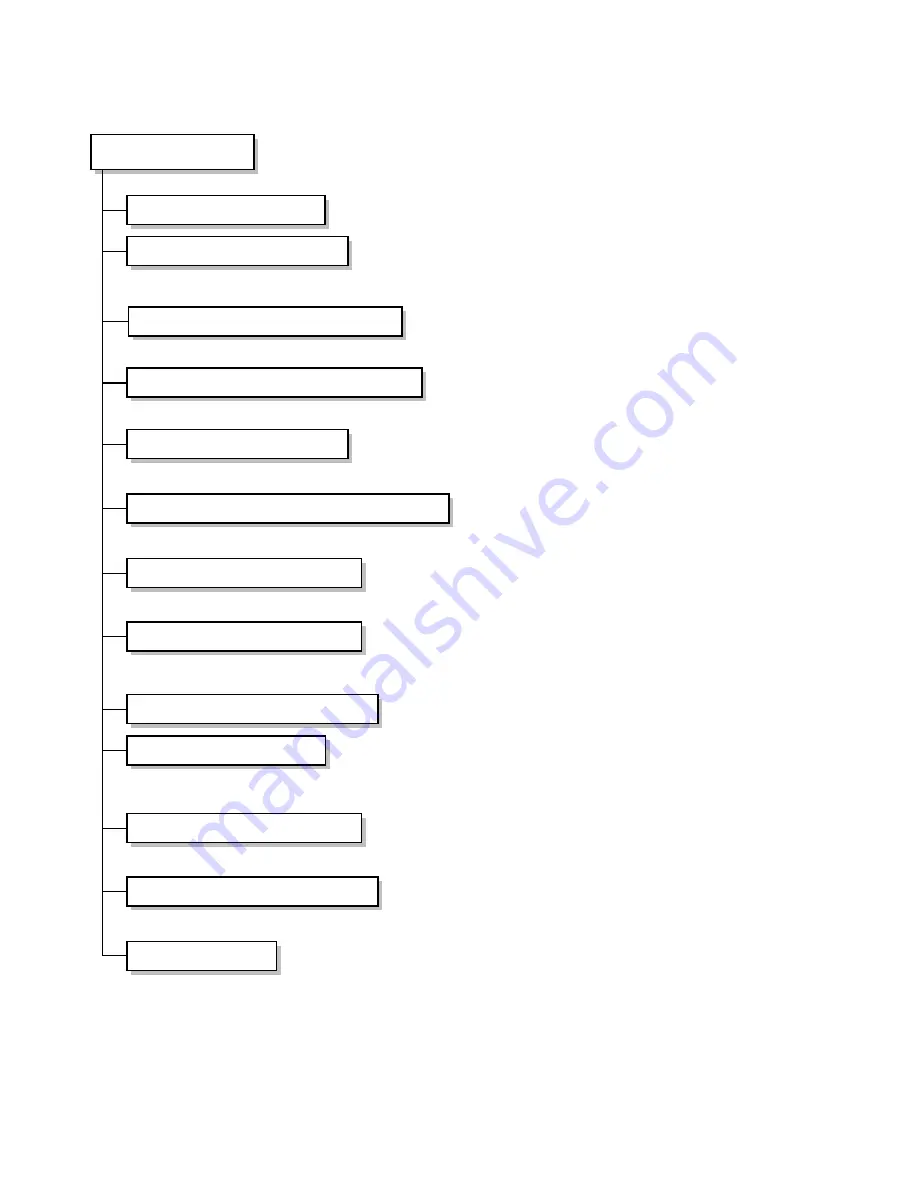
–5–
1.4 Functions
Indoor Unit
Power Switch ON/OFF
Operation Mode Control
Sensing the room temperature
Controlling the room temperature
Starting Current Control
Sensing Heat Exchanger Temperature
Timer Delay Safety Control
Indoor Fan Speed Control
Operation Indication lamps
Temperature Setting
Airflow Direction Control
Room temperature Display
Timer Control
• Cooling, Fan
➔
Cooling Model
• Room temperature sensor (Thermistor)
• Maintains the room temperature in accordance with the setting temperature.
• Indoor fan is delayed for 3 sec at the starting.
• Heat exchanger temperature sensor (Thermistor)
• Restarting is inhibited for approx. 3 minutes.
• High, Low
• Up : up to 30°C
• Down : down to 16°C
• Airflow direction Manual control
• Low, 10° ~ 35°C, Hi
• Off Timer (1, 2, 3....7 hour)
Summary of Contents for LP-8091PC
Page 1: ...Package Air Conditioner SERVICE MANUAL MODEL LP 8091PC Библиотека СОК ...
Page 42: ...9 Electronic Control Device 42 9 1 MAIN P C B ASSY ...
Page 44: ...10 Schematic Diagram 44 Circuit and Troubleshooting ...
Page 46: ... 46 14 17 10 19 29 1 13 11 8 1 15 12 8 9 20 22 5 6 7 2 4 3 2 1 16 ...
Page 49: ... 49 Outdoor Unit 4 1 4 2 4 4 4 3 12 8 ...
Page 52: ...P No 3828A30074W April 2000 Printed in Korea ...