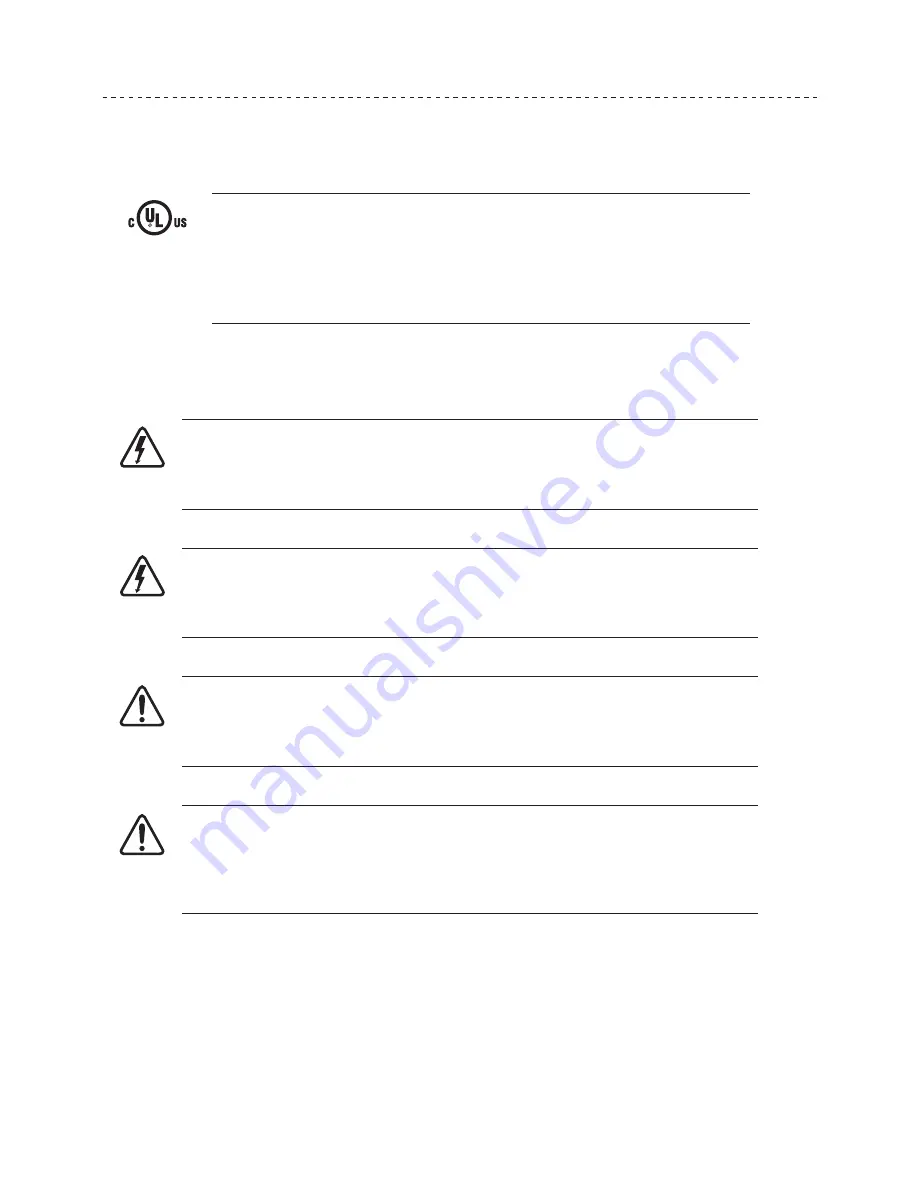
Lenze 13466147 EDBSM01 v19 EN
7
Safety Information
1
This drive has been tested by Underwriters Laboratory (UL) and is an approved component in
compliance with UL508 Safety Standard.
Warnings!
• Suitable for use on a circuit as described in Section 3.2 of this manual.
• Use minimum 75 °C copper wire only, except for control circuits.
• For control circuits, use wiring suitable for NEC Class 1 circuits only.
• Shall be installed in a pollution degree 2 macro-environment.
This drive must be installed and configured in accordance with both national and international
standards. Local codes and regulations take precedence over recommendations provided in this and
other Lenze AC Tech documentation.
DANGER!
Risk of Electric Shock! Capacitors retain charge for approximately 180 seconds after
power is removed. Disconnect incoming power and wait at least 3 minutes before
touching the drive.
DANGER!
Risque de choc électrique! Les condensateurs restent sous charge pendant environ 180
secondes après une coupure de courant. Couper l’alimentation et patienter pendant au
moins 3 minutes avant de toucher l’entraînement.
WARNING!
The opening of branch-circuit protective device may be an indication that a fault has
been interrupted. To reduce the risk of fire or electric shock, current carrying parts and
other components of the controller should be examined and replaced if damaged.
WARNING!
Le déclenchement du dispositif de protection du circuit de dérivation peut être dû à
une coupure qui résulte d’un courant de défaut. Pour limiter le risque d'incendie ou de
choc électrique, examiner les pièces porteuses de courant et les autres éléments du
contrôleur et les remplacer s'ils sont endommagés.
1.6
Customer Modification
Lenze AC Tech Corporation, its sales representatives and distributors, welcome the opportunity to
assist our customers in applying our products. Many customizing options are available to aid in
this function. Lenze AC Tech Corporation cannot assume responsibility for any modifications not
authorized by its engineering department.