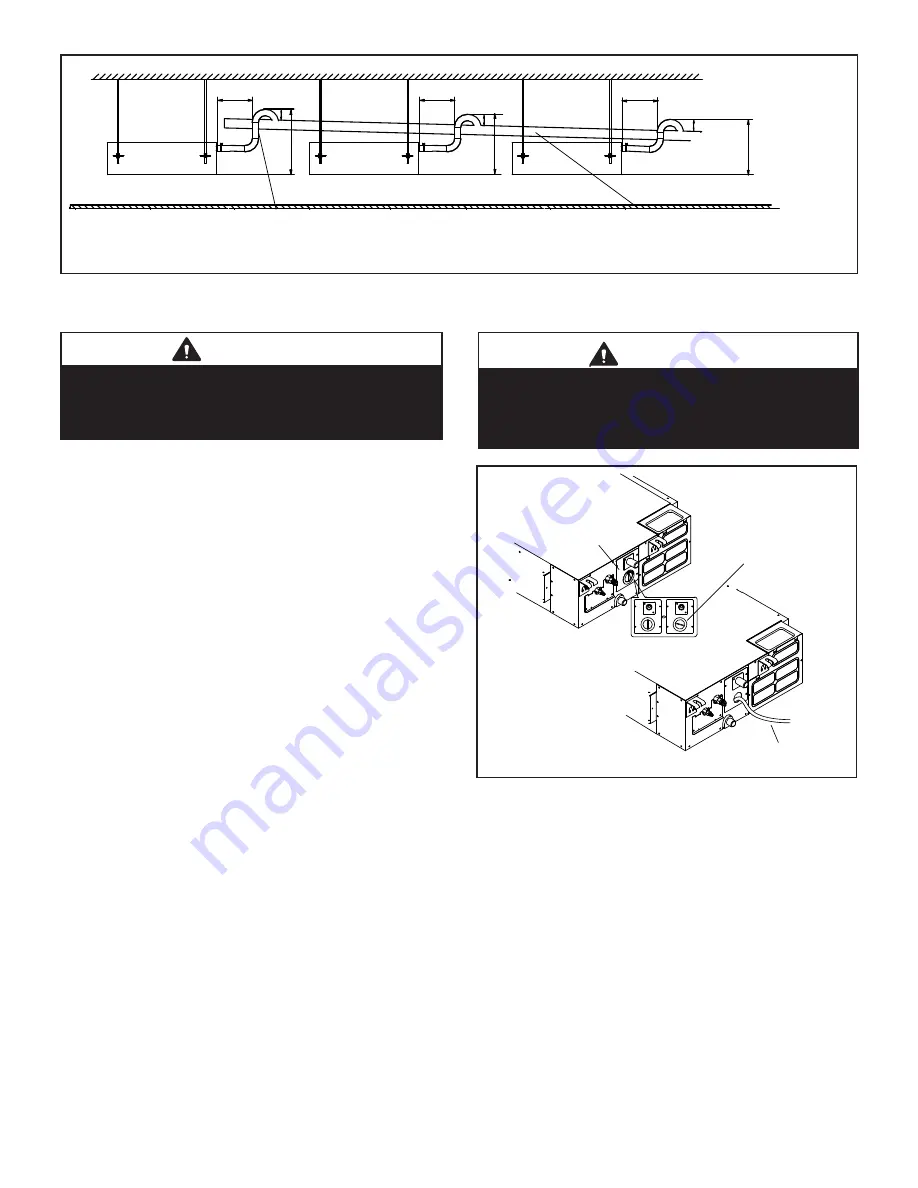
13
Indoor Unit
2~3-15/16 in.
8 in.
2~3-15/16 in.
2~3-15/16 in.
MAIN DRAIN
INDIVIDUAL DRAIN OUTLET FROM EACH INDOOR UNIT
(Must be connected to internal pump and must be routed to
main drain as shown.)
ti
n
U
r
o
o
d
n
I
ti
n
U
r
o
o
d
n
I
(Sloped at 1/4” per foot (6 mm per 305 mm) AWAY
from unit and should be supported as needed to prevent sagging.)
8 in.
8 in.
Max. 28 in.
Max. 28 in.
Max. 28 in.
Figure 19. Condensate Drain with Lift Pump
Multiple Indoor Units
7. After system installation is complete, the
condensate drain line must be checked for leaks
and the condensate pumps must be checked to
ensure proper operation. This check is part of the
commissioning sequence.
Turn the condensate
drain pan test cover latch counterclockwise to open
the cover and access the drain pan. See Figure 20.
Funnel enough water to engage the pump into the
drain pan through a flexible tube.
8. Operate the system in the cooling mode. If the
internal pump is being used, ensure that the pump is
operating and the water in the pan is draining freely.
If the internal pump is not being used, pour the water
into the drain pan and confirm that it has flowed freely
out of the pan and out of the drain termination. If a
leak is found, shut down power to the unit at once and
do not restore power to the unit until the problem has
been resolved.
DRAIN PAN
TEST COVER
FUNNEL WATER INTO
PAN THROUGH TUBE
FOR TEST
COVER LATCH
(Turn latch
counterclockwise
to unlock)
CLOSEDOPEN
CLOSE
D OPEN
Figure 20. Condensate Drain Test
9. Return the test cover and turn the latch clockwise to
re-lock it.
IMPORTANT
When using a gravity drain instead of the factory-
installed lift pump.
Disconnect the factory-installed lift pump, CN 13. See
unit wiring diagrams for location of CN 13.
IMPORTANT
Drain should have a slope of at least ¼ inch per foot and
should be approved corrosion-resistant pipe. You must
confirm operation of every drain and pump in the system
as part of the commissioning procedure.
Summary of Contents for VRF VMDB Series
Page 23: ...23...