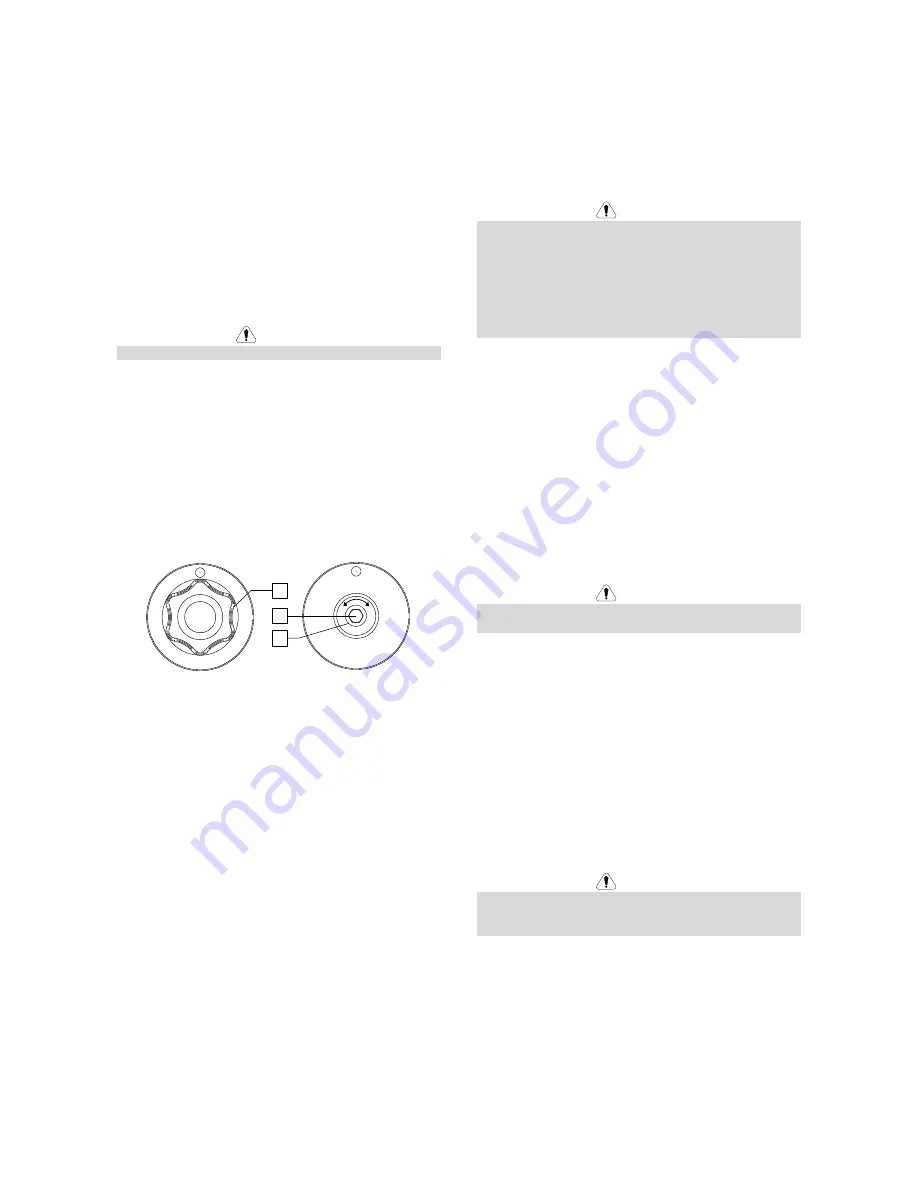
English
English
15
Loading the Electrode Wire
Turn the input power OFF.
Open the spool wire case.
Unscrew the locking nut of the sleeve.
Load the spooled wire on the sleeve such that the
spool turns clockwise when the wire is fed into the
wire feeder.
Make sure that the spindle brake pin [38] goes into
the fitting hole on the spool.
Screw in the locking nut of the sleeve.
Open the wire drive door.
Put on the wire roll using the correct groove
corresponding to the wire diameter.
Free the end of the wire and cut off the bent end
making sure it has no burr.
WARNING
Sharp end of the wire can hurt.
Rotate the wire spool clockwise and thread the end
of the wire into the wire feeder as far as the Euro
Socket.
Adjust force of pressure roll of the wire feeder
properly.
Adjustments of Brake Torque of Sleeve
To avoid spontaneous unrolling of the welding wire the
sleeve is fitted with a brake.
Adjustment is carried by rotation of its screw M10, which
is placed inside of the sleeve frame after unscrewing the
locking nut of the sleeve.
35
51
52
Figure 27.
35. Locking Nut.
51. Adjusting Screw M10.
52. Pressing Spring.
Turning the screw M10 clockwise increases the spring
tension and you can increase the brake torque
Turning the screw M10 anticlockwise decreases the
spring tension and you can decrease the brake torque.
After finishing of adjustment, you should screw in the
locking nut again.
Adjusting Pressure Roll Force
The pressure arm controls the amount of force the drive
rolls exert on the wire.
Pressure force is adjusted by turning the adjustment nut
clockwise to increase force, counterclockwise to
decrease force. Proper adjustment of pressure arm
gives the best welding performance.
WARNING
If the roll pressure is too low the roll will slide on the wire.
If the roll pressure is set too high the wire may be
deformed, which will cause feeding problems in the
welding gun. The pressure force should be set properly.
Decrease the pressure force slowly until the wire just
begins to slide on the drive roll and then increase the
force slightly by turning of the adjustment nut by one
turn.
Inserting Electrode Wire into Welding
Gun
Turn the input power OFF.
Depending on welding process, connect the proper
gun to the Euro Socket, the rated parameters of the
gun and of the welding machine should be matched.
Remote the nozzle from the gun and contact tip or
protection cap and contact tip. Next, straighten the
gun out flat.
Insert the wire through the guide tube, over the roller
and through the guide tube of Euro Socket into liner
of gun. The wire can be pushed into the liner
manually for a few centimetres, and should feed
easily and without any force.
WARNING
If force is required it is likely that the wire has missed the
liner of gun.
Turn the input power ON.
Depress the gun trigger to feed the wire through the
gun liner until the wire comes out of the threaded
end. Or the Cold Inch / Gas Purge Switch [12] can be
used – keep in "Cold Inch" position until the wire
comes out of the threaded end.
When trigger or the Cold Inch / Gas Purge Switch
[13] is released spool of wire should not unwind.
Adjust wire spool brake accordingly.
Turn the welding machine off.
Install a proper contact tip.
Depending on the welding process and the type of
the gun, install the nozzle (GMAW process, FCAW-
GS process) or protection cap (FCAW-SS process).
WARNING
Take precaution to keep eyes and hands away from the
end of the gun while the wire is being come out of the
threated end.
Summary of Contents for PF41
Page 23: ...English English 20 Connection Diagram ...
Page 24: ...English English 21 ...
Page 25: ...English English 22 ...