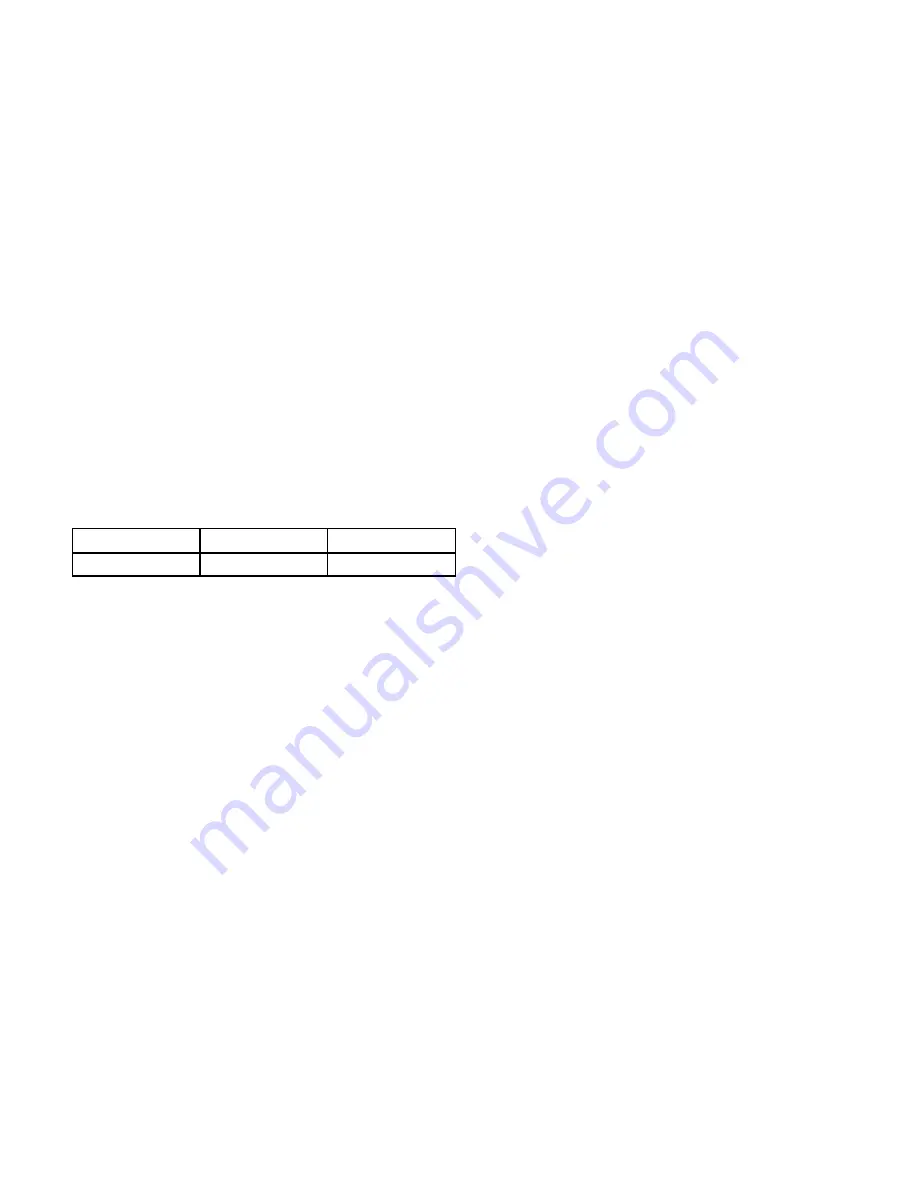
Page 27
C-Heating Components
The SureLight
®
ignitor is made of durable silicon nitride. Ig
nitor longevity is enhanced by controlling voltage to the igni
tor. The integrated control provides a regulated 120 volts to
the ignitor for a consistent ignition and long ignitor life. Due
to this feature of the control, voltage measured with a digital
meter will be slightly lower. To measure correct voltage use
a true RMS meter or ignitor can be ohmed. Ohm value
should be 39 to 70.
A flame sensor is located on the left side of the burner sup
port. The sensor is mounted on the flame rollout plate and
the tip protrudes into the flame envelope of the left-most
burner. The sensor can be removed for service without re
moving any part of the burners. During operation, flame is
sensed by current passed through the flame and sensing
electrode. The SureLight control allows the gas valve to re
main open as long as flame signal is sensed. To check flame
sense signal use the push-button found on the integrated
control and go to Field Test Mode. The menu will display the
flame signal. Table 18 shows the flame signal for the
SLP98DFV unit.
TABLE 18
Flame Signal in Microamps
Normal
Low
Drop Out
2.6 or greater
2.5 or less
1.1
NOTE - A much higher than normal micro amp reading (15
for example) may appear when checking flame signal.
3. Flame Rollout Switches (Figure 14)
Flame rollout switch S47 is a high temperature limit located
inside the burner box. Each furnace is equipped with two
identical switches. The limit is a N.C. SPST manual‐reset
limit connected in series with the primary limit S10. When
S47 senses rollout, the circuit breaks and the integrated
control immediately stops ignition and closes the gas valve.
If unit is running and flame rollout is detected, the gas valve
will close and integrated control will be disabled. Rollout can
be caused by a blocked heat exchanger, flue or lack of com
bustion air. The switch is factory set to trip (open) at 210°F
and cannot be adjusted. The switch can be manually reset. To
manually reset a tripped switch, push the reset button located
on the center of the switch.
All units use inshot burners. Burners are factory set and re
quire no adjustment. Always operate the unit with the burner
box front panel in place. Each burner uses an orifice that is
precisely matched to the burner input. Burners can be re
moved as a one piece assembly for service. If burner assem
bly has been removed, it is critical to align center of each burn
er to the center of the clamshell when re-installing. See more
detail in Section VII- MAINTENANCE..
5. Duralock Plus
SLP98DFV units use an aluminized steel primary and
stainless steel secondary heat exchanger assembly.
Heat is transferred to the air stream from all surfaces of
the heat exchanger. The shape of the heat exchanger en
sures maximum efficiency.
The combustion air inducer pulls fresh air through the burn
er box. This air is mixed with gas in the burner venturi and at
the corbel orifices. The gas / air mixture is then burned at
the entrance of each clamshell. Combustion gases are then
pulled through the primary and secondary heat exchangers
and exhausted out the exhaust vent pipe.