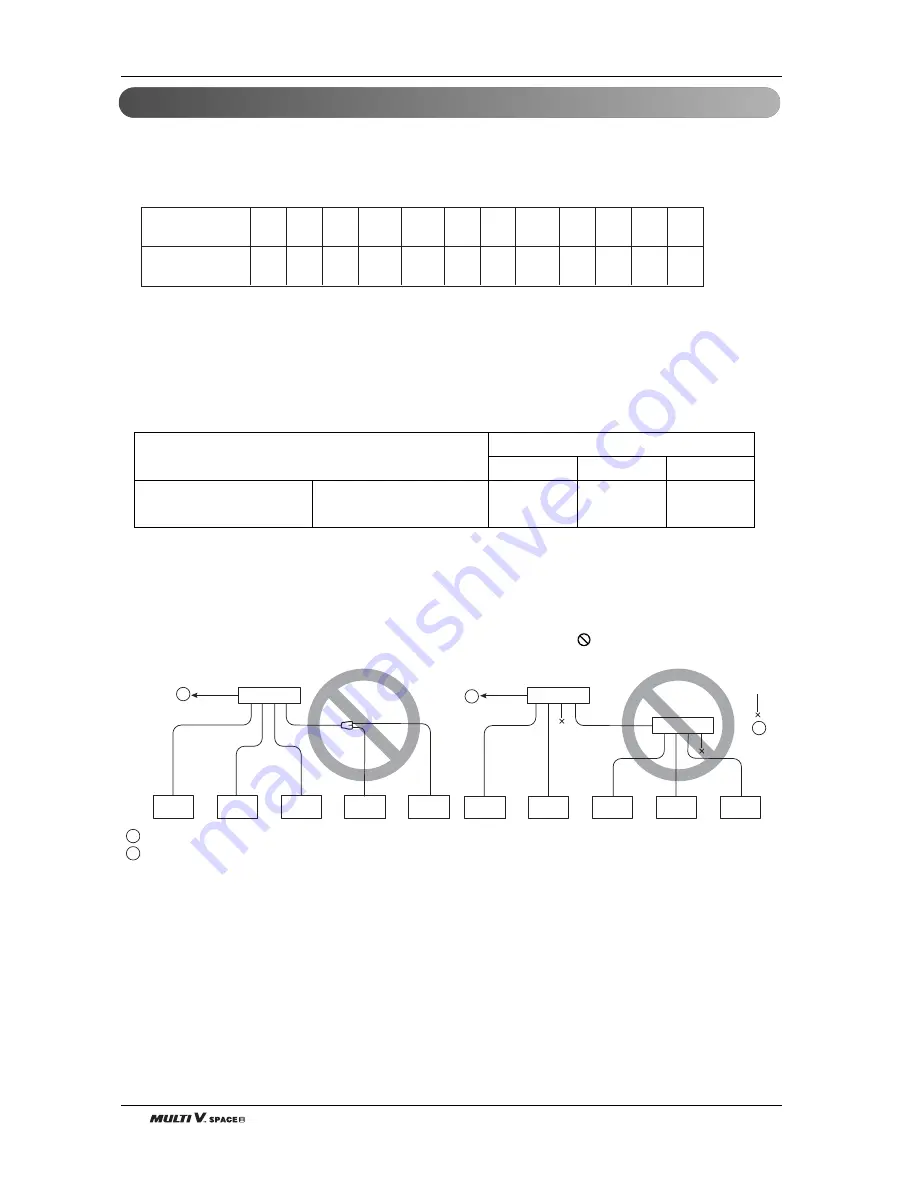
18
Outdoor Unit
Refrigerant piping installation
To Outdoor Unit
Sealed Piping
A
A
B
A
B
1. Use the following materials for refrigerant piping.
• Material: Seamless phosphorous deoxidized copper pipe
• Wall thickness : Comply with the relevant local and national regulations for the designed pressure
3.8MPa. We recommend the following table as the minimum wall thickness.
2. Commercially available piping often contains dust and other materials. Always blow it clean with a dry inert
gas.
3. Use care to prevent dust, water or other contaminants from entering the piping during installation.
4. Reduce the number of bending portions as much as possible, and make bending radius as big as possible.
5. Always use the branch piping set shown below, which are sold separately.
6. If the diameters of the branch piping of the designated refrigerant piping differs, use a pipe cutter to cut
the connecting section and then use an adapter for connecting different diameters to connect the piping.
7. Always observe the restrictions on the refrigerant piping (such as rated length, difference in height, and
piping diameter).
Failure to do so can result in equipment failure or a decline in heating/cooling performance.
8. A second branch cannot be made after a header. (These are shown by .)
9. The Multi V will stop due to an abnormality like excessive or insufficient refrigerant. At such a time, always
properly charge the unit. When servicing, always check the notes concerning both the piping length and
the amount of additional refrigerant.
10
. Never perform a pump down. This will not only damage the compressor but also deteriorate the
performance.
11
. Never use refrigerant to perform an air purge. Always evacuate using a vacuum pump.
Caution
ARBLN01621
ARBLN03321
ARBL054
ARBL057
ARBL1010
Y branch
Header
4 branch
7 branch
10 branch
0.99
22.2
1.1
31.8
1.21
34.9
1.35
38.1
1.43
41.3
0.99
28.58
0.99
25.4
0.99
19.05
0.99
15.88
0.8
12.7
0.8
9.52
0.8
6.35
Minimum
thickness [mm]
Outer diameter
[mm]