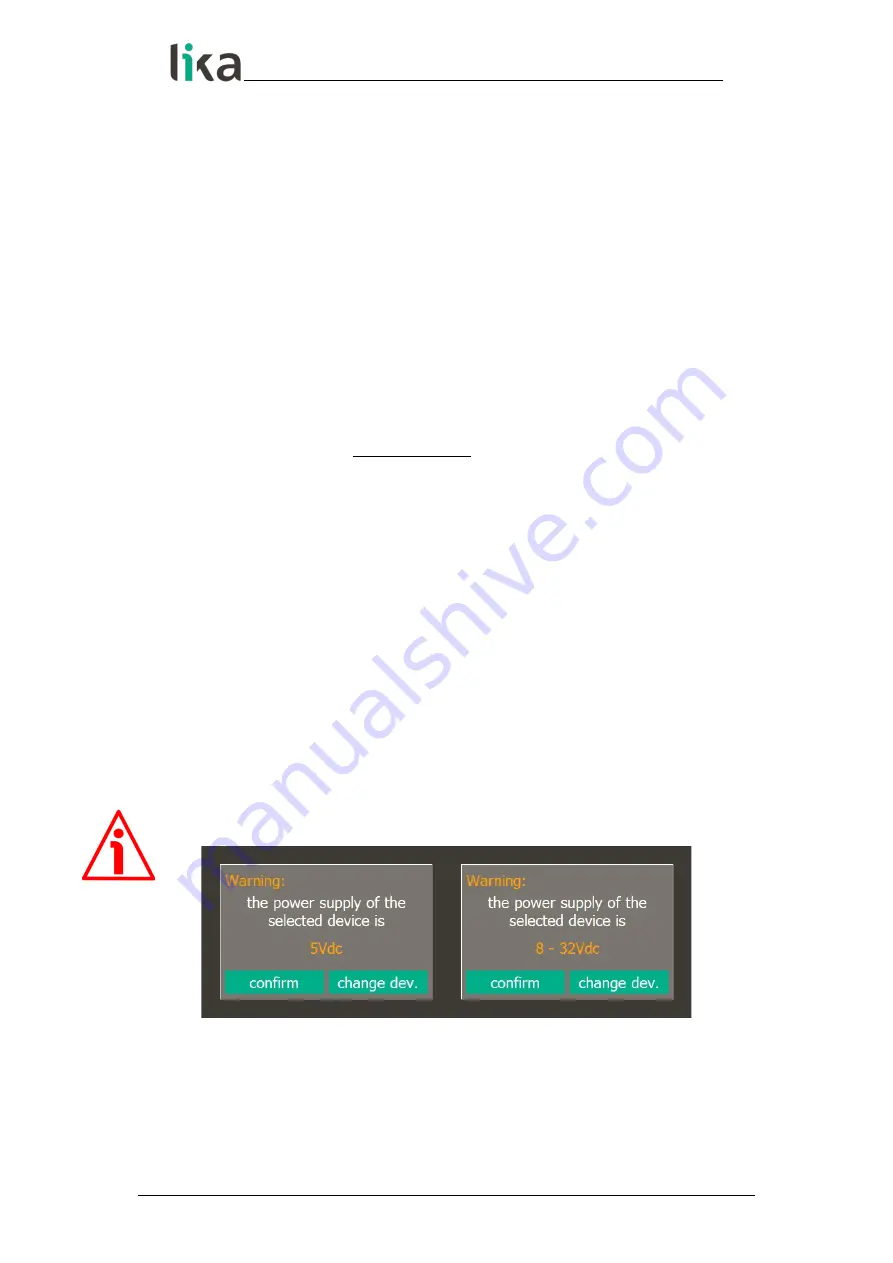
AMM8A SSI & BiSS C-mode
6.5 Encoder calibration and synchronization interface
To launch the program just double-click the IF90-SC_AMM8_xx_vx.x.x.exe
executable file. The main page of the encoder calibration and synchronization
interface will appear.
It consists of a single page where all features and diagnostic information are
available.
Two main sections can be found in the page:
1. the section at the top of the page where the functions necessary for
connection can be found;
2. the
Start procedure
section in the middle of the page where the
functions necessary for the mechanical alignment, calibration and
synchronization procedure can be found.
If you select the
Diagnostics
check box on the right side of the page, the
window of the interface will enlarge: diagnostic information (data exchange)
concerning the interface (not the encoder!) will be available in the column on
the right. You can save the sequence of messages in the IF90_diagnostics.txt file
(press the
SAVE FILE
button) or delete them (press the
CLEAR
button).
6.5.1 Establishing a connection to the IF90-SC interface
After opening the program, you must establish the connection between the
IF90-SC interface and the encoder. You must select the interface unit model
through the
Interface
drop-down menu first, then the encoder model through
the
Encoder
drop-down menu, confirm the encoder choice and finally press the
CONNECT
buttons on the side of each item to establish the connection. Please
note that you cannot try connecting to the encoder until the connection to the
interface is missing, the relevant
CONNECT
button is disabled.
WARNING
Please note that, after choosing the encoder model, you will be required to
confirm your choice by pressing the
CONFIRM
button in the pop-up window.
The IF90-SC interface in fact also provides power conversion to power the
encoder. When you choose the encoder model you automatically select also the
voltage to be supplied to the encoder: if you select a wrong model and perhaps
MAN AMM8A SSI_BiSS E 1.10.odt 6 - Calibration and synchronization procedure 41 of 80