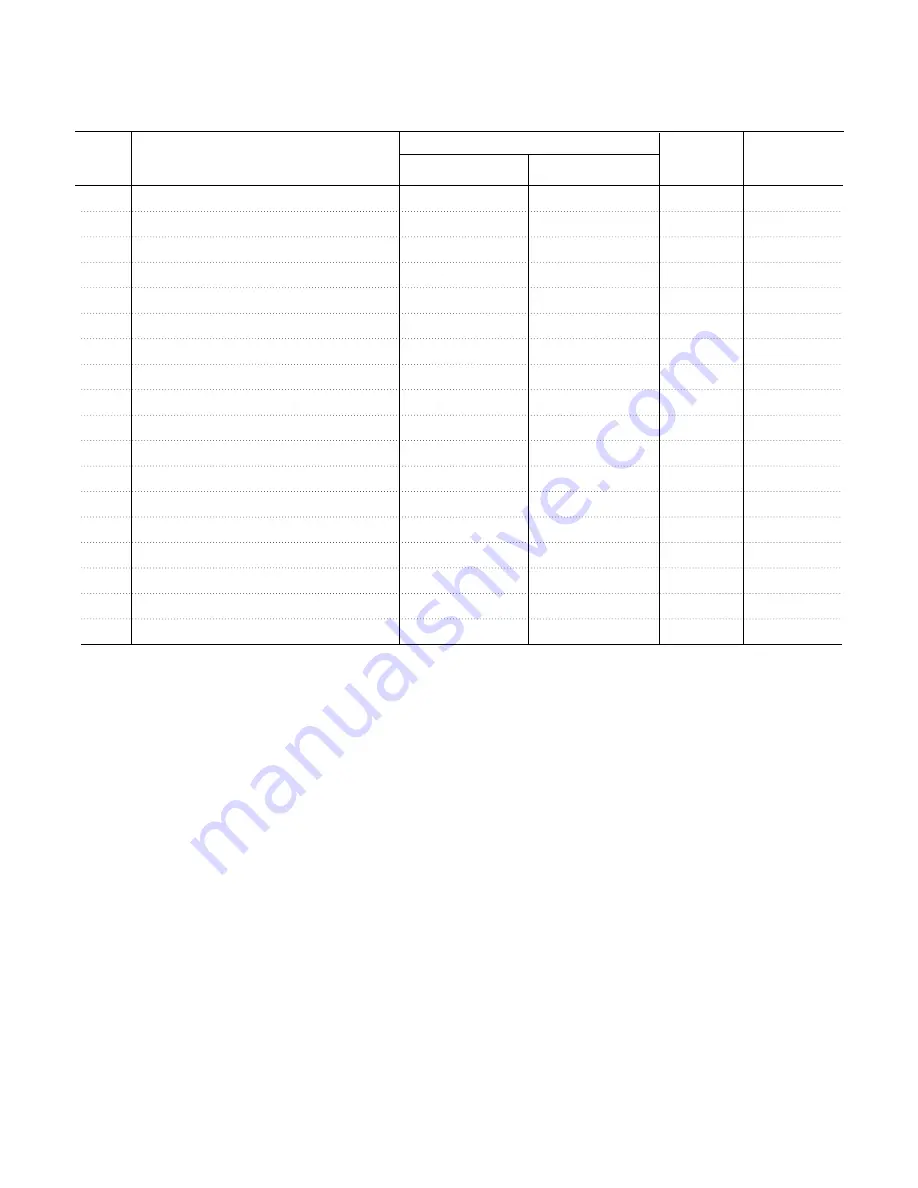
– 78 –
No.
DESCRIPTION
LP-20091CL
LP-20091XL
PART NO.
Q'TY
REMARK
27
BUSHING BASE COMP
4A00077A
4A00077A
16
28
NUT
4H00947C
4H00947C
16
29
FAN ASSY
0A00026B
0A00026B
4
30
FAN LOCKER
4A01387A
4A01387A
4
31
SPRING LOCK WASHER
1WSD1000030
1WSD1000030
4
32
HEXAGON NUTS
1NHA1001206
1NHA1001206
4
33
GRILLE COVER
2A00144P
2A00144P
4
34-1
PANEL ASSY FRONT
3721AP2913P
3721AP2913P
2
34-2
PANEL ASSY FRONT
3721AP2913Q
3721AP2913Q
2
35
COVER ASSY CONTROL
3551AP7047Z
3551AP7047Z
2
36
PANEL INSTALL-U
3720AP3810P
3720AP3810P
2
37
BRACKET INSTALL-L
4810AP3814P
4810AP3814P
2
39
BRACKET F.P
4810AP7078A
4810AP7078A
2
40
COVER FAN
3550AP3912A
3550AP3912A
2
42
LOW PRESSURE S/W
3A02414B
3A02414B
2
43
HIGH PRESSURE S/W
6600AG3057A
6600AG3057A
2
44
TUBE ASSY, DISCHARGE
5211A30051B
5211A30051B
2
45
TUBE ASSY, CONDENSER
5211A30052A
5211A30052A
2
Summary of Contents for LP-10091CL/XL
Page 1: ...Package Air Conditioner SERVICE MANUAL MODEL LP 10091CL XL LP 15091CL XL LP 20091CL XL ...
Page 7: ...2 1 LP 10091CL XL 2 2 LP 15091CL XL 2 3 LP 20091CL XL 7 2 DIMENSIONS ...
Page 53: ... 53 9 ELECTRONIC CONTROL DEVICE 9 1 MAIN P C B ASSY ...
Page 55: ... 55 10 SCHEMATIC DIAGRAM LP 10091CL XL LP 15091CL XL ...
Page 57: ... 57 22 19 10 4 5 1 12 21 20 15 13 16 2 9 8 7 18 17 6 3 11 14 ...
Page 62: ... 62 3 13 12 9 11 10 2 8 1 6 5 7 4 16 17 24 25 22 20 14 15 23 21 26 19 ...
Page 67: ... 67 3 13 12 9 11 10 2 8 1 6 5 7 4 16 17 24 25 22 20 14 15 23 21 26 19 ...
Page 76: ...11 6 Outdoor Unit LP 20091CL 20091XL 1 Exploded View 76 ...