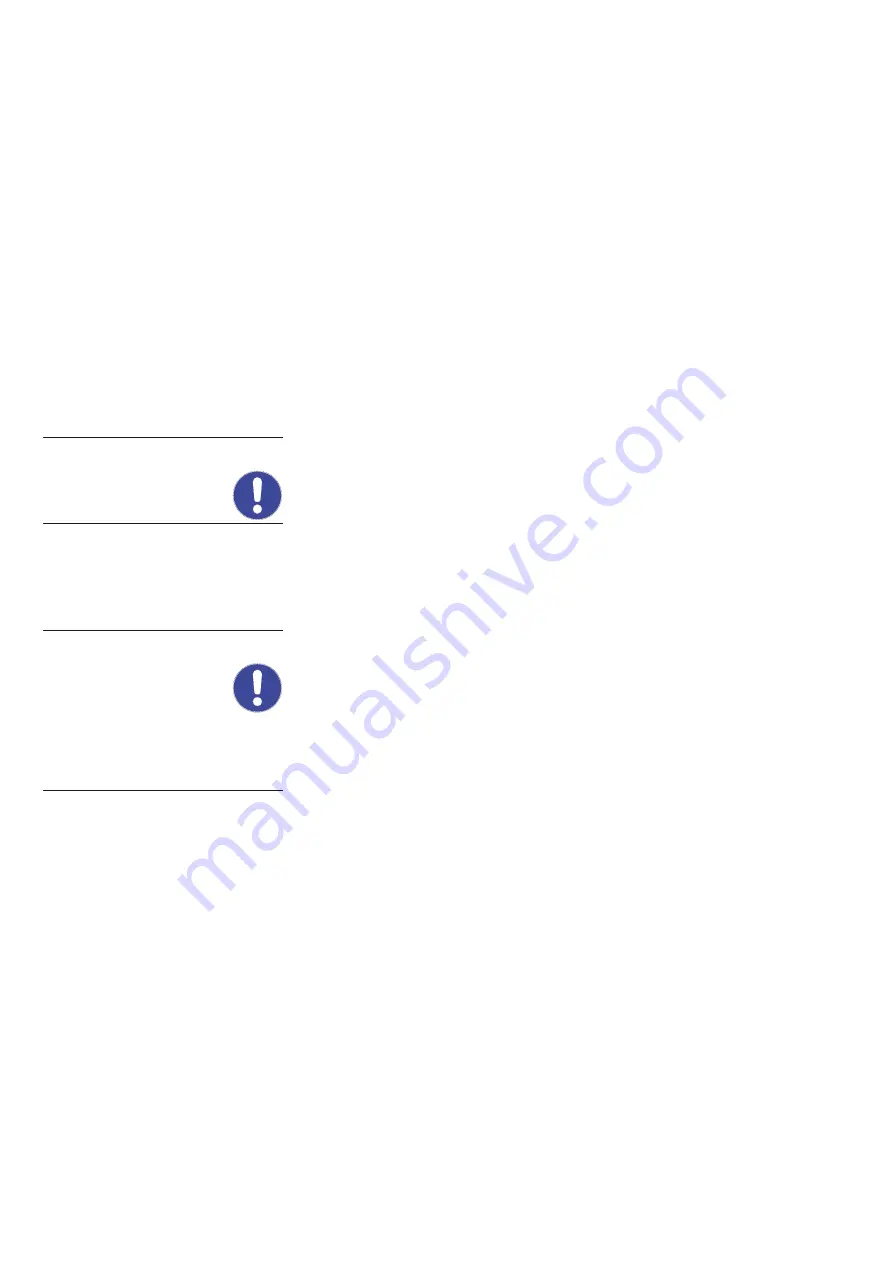
24
GA02307_002_C0 - 11/2016 - © Leybold
Operation
Standard gasballast with E.M. valve (Cat. No. 951 31).
This kit is intended for being mounted on pumps on which the gas ballast
can be driven by an electromagnetic valve applied at 24 VDC 18 W.
With the gas ballast valve open and at operating temperature, the
SOGEVAC
®
pump can pump pure water vapor up to the water vapor
tolerance indicated in the Technical Data. The pump’s water vapor tolerance
can be increased by raising the operating temperature.
Use a screwdriver to open the gas ballast valve. The running noise of the
pump is slightly louder when the gas ballast valve is open. Before opening
the pump to vapors, ensure that the gas ballast valve is open and that the
pump has been warmed up for about 30 minutes with closed intake line.
Do not open the pump to condensable vapors until it has warmed to oper-
ating temperature (approximately 75 °C); pumping process gas with a cold
pump results in vapors condensing in the oil.
For processes with a high proportion of condensable vapors, slowly open the
intake line after reaching the operating temperature to prevent excessive
quantities of vapor entering the pump.
One sign of condensation of vapors in the pump is a rise in the oil level
during operation of the pump.
During pumping, vapors may dissolve in the oil. This changes the oil prop-
erties and causes a risk of corrosion in the pump. Therefore, do not switch
off the pump immediately after completion of the process. Instead, allow
the pump to continue operating with the gas ballast valve open and the
intake line closed until the oil is free of condensed vapors. We strongly rec-
ommend operating the pump in this mode for about 30 minutes after com-
pletion of the process.
In cyclic process operation, the pump should not be switched off during the
intervals between the individual working phases, but should continue to run
with gas ballast valve open and intake port closed (if possible via a valve).
Power consumption is minimal when the pump is operating at ultimate
pressure.
Once all vapors have been pumped off from a process (e.g. during drying),
the gas ballast valve can be closed to improve the ultimate pressure.
4.2 Switching off / Shutdown
Under normal circumstances, all that you need to do is to switch off the
pump.
The intake port of the SOGEVAC
®
pumps contains an anti-suckback valve
which closes the intake port when the pump is switched off, thus maintaining
the vaccum in the connected apparatus and preventing oil from being sucked
back into the apparatus. The valve’s functioning is not impaired by gas ballast
operation.
Nevertheless, the anti suck-back valve is not a safety valve and operates
correctly only if clean and undamaged. A valve must be installed if oil back
streaming is to be avoided be all means.
NOTICE
NOTICE
Summary of Contents for SOGEVAC SV 200 BR2
Page 36: ... 36 GA02307_002_C0 11 2016 Leybold Spare parts fig 6 SV200 ...
Page 38: ... 38 GA02307_002_C0 11 2016 Leybold Spare parts fig 7 SV200 ...
Page 40: ... 40 GA02307_002_C0 11 2016 Leybold Spare parts fig 7 SV200 ...
Page 43: ... 43 GA02307_002_C0 11 2016 Leybold EC Conformance Declaration ...