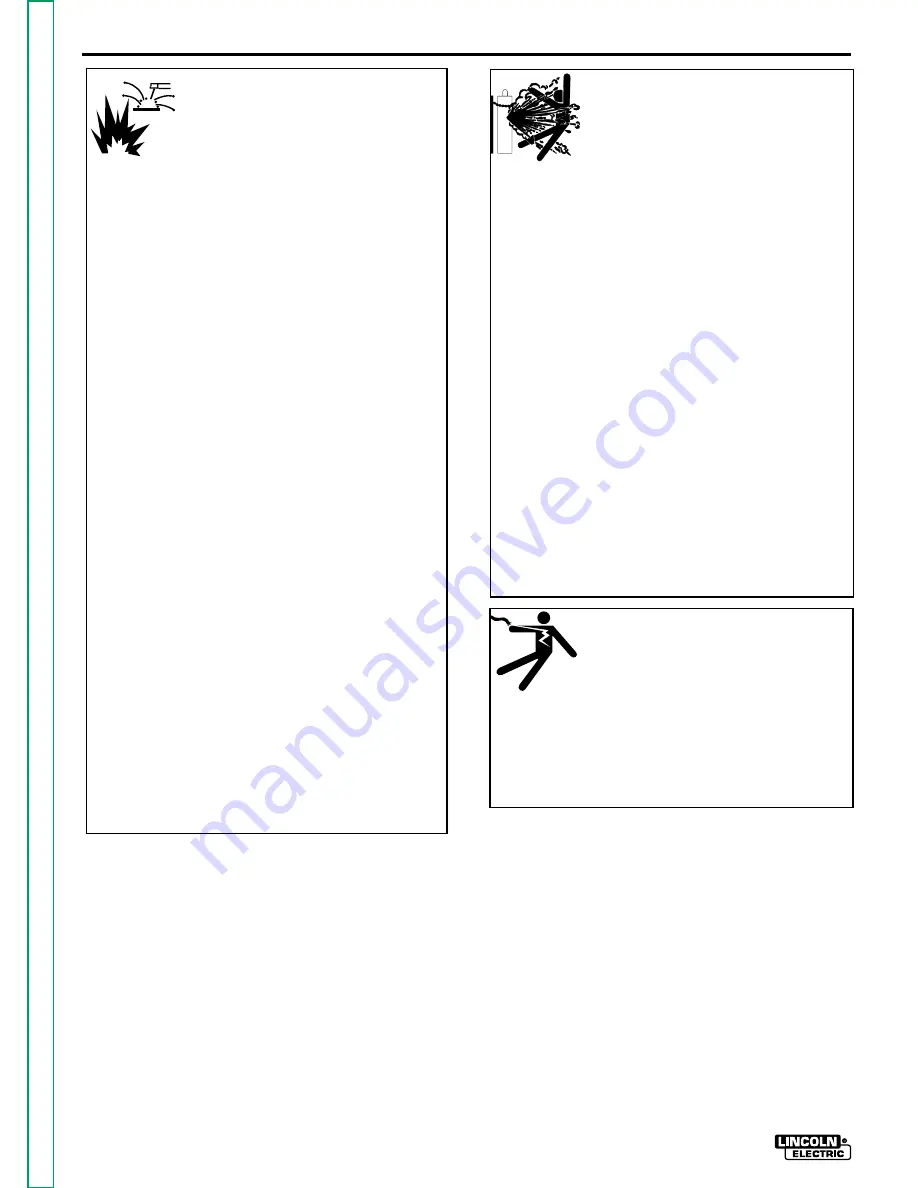
FOR ELECTRICALLY
powered equipment.
6.a.Turn off input power using the disconnect
switch at the fuse box before working on
the equipment.
6.b. Install equipment in accordance with the U.S. National
Electrical Code, all local codes and the manufacturer’s
recommendations.
6.c. Ground the equipment in accordance with the U.S. National
Electrical Code and the manufacturer’s recommendations.
CYLINDER may explode
if damaged.
5.a. Use only compressed gas cylinders contain-
ing the correct shielding gas for the process
used and properly operating regulators
designed for the gas and pressure used. All
hoses, fittings, etc. should be suitable for the
application and maintained in good condi-
tion.
5.b. Always keep cylinders in an upright position securely
chained to an undercarriage or fixed support.
5.c. Cylinders should be located:
• Away from areas where they may be struck or subjected to
physical damage.
• A safe distance from arc welding or cutting operations and
any other source of heat, sparks, or flame.
5.d. Never allow the electrode, electrode holder or any other
electrically “hot” parts to touch a cylinder.
5.e. Keep your head and face away from the cylinder valve outlet
when opening the cylinder valve.
5.f. Valve protection caps should always be in place and hand
tight except when the cylinder is in use or connected for
use.
5.g. Read and follow the instructions on compressed gas
cylinders, associated equipment, and CGA publication P-l,
“Precautions for Safe Handling of Compressed Gases in
Cylinders,” available from the Compressed Gas Association
1235 Jefferson Davis Highway, Arlington, VA 22202.
WELDING OR CUTTING
SPARKS can cause fire or
explosion.
4.a. Remove fire hazards from the welding or cut-
ting area. If this is not possible, cover them to
prevent the welding or cutting sparks from start-
ing a fire. Remember that welding or cutting sparks and hot
materials from welding or cutting can easily go through small
cracks and openings to adjacent areas. Avoid welding or cut-
ting near hydraulic lines. Have a fire extinguisher readily
available.
4.b. Where compressed gases are to be used at the job site,
special precautions should be used to prevent hazardous
situations. Refer to “Safety in Welding and Cutting” (ANSI
Standard Z49.1) and the operating information for the
equipment being used.
4.c. When not welding or cutting, make certain no part of the
electrode circuit is touching the work or ground. Accidental
contact can cause overheating and create a fire hazard.
4.d. Do not heat, cut or weld tanks, drums or containers until the
proper steps have been taken to insure that such procedures
will not cause flammable or toxic vapors from substances
inside. They can cause an explosion even though they have
been “cleaned”. For information, purchase “Recommended
Safe Practices for the Preparation for Welding and Cutting of
Containers and Piping That Have Held Hazardous
Substances”, AWS F4.1 from the American Welding Society
(see address above).
4.e. Vent hollow castings or containers before heating, cutting or
welding. They may explode.
4.f. Sparks and spatter are thrown from the welding and cutting
arc. Wear oil free protective garments such as leather gloves,
heavy shirt, cuffless trousers, high shoes and a cap over
your hair. Wear ear plugs when welding or cutting out of posi-
tion or in confined places. Always wear safety glasses with
side shields when in a welding or cutting area.
4.g. Connect the work cable to the work as close to the welding
or cutting area as practical. Work cables connected to the
building framework or other locations away from the welding
area increase the possibility of the welding or cutting current
passing through lifting chains, crane cables or other alternate
circuits. This can create fire hazards or overheat lifting
chains or cables until they fail.
4.h. Also see item 7c.
IDEALARC DC-600
SAFETY
ii