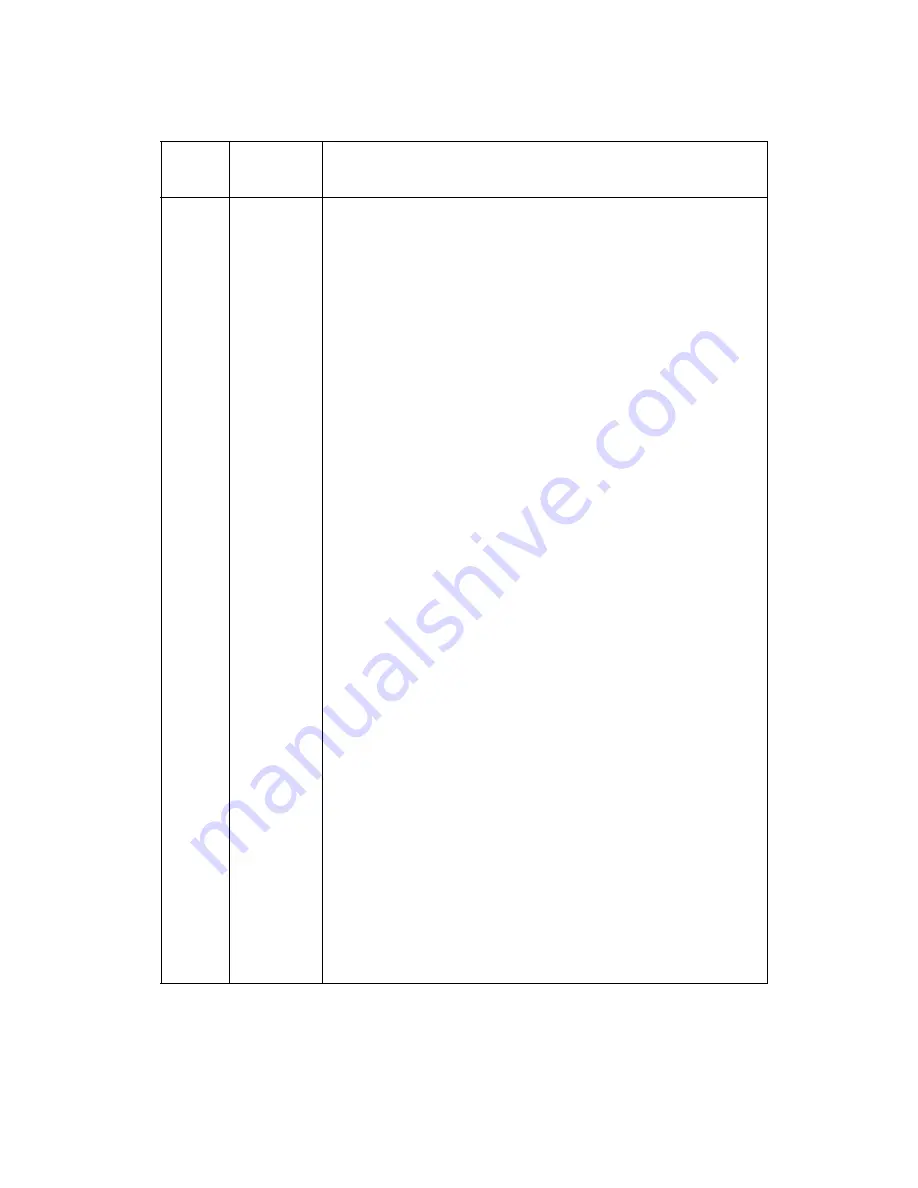
Parts catalog
7-11
25XX-100, -110
Assembly 3: Carrier/paper feed (left side)
Asm-
Index
Part
number
Description
3-1
40X2910
Gears and bushings, parts packet (258X)
2
40X2926
Screws, washers and clips, parts packet
3
40X2931
Kit, pull tractor actuator
4
40X2966
Frame, left side (2580, 2581)
4
40X2967
Frame, left side (2590, 2591)
5
40X2938
Sensor, Pull Tractor
6
40X3007
Plate, frame support (2580, 2590)
6
40X3008
Plate, frame support (2581, 2591)
7
40X2921
Holder, lower pinch roller shaft, left
8
40X2906
Springs, parts packet
9
40X2939
Sensor, Paper Select
10
40X2908
Holder, platen
11
40X2893
Sensor, Head Gap
12
40X2969
Guide, paper assembly (2580, 2590)
12
40X2970
Guide, paper assembly (2581, 2591)
13
40X2973
Platen (2580, 2590)
13
40X2974
Platen (2581, 2591)
14
40X2895
Guide, ASF/DTR, left
15
40X2919
Sensor, Top-of-form
16
40X2972
Sensor, Paper Present
17
40X2986
Gear, ribbon drive rack (2580, 2590)
17
40X2987
Gear, ribbon drive rack (2581, 2591)
18
40X2977
Plate, tension pulley assembly
19
40X3021
Plate, carrier assembly (2580, 2590)
19
40X3022
Plate, carrier assembly (2581, 2591)
20
40X2975
Separator, paper (2580, 2590)
20
40X2976
Separator, paper (2581, 2591)
21
40X2901
Motor, carrier (with BKT)
22
40X2920
Sensor, Home Position
Summary of Contents for 25**-100
Page 11: ...xi 25XX 100 110 ...
Page 62: ...2 42 Service Manual 25XX 100 110 ...
Page 74: ...3 12 Service Manual 25XX 100 110 ...
Page 118: ...4 44 Service Manual 25XX 100 110 Sensor removals ...
Page 124: ...4 50 Service Manual 25XX 100 110 ...
Page 127: ...Locations and connectors 5 3 25XX 100 110 Logic board 9w 24w ...
Page 130: ...5 6 Service Manual 25XX 100 110 Logic board 9w 24w ...
Page 132: ...5 8 Service Manual 25XX 100 110 Logic board 9w 24w ...
Page 134: ...5 10 Service Manual 25XX 100 110 Logic board 9w 24w ...
Page 136: ...5 12 Service Manual 25XX 100 110 Logic board 9w 24w ...
Page 138: ...5 14 Service Manual 25XX 100 110 Logic board 9w 24w ...
Page 140: ...5 16 Service Manual 25XX 100 110 Logic board 9w 24w ...
Page 142: ...5 18 Service Manual 25XX 100 110 Logic board 9w 24w ...
Page 144: ...5 20 Service Manual 25XX 100 110 Logic board 9w 24w ...
Page 146: ...5 22 Service Manual 25XX 100 110 Logic board 9w 24w ...
Page 148: ...5 24 Service Manual 25XX 100 110 Logic board 9w 24w ...
Page 152: ...5 28 Service Manual 25XX 100 110 ...
Page 160: ...7 2 Service Manual 25XX 100 110 Assembly 1 Covers ...
Page 162: ...7 4 Service Manual 25XX 100 110 Assembly 1 cont Covers ...
Page 164: ...7 6 Service Manual 25XX 100 110 Assembly 2 Carrier paper feed right side ...
Page 166: ...7 8 Service Manual 25XX 100 110 Assembly 2 cont Carrier paper feed right side ...
Page 168: ...7 10 Service Manual 25XX 100 110 Assembly 3 Carrier paper feed left side ...
Page 170: ...7 12 Service Manual 25XX 100 110 Assembly 3 cont Carrier paper feed left side ...
Page 172: ...7 14 Service Manual 25XX 100 110 Assembly 4 Electronics ...
Page 174: ...7 16 Service Manual 25XX 100 110 Assembly 5 ASF Roller support ...
Page 176: ...7 18 Service Manual 25XX 100 110 Assembly 6 ASF Side frame covers ...
Page 178: ...7 20 Service Manual 25XX 100 110 Assembly 7 Tractor 2 option ...
Page 180: ...7 22 Service Manual 25XX 100 110 ...
Page 184: ...I 4 Service Manual 25XX 100 110 ...