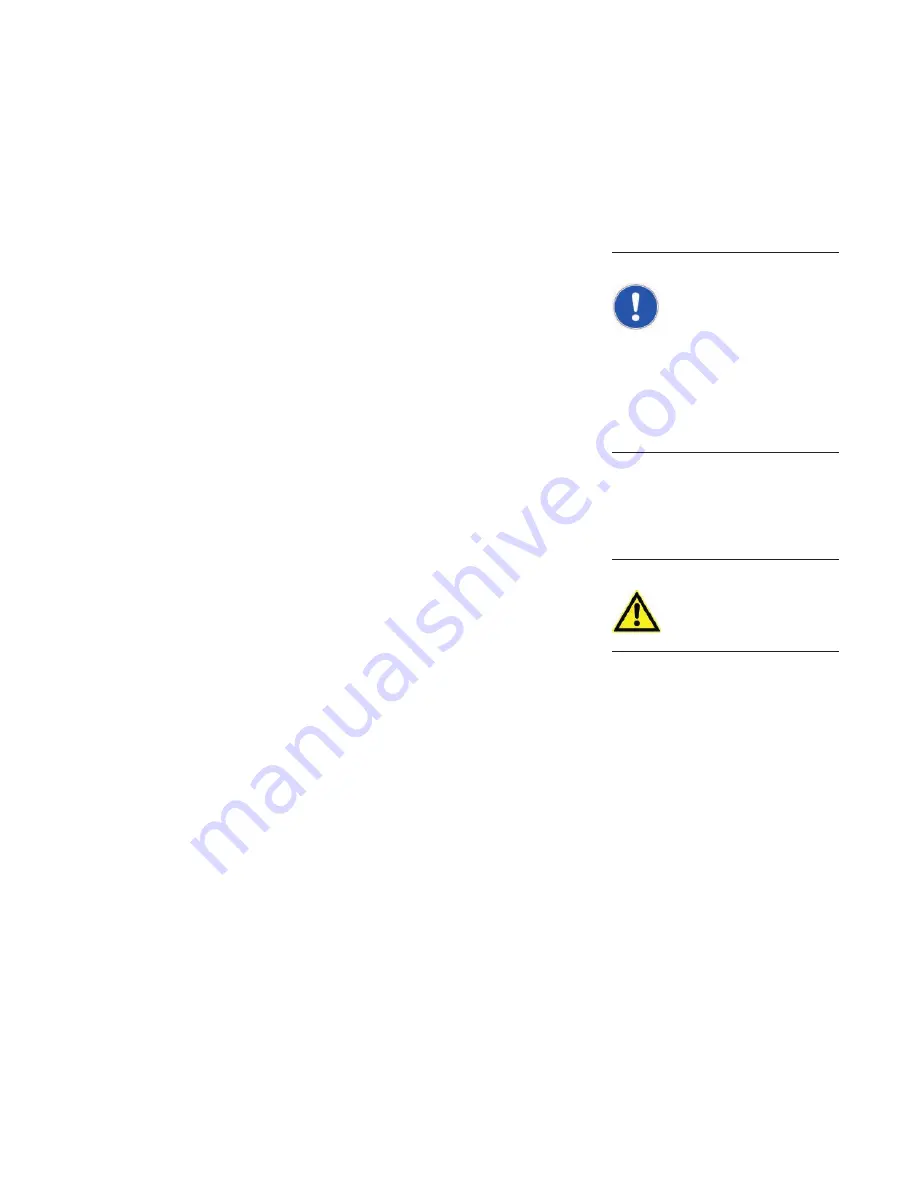
Installation
29
300407956_002_C1 - 01/2017 - © Leybold
The exhaust line should have the same or larger diameter than the exhaust
flange (DN 40 KF) and 2.0 mm min. thickness. The exhaust line must be able
to withstand 1.3 bar and 150 °C.
Observe the following when connecting the pump and the exhaust system:
When there is high pressure from the exhaust system, check whether the
silencer of the vacuum pump and the exhaust pipes for the facilities are
blocked or not.
When using explosive, corrosive or toxic gas for the process, the pump
exhaust system must not contact the atmosphere.
The supports must be installed under the exhaust pipe line to avoid any
leakage caused by shear strength at the connecting parts of the pipe lines.
A leak check will surely be performed after the installation of the vacuum
pump or when finding any leakage. When proceeding with the leak check for
the vacuum pump or the vacuum system, please pay attention to check any
emission of gas (moisture, residual of organic solvent) which will cause virtual
leaks of the vacuum system. The recommended maximum leak rate value for
a purge gas leakage test or other ways of test is 1x10
-5
mbarl/s.
Observe Safety Information 0.1.6 to 0.1.8.
Check leak tightness of the exhaust lines on a regular basis!
Observe Safety Information 0.4.
Keep the exhaust line free of deposits. If the exhaust flow becomes restrict-
ed, deposits could collect in the LEYVACs.
Connect the exhaust line to an abatement system with sufficient throughput,
if required by the process. The LEYVAC pumps will not be switched off auto-
matically, when the abatement system is too small and there is an overpres-
sure. As prevention an optional pressure sensor may be installed; in this case
provide an adequate electrical connection; cf. Section 3.7.3.
In order to prevent deposits in the exhaust lines it may be necessary to heat
the exhaust lines.
Run the exhaust line only by way of a fixed installation to the outside and/or
connected to a silencer.
NOTICE
WARNING