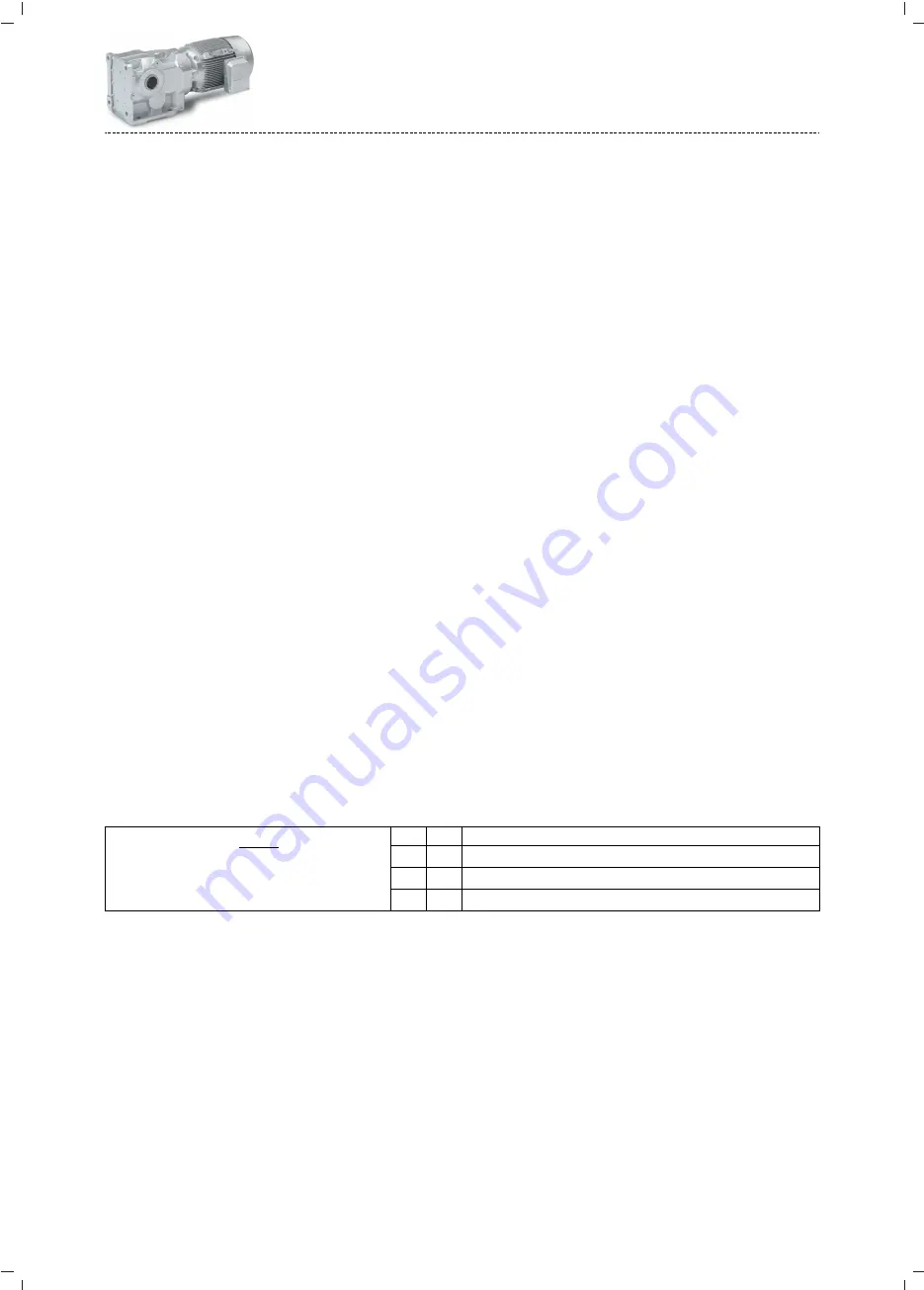
Brakes
The motors can be ordered with a spring-applied brake to allow stopping or deceleration of
the moving masses. The spring-applied brake operates according to the closed-circuit
principle. In the deenergized state, the brake is closed, preventing possible movement of the
motor shaft or the load after switching off or in the event of a power failure.
The application brake can be used as a holding brake and a service brake.
Brake connection
If the installation is already supplied with DC voltage, a direct connection without rectifier is
possible. High induction peaks may occur and a freewheeling diode or a spark suppressor
should be provided.
A rectifier is required if the brake is connected to the mains. This is included in the scope of
supply and is located in the motor’s terminal box.
Rectifier
The rectifier converts the connection’s AC voltage into a DC voltage.
Alternatively, a half-wave bridge rectifier can be used for the application brake. This provides
twice the voltage for a very short time (300 ms). As a result, the features of the brake –
depending on the assignment of the brake’s coil voltage and supply voltage – can be optimized
in the form of a short-term overexcitation of the brake coil or a reduction of the holding
current.
AC or DC voltage switching
Brakes can be switched both before the rectifier (AC voltage switching) as well as after the
rectifier (DC voltage switching). The choice of control system influences the engagement time
of the armature plate, inter alia.
AC switching increases the engagement time by a factor of 5 to 10 compared to DC switching.
This is to be observed taken into account when choosing the control system. DC switching is
possible by simply removing a bridge and using the switching contact connection. However,
this calls for two additional cores in the control cabinet.
DC switching is particularly expedient for lifting applications because a short engagement time
is necessary here to guarantee a secure hold without any prior slipping of the load.
Motor supply cables
If long motor supply cables are used, pay attention to the ohmic voltage drop along the cable
and compensate for it with a higher voltage at the input end of the cable.
The following applies to Lenze system cables:
=
+
´
´
´
B
Lg
B
[V]
U[V] U [V] 0.08
l [m] I [A]
[A] [m]
U
V
Resulting supply voltage
U
B
V
Rated voltage of the brake
l
Lg
m
Cable length
I
B
A
Rated current of the brake
Manual release lever
The holding and application brake can be ordered with a manual release lever to facilitate
positioning and maintenance work. By using the manual release lever, the brake can be
released manually in a deenergized operating state.
A locking manual release lever can be ordered as an option. This is equipped with a clamping
device to hold the brake in the released position.
Product extensions
Brakes
93
Summary of Contents for IE3 g500-B
Page 1: ...Geared motors IE3 g500 B m540 P bevel geared motor Project planning EN...
Page 2: ......
Page 118: ......
Page 119: ......
Page 120: ...04 2021 1 0 www Lenze com...