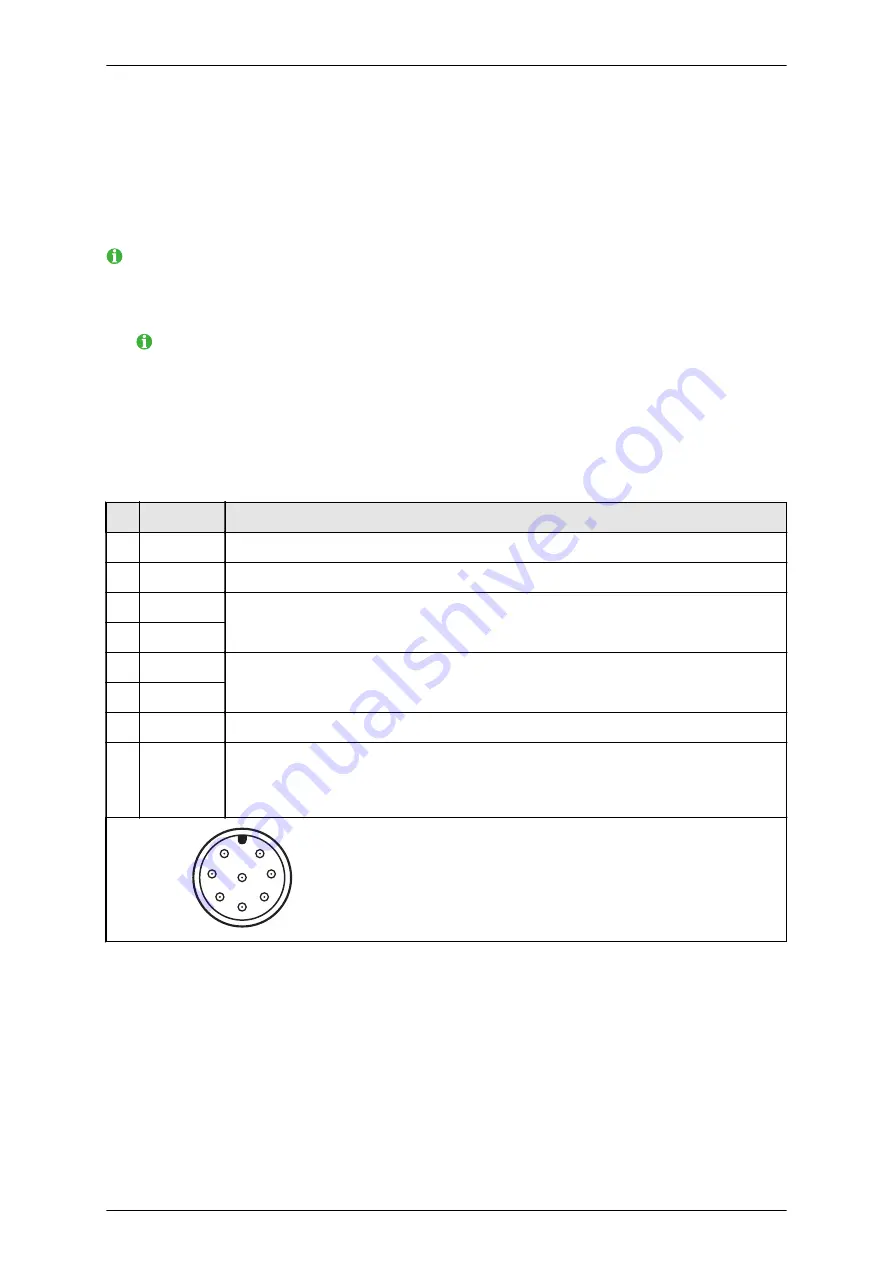
5 Commissioning
Bauer
Connection
20
GEL 235/235x/203x
5 Commissioning
Check whether all cables are laid and the encoder is mounted firmly.
5.1 Connection
Connection of the fieldbus variants:
→
separate Reference document.
Check whether the connector plug is wired correctly, according to the connection
schemes further below.
Connect inputs that are not used/assigned to GND.
Connect the encoder.
Supply the encoder with voltage.
5.1.1 SSI
8-pole connector M12 (GEL 2352)
Pin
Signal
Explanation
1
GND
Ground
2 PRESET Set actual value to centre of measurement range
3
DATA- Output: Differential data signal according to RS 485
4
DATA+
5
CLOCK-
Input: Differential clock signal according to RS 485
6 CLOCK+
7
V
S
Supply voltage
8 CW/CCW Direction of rotation (flange side view):
ascending clockwise (CW) = GND (default), ascending counter-clock-
wise (CCW) = V
S
1
8
2
7
3
6
4
5
Connector
socket
(pins, connection side view)