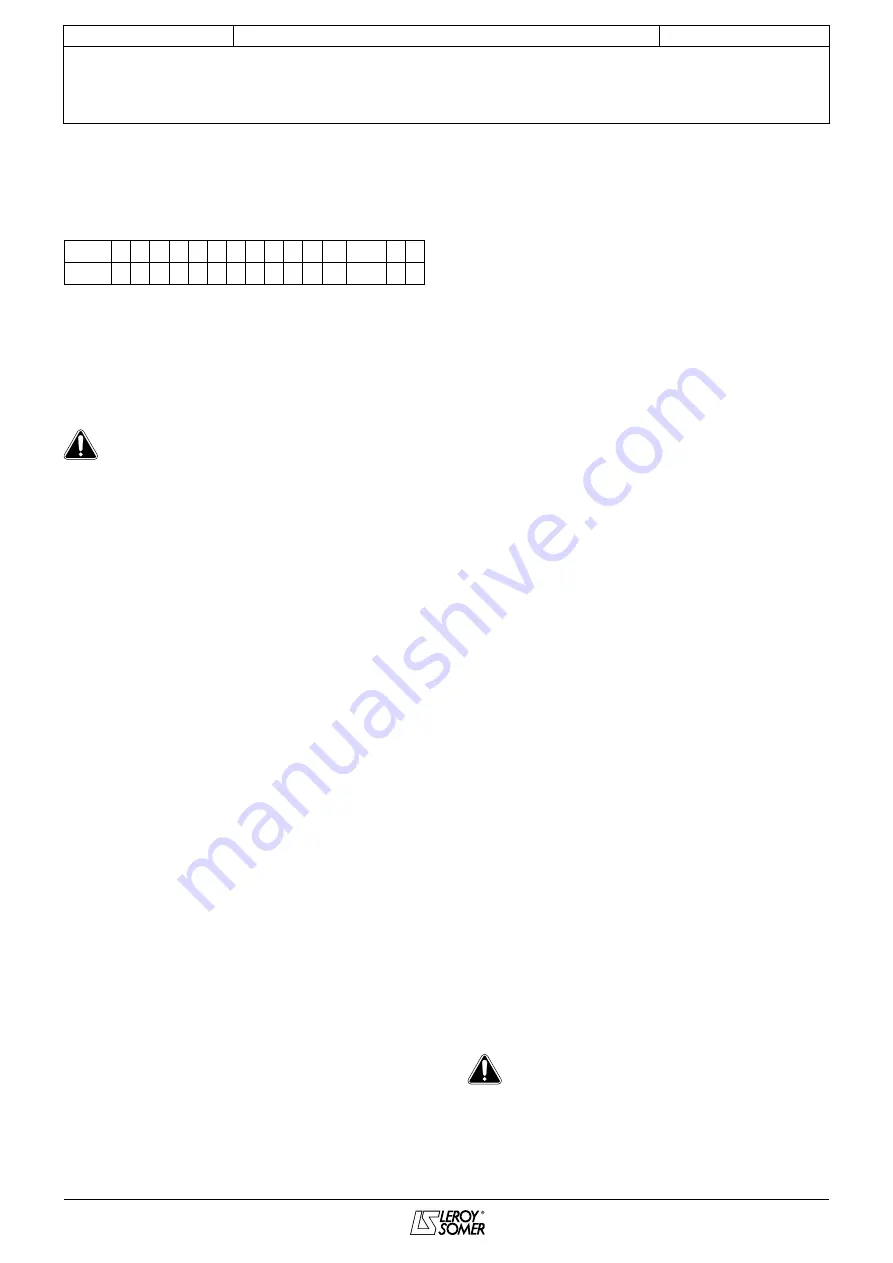
7
2009.07 / a
LEROY-SOMER
InstallatIon anD maIntenance
MICRO GEARLESS XAP1-CE
Permanent magnet synchronous motor for commercial lifts
4406 en -
Encoder connection
4.2.2 -
never touch the connection pins at the encoder cable. the
encoder may be destroyed by electrostatic discharge.
Pins of the connector
Pin
1 2 3 4 5 6 7 8 9 10 11 12 13 14 15
signal a
Ā
B B¯
U
Ū
V V¯ W W
¯ +5Vcc 0V
- connect the power cables to the terminals U1, V1, W1, in
conformity with Iec 600034-1 (see § 4.2).
- connect the Ptc thermistor to the controller (option).
- connect the ground terminal to earth (see § 4.2).
- connect the brakes and the micro-switches
- connect the encoder.
Carefully verify that no screw, washer, or any other
foreign part may have entered the motor and may
be in contact with the winding
.
Start up
4.3 -
check that the electrical drives are connected to earth before
doing the first operation.
start up the machine and check the following points:
- All electrical fixations and connections are correctly
tightened.
after start up, check:
- noise
- Vibrations
- action of switches/buttons
- also check the current and the voltage on the machine while
operating at rated load.
MAINTENANCE / SERvICE
5 -
After 1 month of running
5.1 -
- check the tightness of bolts or electrical connections.
- check the vibrations. check on abnormal connections.
- Remove grease traces (if any) from the brake discs.
- make sure that the brake noise level is below 60dBa. If a
higher noise level is reported, inform leRoY-someR
- If a brake wear check is necessary: check that the brake
airgap measures between 0,25 mm and 0,3 mm according to
the control procedure described in § 6.
note: this measurement will be used as reference.
Every year
5.2 -
- make sure that the brake noise level is inferior to 60dBa. If
higher, adjust according to § 6.
- If a brake wear check is necessary, check that the airgap is
less than 0,3 mm. If higher: check that the motor doesn’t start
with the brake closed, otherwise contact leRoY-someR
ADJUSTMENT PROCEDURE FOR
6 -
BRAKES, ENCODER AND
MICROSWITCHES
Control of the airgap of the brake
6.1 -
-the brake must not be energized.
- measure the airgap with a set of feeler gauges.
- the brake is designed for static application. Dynamic braking
must be limited to emergencies and tests only.
At normal use the wear of the brake will be insignificant. If the
airgap will be bigger than 0,6 mm, the brake disc must be
changed, see § 7.2.
- energize the brakes
- check the value of the airgap
- check the noise level of each brake (no slapping) and that the
sheave turns freely when the brakes are released.
Encoder adjustment
6.2 -
- avoid removing the encoder from the motor.
- In case of replacement, it is imperative to remove the cables
from the sheave, in order not to have any resistant torque
during the encoder setting.
- connect the power supply of the encoder to the controller.
- Proceed to the setting of the new encoder according to the
technical instructions given by the manufacturer of the
controller.
Control and adjustment of the
6.3 -
micro-switches
Control
6.3.1 -
- each brake unit is equipped with a micro-switch.
- the micro-switches are closed when the brakes are closed
(active).
- the micro-switches are wired in series.
- control the micro-switches using an ohmmeter.
- control successively each micro-switch after having short
circuited the other. the control is done by operating the brake
several times (opening/closing), to be carried out without
failure on at least 3 equidistant points during a full rotation of
the brake disc.
Adjustment
6.3.2 -
Tools needed
6.3.2.1 -
- 2 flat spanners for hex nuts (8 mm)
- a pilot lamp for adjusting the micro-switches.
- suitable connections on the pilot lamp in order to be able to
plug to the connector of the micro-switch.
Adjustment of the micro-switches
6.3.2.2 -
Secure the load before any action on the brakes.
- connect the pilot lamp to the two wires of the micro-switch.
- Insert a calibre gauge of 0,1mm close to the adjustment
screw, in the corresponding airgap. then energize the machine,
tighten the adjustment screw H m5 (8/plat) to contact with the
micro-switch until commutation is achieved (see fig.2).