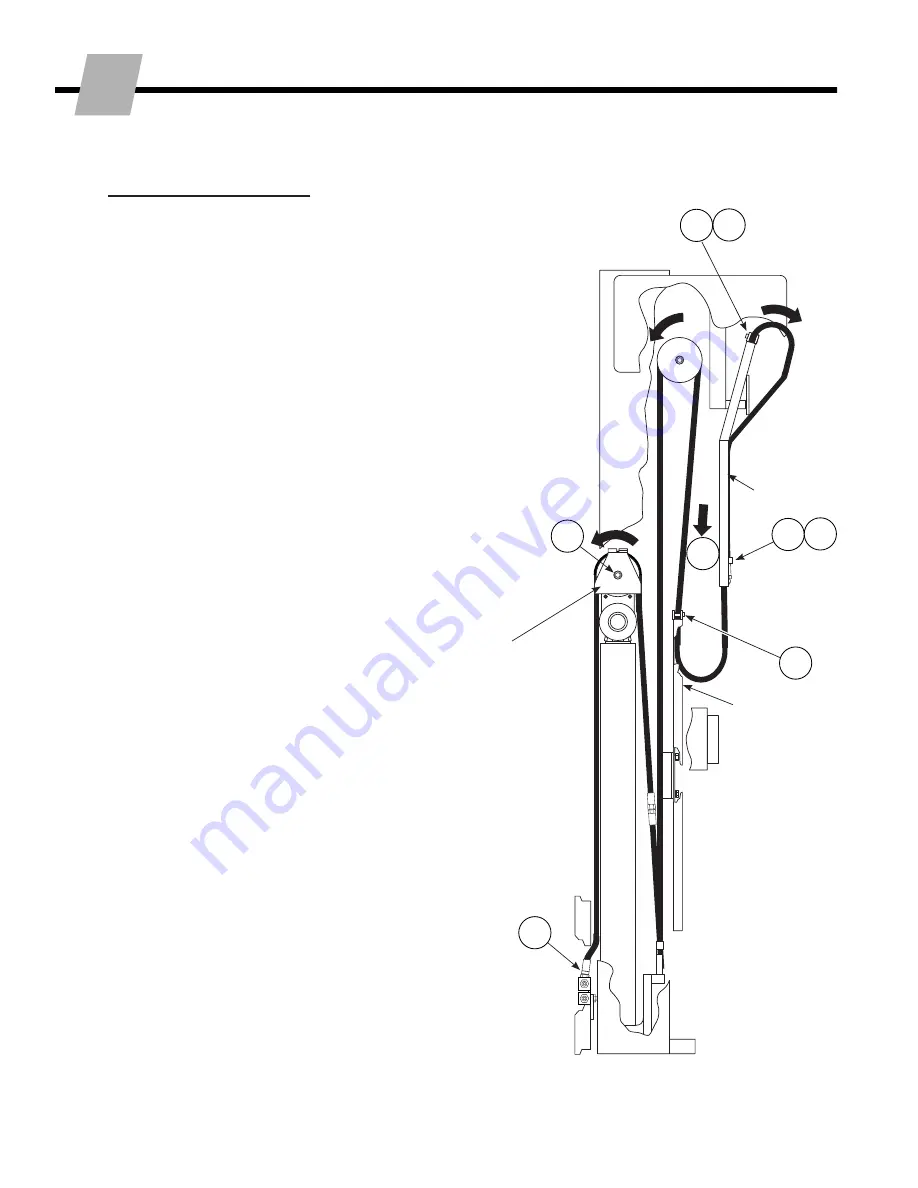
Page 12
263920 R
2
I
nstallation
2.4-2
Internal Reeving
STANDARD
( Continued )
Lower
Hose
Guide
Crosshead
MA3158.eps
25
19
24
22
Upper
Hose
Guide
19
23
24
21
19.
Install the hose clamps to the upper hose guide.
Leave capscrews finger tight.
20.
Route the hoses under the hose clamps at the top
of the upper hose guide. Tighten the capscrews
finger tight.
21.
Route the hoses under the hose clamps at the
bottom of the upper hose guide. Do no tighten the
clamp capscrews.
22.
Tighten the crosshead coverplate capscrew to a
torque of 52 ft.-lbs. (71 Nm).
23.
Align the hoses by twisting the hose ends to
travel centered in the crosshead on the natural
curve of the hose. The hoses should travel
parallel to each other. Hold the hoses while
tightening the fittings to keep the hoses from
twisting.
24.
Loosen the hose clamps at the top of the lower
hose guide. Pull down on the hoses with 40 lbs.
of force. Tighten the hose clamp capscrews to 7-
11 ft.-lbs. (10-15 Nm).
25.
Loosen the hose clamps on the upper hose guide.
Adjust the hoses to the natural hose bend and
align evenly spaced in the guide rails. Tighten the
hose clamp capscrews to 7-11 ft.-lbs. (10-15
Nm).
26.
Raise and lower the Mast slowly through several
cycles and check for proper hose alignment,
clearances and hose tracking in the guides.