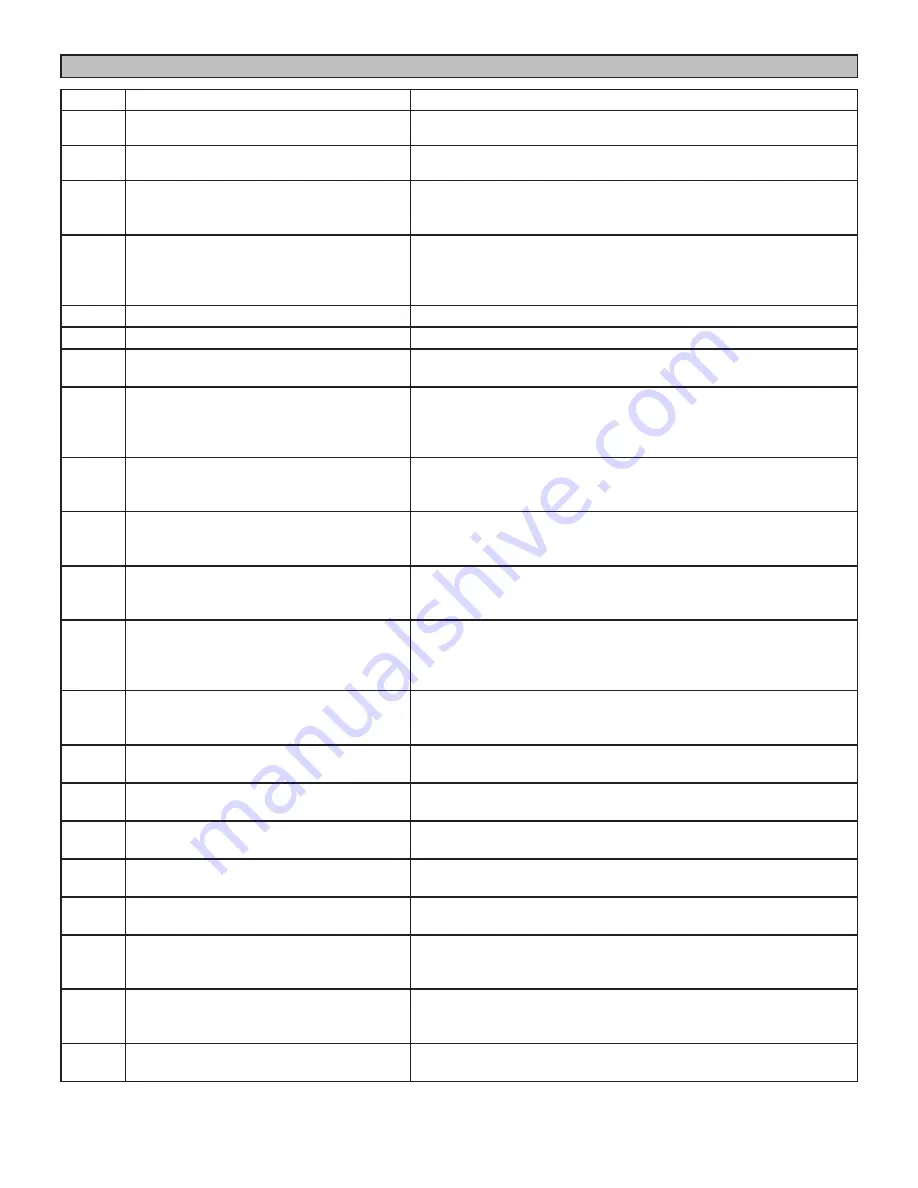
Page 57
Integrated Control Diagnostic Codes
Code
Diagnostic Codes/Status of Equipment
Action Required to Clear and Recover
E200
Hard lockout - Rollout circuit open or previously
open.
Correct unit cause of rollout trip or replace flame rollout switch and test furnace
operation.
E201
Indoor blower communication failure - Unable to
communicate with blower motor.
Indoor blower communication failure including power outage.
E202
Indoor blower motor mis-match - Indoor
motor horsepower does not match unit
capacity.
Incorrect furnace size code selected. Check unit size codes on
configuration guide or in installation instructions.
E203
Appliance capacity / size is NOT
programmed. Invalid unit codes refer to
configuration flow chart in installation
instructions.
No furnace size code selected. Check unit size codes on configuration
guide or in installation instructions.
E204
Gas valve mis-wired.
Check operation of gas valve.
E205
Gas valve control relay contact shorted.
Check operation of gas valve.
E207
Hot surface ignitor sensed open - Refer to
troubleshooting in installation instruction.
Measure resistance of Hot Surface Ignitor, replace if open or not within
specification.
E223
Low pressure switch failed open - Refer to
troubleshooting in installation instruction.
Check inches of water column pressure during operation of low pressure
switch on heat call, measure inches of water column of operating
pressure, inspect vent and combustion air inducer for correct operation
and restriction.
E224
Low pressure switch failed closed - Refer to
troubleshooting in installation instruction.
Check low pressure switch for closed contacts, measure inches of water
column of operating pressure, inspect vent and combustion air inducer
for correct operation and restriction.
E225
High pressure switch failed open - Refer to
troubleshooting in installation instruction.
Check inches of water column pressure of high pressure switch on heat
call, measure inches of water column of operating pressure, inspect vent
and combustion air inducer for correct operation and restriction.
E226
High pressure switch failed closed - Refer to
troubleshooting in installation instruction.
Check high pressure switch for closed contacts, measure inches of
water column of operating pressure, inspect vent and combustion air
inducer for correct operation and restriction.
E227
Low pressure switch open during trial for
ignition or run mode. Refer to troubleshooting
in installation instruction.
Check inches of water column pressure during operation of low pressure
switch on heat call, measure inches of water column of operating
pressure, inspect vent and combustion air inducer for correct operation
and restriction.
E228
Unable to perform successful pressure switch
calibration.
Retry after 300 seconds. Error counter cleared when exiting lockout,
unable to perform pressure switch calibration. Check vent system and
pressure switch wiring connections.
E240
Low flame current - Run mode - Refer to
troubleshooting in installation instruction.
Check micro amperes of flame sensor, clean or replace sensor. Measure
voltage of neutral to ground for good unit ground.
E241
Flame sensed out of sequence - Flame still
present.
Shut off gas, check for gas valve leak.
E250
Limit switch circuit open - Refer to
troubleshooting in installation instruction.
Check why limit is tripping, overfired, low air flow.
E252
Discharge air temperature too high (gas heat
only).
Check temperature rise, air flow and input rate.
E270
Soft lockout - Exceeded maximum number of
retries. No flame current sensed.
Check for gas flow, ignitor lighting burner, flame sensor current.
E271
Soft lockout - Exceeded maximum number of
retries. Last retry failed due to the pressure
switch opening.
See E 223.
E272
Soft lockout - Exceeded maximum number
of recycles. Last recycle due to the pressure
switch opening.
See E 223 and E 225.
E273
Soft lockout - Exceeded maximum number of
recycles. Last recycle due to flame failure.
See E 240.