
is marked “POWER”. When the toggle switch is pressed
downwards to the “O” position the input mains power is
switched off.
b)
Pilot Light
This light illuminates when the input mains power is
switched on.
c)
Volts Control
The output voltage is controlled by two rotary switches.
One rotary switch provides three “course” voltage settings.
The other rotary switch provides the user with a selection
of ten fine voltage settings. The selection between these
two rotary switches allows the user to select any one of
thirty welding voltages.
The Coarse Voltage rotary switch is marked with the three
coarse ranges A, B and C.
A) is the low range which supplies voltage from 16 to
18.5V.
B) is the medium range which supplies voltage from 18.5
to 24V.
C) is the high range which supplies voltage from 24 to
36.5V.
The fine voltage rotary switch is marked with the ten
welding voltages a, b, c, d, e, f, g, h, i and j.
d)
Wire Feed Speed Control *
Use this control to adjust the speed at which the electrode
wire feeds when welding. This is in effect a current control
as the power source will deliver the current necessary to
melt the wire. The higher the speed, the more current will
be required. Wire feed speed range is approximately 1 to
20 meters/min (40 to 790 inches/min.).
Operation of the gun trigger switches the wire feed motor
on and off, depending upon the trigger mode setting. The
wire feed motor is dynamically braked to minimise wire
overrun after welding has ceased.
Welding voltage is available immediately the gun trigger is
operated. When welding is stopped there is a delay to allow
the electrode to burn back slightly and prevent sticking in
the crater. [See Burnback Control 2.2 f)]
e)
Inductance Settings
The inductance can be changed by changing the position
of the negative output connection. The negative output
connection closest to the side panel work is the High
Inductance Negative Output Connection.
The High Inductance Negative Output Connection is
symbolised by “ “.
The High Inductance Negative Output Connection is more
suitable when a soft arc is preferred.
The negative output connection furthest from the side
panel work is the Low Inductance Negative Output
Connection.
The Low Inductance Negative Output Connection is
symbolised by “ “.
The Low Inductance Negative Output Connection is more
suitable when a crisp arc is preferred.
WARNING
ELECTRIC
SHOCK
can kill
FUMES AND
GASES can be
dangerous
WELDING SPARKS
can cause fire or
explosion
ARC RAYS
can burn
• Do not touch electrically live
parts or electrode with skin or
wet clothing.
• Insulate yourself from work and
ground.
• Always wear dry insulating
gloves.
• Keep your head out of fumes.
• Use ventilation or exhaust to
remove fumes from breathing
zone.
• Keep flammable material away.
• Do not weld upon containers
which have held combustibles.
• Wear eye, ear and body
protection.
IMPORTANT SAFETY NOTE: In 2T mode {refer 2.2 (i)}, this DC
Constant Voltage wire welder provides “COLD” electrode when
the gun trigger is not operated. Conversely, the output terminals
are “LIVE” when the gun trigger is “activated” when pressed in 2T
mode, or triggered on in 4T mode.
Section 2 - OPERATING INSTRUCTIONS
Duty Cycle
(1)
Amps
Volts
35%
455
36.5
60%
350
31.5