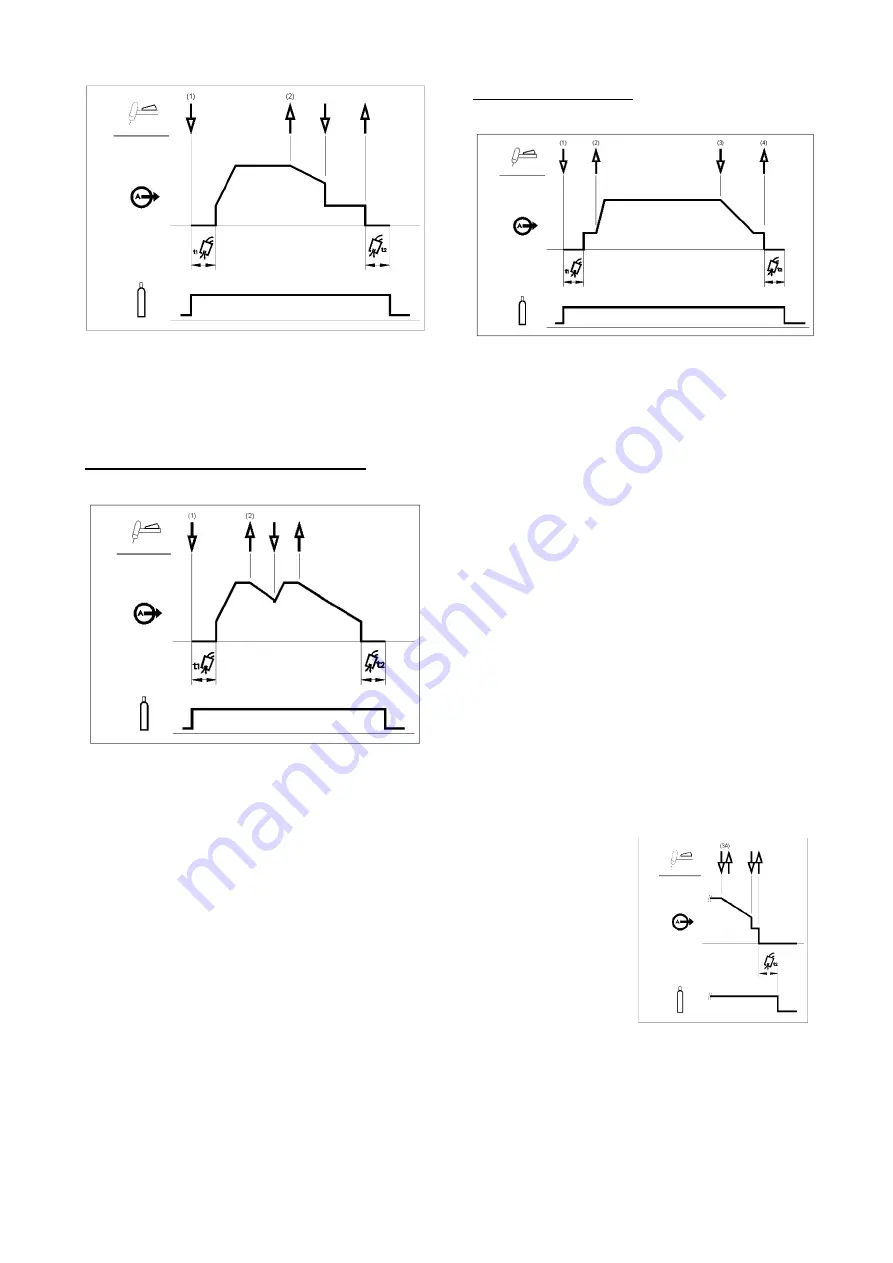
English 12 English
As shown above, it is possible to press and hold the TIG
torch trigger a second time during downslope to end the
downslope function and maintain the output current at
the Crater current. When the TIG torch trigger is
released the output will turn OFF and the post flow time
will start. This operation sequence, 2-step with restart
disabled, is the default setting from the factory.
2-Step Trigger Sequence with Restart Option
If the 2-step restart option is enabled from the setup
menu the following sequence will occur:
1. Press and hold the TIG torch trigger to start the
sequence as described above.
2. Release the TIG torch trigger to start the
downslope. During this time press and hold the TIG
torch trigger to restart welding. The output current
will increase again at a controlled rate until the
Welding current is reached. This sequence can be
repeated as many times as necessary. When the
welding is complete release the TIG torch trigger.
When the Crater current is reached the output of the
machine is turned OFF.
4-Step Trigger Sequence
With the 4-step trigger mode and a TIG welding mode
selected, the following welding sequence will occur.
1. Press and hold the TIG torch trigger to start the
sequence. The machine will open the gas valve to
start the flow of the shielding gas. After the pre-flow
time, to purge air from the torch hose, the output of
the machine is turned ON. At this time the arc is
started according to the selected welding mode.
After the arc is started the output current will be at
the Start current. This condition can be maintained
as long as necessary.
If the Start current is not necessary, do not hold the
TIG torch trigger as described at the beginning of this
step. In this condition, the machine will pass from
Step 1 to Step 2 when the arc is started.
2. Releasing the TIG torch trigger starts the upslope
function. The output current will be increased at a
controlled rate, or upslope time, until the Welding
current is reached. If the torch trigger is pushed
during the upslope time the arc will stop immediately
and the output of the machine is turned OFF.
3. Press and hold the TIG torch trigger when the main
part of the weld is complete. The machine will now
decrease the output current at a controlled rate, or
downslope time, until the Crater current is reached.
4. This Crater current can be maintained as long as
necessary. When the TIG torch trigger is released
the output of the machine is turned OFF and the
post flow time will start.
As shown here, after the
TIG torch trigger is quickly
pressed and released
from step 3A, it is possible
to press and hold the TIG
torch trigger another time
to end the downslope time
and maintain the output
current at the Crater
current. When the TIG
torch trigger is released
the output will turn OFF.
This sequence operation, 4-step with restart disabled, is
the default setting from the factory.