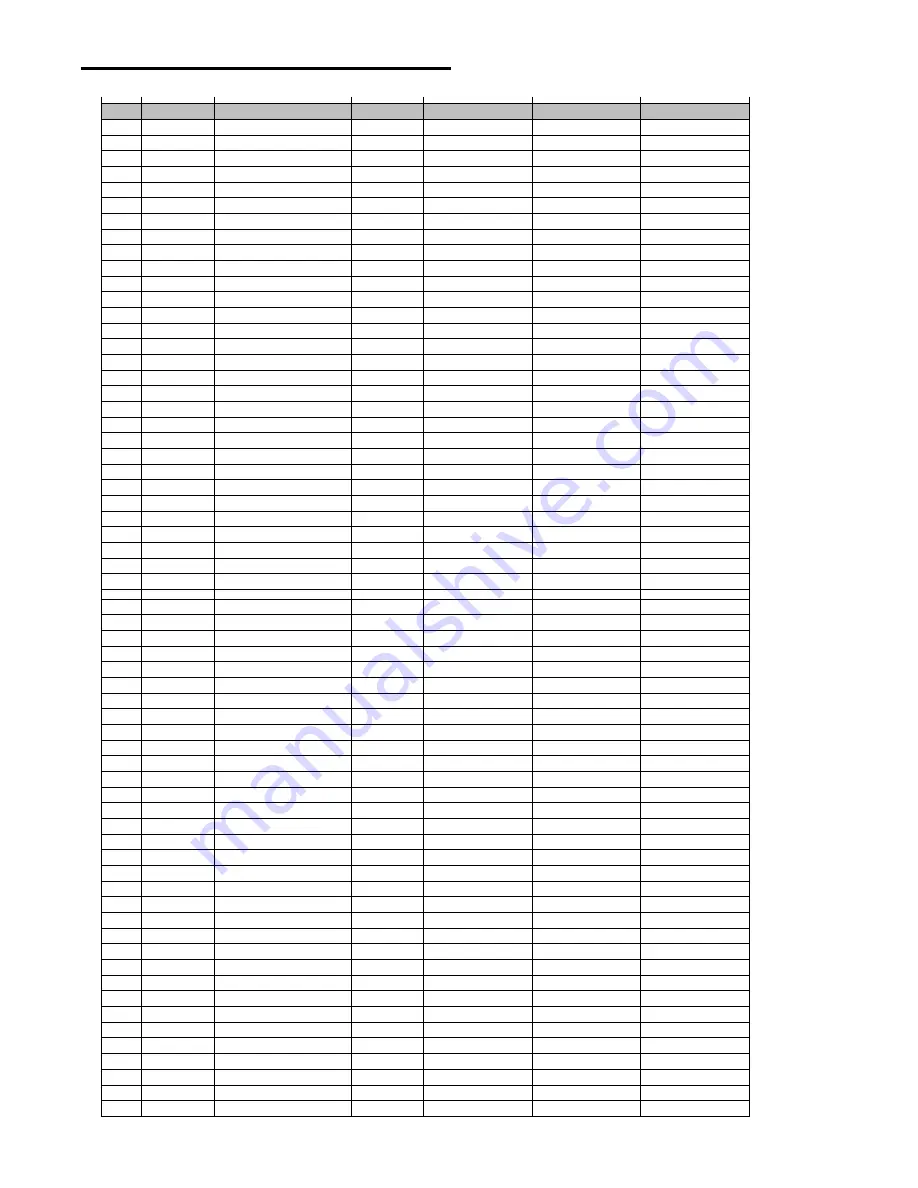
E-
1
LIST OF LEGACY WELD MODES
Mode
Process
Procedure
Wire Size
Wire Type
Gas Type
ArcControl
1
SMAW
Stick General Purpose
Arc Force
2
SMAW
Stick Crisp
Arc Force
3
GTAW
Touch Start TIG
5
GMAW
CV MIG
Pinch
6
FCAW-S
CV Flux Core Self Shield
Pinch
7
FCAW-G
CV Flux Core Gas Shield
Pinch
8
GTAW
TIG Pulse (0.5 - 20 Hz)
Frequency
9
GTAW
TIG Pulse (20-300 Hz)
Frequency
10
GMAW
CV
.035in
Steel
CO2
Pinch
11
GMAW
CV
.035in
Steel
Argon Blends
Pinch
14
GMAW
Pulse
.035in
Steel
Argon Blends
Arc Control
16
GMAW
Vertical Up Pulse
.035in
Steel
Argon Blends
Frequency Offset
19
GMAW
Pulse
.045in
Steel
Argon Blends
Arc Control
20
GMAW
CV
.045in
Steel
CO2
Pinch
21
GMAW
CV
.045in
Steel
Argon Blends
Pinch
23
GMAW
Vertical Up Pulse
.045in
Steel
Argon Blends
Frequency Offset
28
GMAW
CV
.025in
Steel
CO2
Pinch
29
GMAW
CV
.025in
Steel
Argon Blends
Pinch
30
GMAW
Pulse
.025in
Steel
Argon Blends
Arc Control
31
GMAW
CV
.035in
Stainless
Pinch
32
GMAW
Pulse
.035in
Stainless
Arc Control
33
GMAW
CV
.035in
Stainless
He Ar CO2
Pinch
34
GMAW
Pulse
.035in
Stainless
He Ar CO2
Arc Control
38
GMAW
Vertical Up Pulse
.035in
Stainless
Frequency Offset
40
GMAW
Power Mode
®
(Non Syn)
Gas Shield
Pinch
41
GMAW
CV
.045in
Stainless
Pinch
42
GMAW
Pulse
.045in
Stainless
Arc Control
43
GMAW
CV
.045in
Stainless
He Ar CO2
Pinch
44
GMAW
Pulse
.045in
Stainless
He Ar CO2
Arc Control
48
Frequency Offset
61
GMAW
CV
.030in
Stainless
Pinch
62
GMAW
Pulse
.030in
Stainless
Arc Control
63
GMAW
CV
.030in
Stainless
He Ar CO2
Pinch
64
GMAW
Pulse
.030in
Stainless
He Ar CO2
Arc Control
71
GMAW
CV
3/64in
Aluminum 4043
Argon
Pinch
72
GMAW
Pulse
3/64in
Aluminum 4043
Argon
Arc Control
75
GMAW
CV
3/64in
Aluminum 5356
Argon
Pinch
76
GMAW
Pulse
3/64in
Aluminum 5356
Argon
Arc Control
81
GMAW
CV
.045in
Metal Core
Argon Blends
Pinch
82
GMAW
Pulse
.045in
Metal Core
Argon Blends
Arc Control
83
GMAW
CV
.052in
Metal Core
Argon Blends
Pinch
84
GMAW
Pulse
.052in
Metal Core
Argon Blends
Arc Control
85
GMAW
CV
1/16in
Metal Core
Argon Blends
Pinch
86
GMAW
Pulse
1/16in
Metal Core
Argon Blends
Arc Control
93
GMAW
CV
.030in
Steel
CO2
Pinch
94
GMAW
CV
.030in
Steel
Argon Blends
Pinch
95
GMAW
Pulse
.030in
Steel
Argon Blends
Arc Control
97
GMAW
Pulse On Pulse
.030in
Aluminum 4043
Argon
Modulation Freq
98
GMAW
Pulse On Pulse
.035in
Aluminum 4043
Argon
Modulation Freq
99
GMAW
Pulse On Pulse
3/64in
Aluminum 4043
Argon
Modulation Freq
101
GMAW
Pulse On Pulse
.035in
Aluminum 5356
Argon
Modulation Freq
102
GMAW
Pulse On Pulse
3/64in
Aluminum 5356
Argon
Modulation Freq
138
GMAW
CV
.040in
Steel
CO2
Pinch
140
GMAW
Pulse
.040in
Steel
Argon Blends
Arc Control
146
GMAW
CV
.030in
Aluminum 4043
Argon
Pinch
147
GMAW
Pulse
.030in
Aluminum 4043
Argon
Arc Control
148
GMAW
CV
.035in
Aluminum 4043
Argon
Pinch
149
GMAW
Pulse
.035in
Aluminum 4043
Argon
Arc Control
151
GMAW
CV
.035in
Aluminum 5356
Argon
Pinch
152
GMAW
Pulse
.035in
Aluminum 5356
Argon
Arc Control
190
GMAW
Pulse
.030in
Si Bronze
Argon
Arc Control
191
GMAW
Pulse
.045in
Si Bronze
Argon
Arc Control
192
GMAW
Pulse
.035in
Si Bronze
Argon
Arc Control
196
GMAW
Pulse
.045in
Copper
75He/25Ar
Arc Control
Argon Blends
Argon Blends
Argon Blends
Argon Blends
Stainless
.045in
Vertical Up Pulse
GMAW
Argon Blends
Argon Blends
Argon Blends
Argon Blends