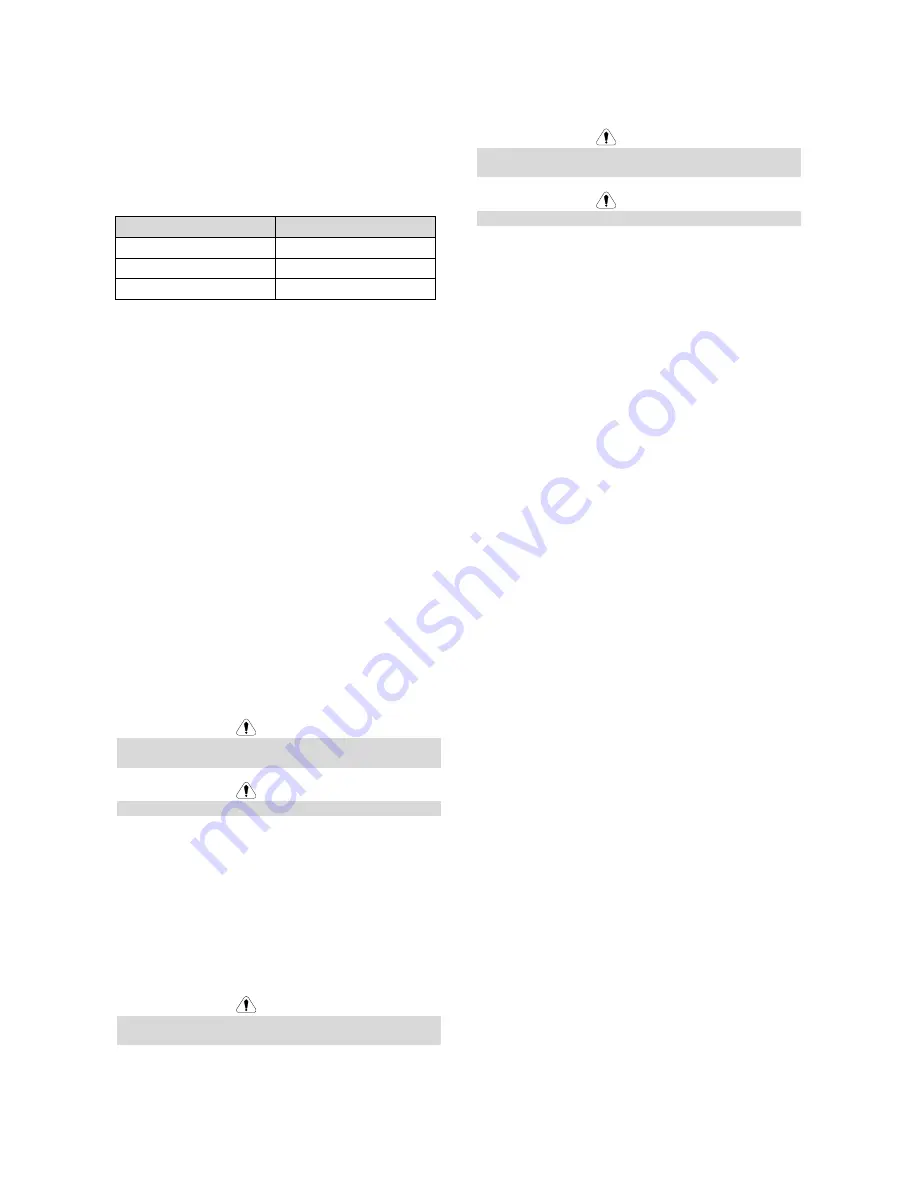
English
English
12
Welding GMAW, FCAW-GS and FCAW-SS Process in non-synergic mode
During non-synergic mode wire feed speed and welding
voltage are independent parameters and must be set by
the user.
Table 5. GMAW and FCAW non-synergic Welding
Programs
Process
Program
GMAW, standard CV
5
FCAW-GS, standard CV
7 or 155
FCAW-SS, Standard CV
6
Note:
The list of available programs depends on the
power source.
Procedure of begin welding of GMAW, FCAW-GS or
FCAW-SS process:
Connect Lincoln Electric power sources using
ArcLink
®
protocol to communication to wire feeder.
Place the machine conveniently near the work area
in a location to minimize exposure to weld spatter
and to avoid sharp bends in the gun cable.
Determine the wire polarity for the wire to be used.
Consult the wire data for this information.
Connect output the gun to GMAW, FCAW-GS or
FCAW-SS process to Euro Socket [1].
Connect the work lead to output sockets of the power
source and lock it.
Connect the work lead to the welding piece with the
work clamp.
Install the proper wire.
Install the proper drive roll.
Manually push the wire into the gun’s liner.
Make a sure, if it is needed (GMAW, FCAW-GS
process), that the gas shield has been connected.
Turn the input power ON and wait until the PF41 will
not be ready to work with the power source - Status
LED [18] stops blinking and lights steady green light.
Insert the wire into the welding gun.
WARNING
Keep the gun cable as straight as possible when loading
electrode through cable.
WARNING
Never use defected gun.
Check gas flow with Gas Purge Switch [12] – GMAW
and FCAW-GS process.
Close the wire drive door.
Close the spool wire case.
Select the right welding program. Non-synergic
programs are described in the Table 5.
Note:
The list of available programs depends on the
power source.
Set the welding parameters.
The welding machine is now ready to weld.
WARNING
The wire drive door and wire spool case have to be
completely closed during welding.
WARNING
Keep the gun cable as straight as possible when welding
or loading electrode through cable.
WARNING
Do not kink or pull cable around sharp corners.
By applying the principle of occupational health and
safety at welding, welding can be begun.
For 5, 6 and 7 program can set:
Wire Feed Speed, WFS [28]
The welding voltage [22]
Burnback Time [24]
Run-in WFS [25]
Preflow Time/ Postflow Time [Config Menu]
2-Step/4-Step [13]
Crater [26]
Pinch [23]
Pinch
controls the arc characteristics when short-arc
welding. increasing Pinch Control greater than 0.0
results in a crisper arc (more spatter) while decreasing
the Pinch Control to less than 0.0 provides a softer arc
(less spatter).
Adjust range: from -10 to +10.
Factory default, Pinch is OFF.
Summary of Contents for PF41
Page 23: ...English English 20 Connection Diagram ...
Page 24: ...English English 21 ...
Page 25: ...English English 22 ...