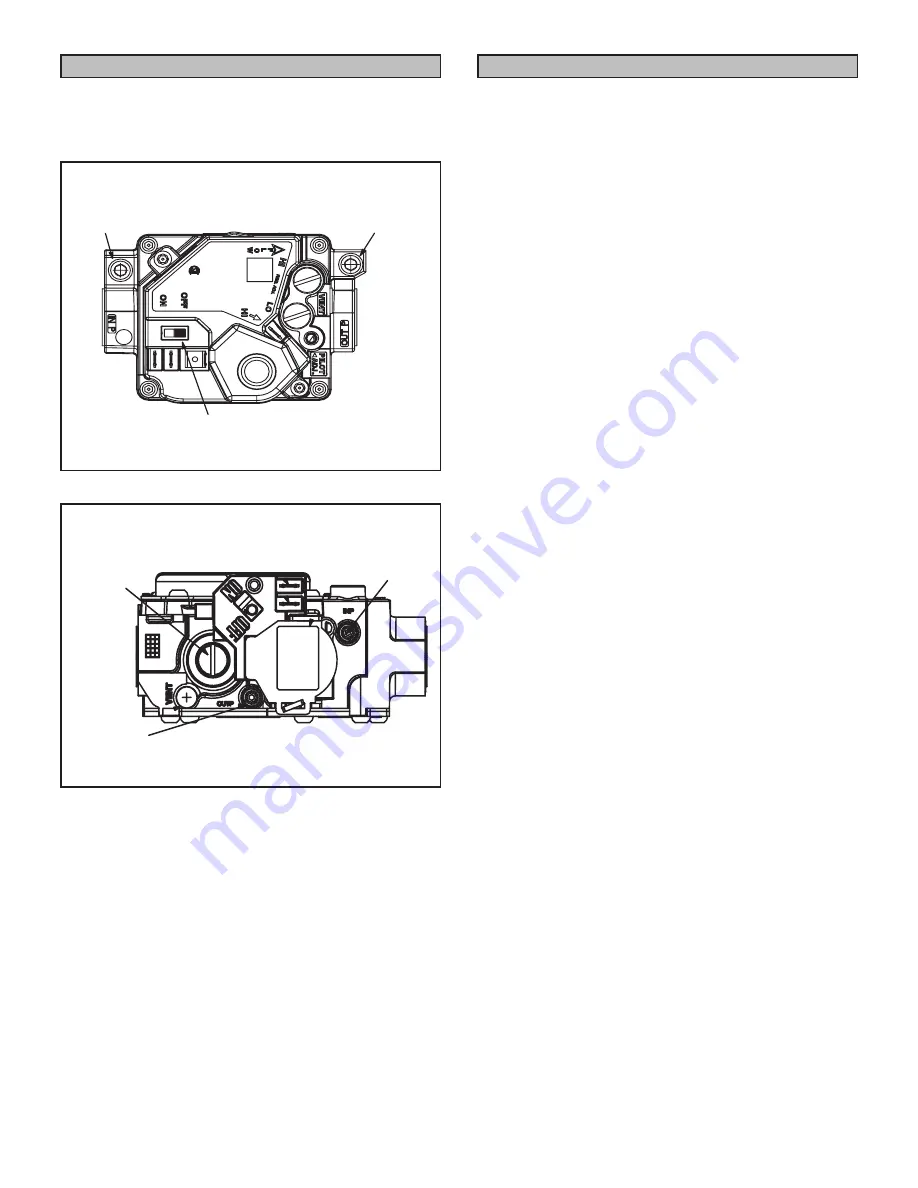
Page 21
To Turn Off Gas to Unit
1 - Set thermostat to lowest level.
2 - Turn off all electrical power to unit if service is to be
performed.
3 - Move switch to OFF
INLET
PRESSURE
PORT
WHITE RODGERS 36H SERIES GAS VALVE
Two-Stage
GAS VALVE SWITCH SHOWN IN OFF POSITION
MANIFOLD
PRESSURE
OUTLET
MANIFOLD
PRESSURE
ADJUSTMENT
SCREW
FIGURE 12
WHITE RODGERS 36G GAS VALVE
Single-Stage
GAS VALVE SWITCH SHOWN IN OFF POSITION.
MANIFOLD
PRESSURE
ADJUSTMENT
SCREW
INLET
PRESSURE
PORT
MANIFOLD
PRESSURE
OUTLET
FIGURE 13
Heating Sequence of Operation
1 - When the thermostat calls for heat, the combustion
air inducer starts immediately.
2 -
Combustion air pressure switch proves inducer
operation before allowing ignition sequence to
start. This switch is factory set and no adjustment is
necessary.
3 - After pre-purge of approximately 30 seconds, the
spark ignition is energized and the solenoid valves
open in the gas valve.
4 - The spark then ignites the gas, the ignition sensor
proves the flame and the combustion process
continues.
5 - In the event that the flame is not detected after the
first 10-second trial for ignition, the controller will
repeat steps 3 and 4 an additional two times before
locking out the gas valve. Ignition control will then
automatically repeat steps 3, 4, and 5 after 60
minutes.
NOTE -
To interrupt the 60-minute lockout period, move
thermostat from “Heat” to “OFF” then back to “Heat.” Heat
-
ing sequence then restarts at step 1.
6 - The burners must light without noticeable crossover
delay. There must be no flame lifting from the burner
heads, flashback or burning within the burner. The
flames should be predominantly blue in color and
should be approximately centered in the tubes with
no apparent impingement taking place.
7 - The ignition control will energize the fan approximately
30 seconds after ignition is established.
8 - After the thermostat demand is satisfied the gas
valve is closed. Thirty seconds after the demand is
satisfied, the combustion air inducer is shut off.
9 - The ignition control will shut off the system fan
approximately 150 seconds after the gas valve is de-
energize.
Summary of Contents for LS25 Series
Page 5: ...Page 5 ...