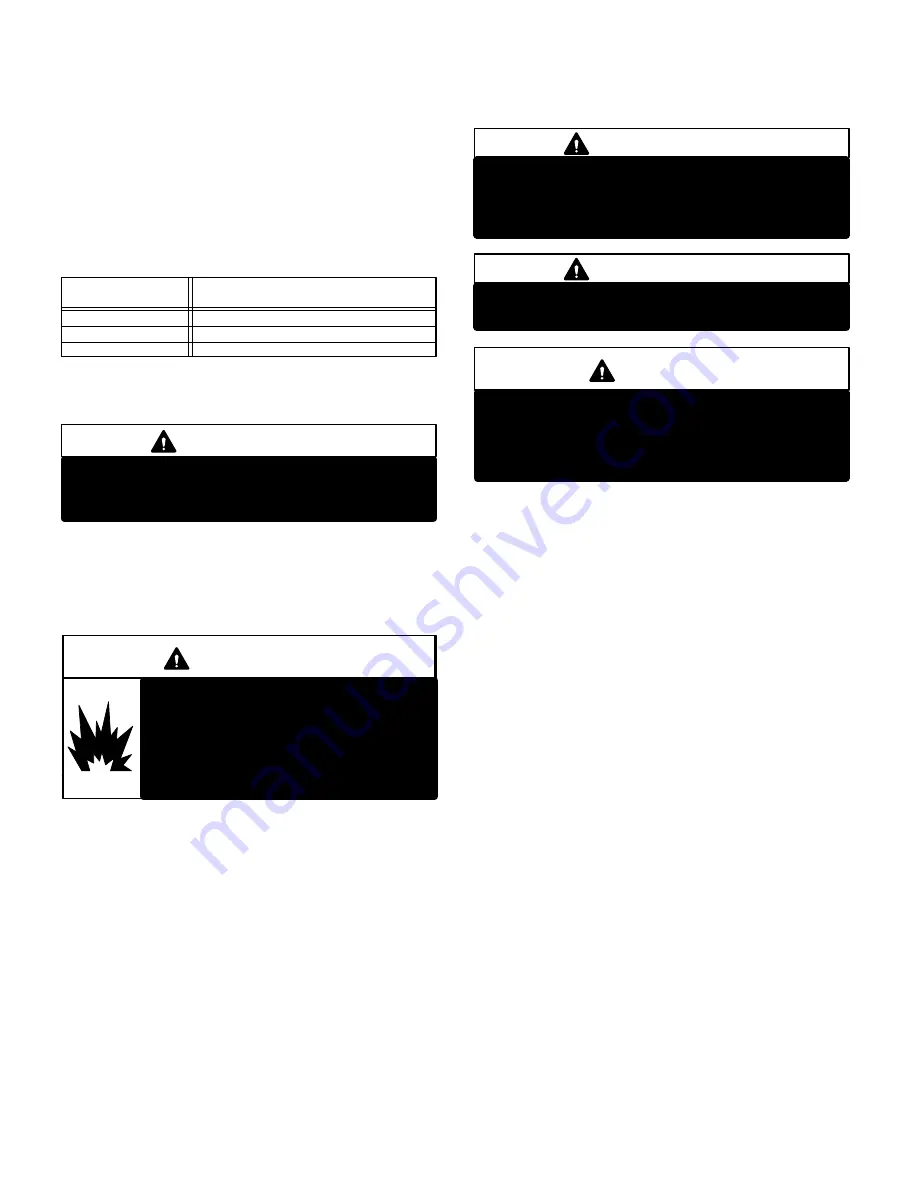
Page 8
3– Replace stem cap. Tighten finger tight, then tight-
en an additional 1/6 turn.
V–CHARGING
The unit is factory–charged with the amount of
HCFC-22 refrigerant indicated on the unit rating plate.
This charge is based on a matching indoor coil and out-
door coil with a 25 foot (6096mm) line set. For varying
lengths of line set, refer to table 4 for refrigerant charge
adjustment. A blank space is provided on the unit rat-
ing plate to list actual field charge.
LIQUID LINE
1/4 in. (6 mm)
5/16 in. (8mm)
3/8 in. (10 mm)
TABLE 4
Ounce per 5 foot (ml per mm) adjust
from 20 foot (6096 mm) line set*
1 ounce per 5 feet (30 ml per 1524 mm)
*If line set is greater than 20 ft. (6.09m) add this amount. If line set
is less than 20 feet (6.09m) subtract this amount
SET DIAMETER
2 ounce per 5 feet (60 ml per 1524 mm)
3 ounce per 5 feet (90 ml per 1524 mm)
Units are designed for line sets up to 50ft. Consult Lennox
Refrigerant Piping Manual for line sets over 50ft.
IMPORTANT
If line length is greater than 20 feet (6096mm), add
this amount. If line length is less than 20 feet (6096
mm), subtract this amount.
A–Leak Testing
1– Attach gauge manifold and connect a drum of dry
nitrogen to center port of gauge manifold.
2– Add a small amount of refrigerant to the lines. Open
high pressure valve on gauge manifold. Pressurize
line set and indoor coil to 150 psig (1034 kPa).
WARNING
Danger of Explosion.
Can cause injury, death and equipment
damage.
When using dry nitrogen, use a pres-
sure–reducing regulator, set at 150
psig (1034 kPa) or less to prevent ex-
cessive pressure.
3– Check lines and connections for leaks.
NOTE – If electronic leak detector is used, add a trace of
refrigerant to nitrogen for detection by leak detector.
4– Release nitrogen pressure from the system, cor-
rect any leaks and recheck.
B–Evacuating the System
Evacuating the system of non–condensables is critical
for proper operation of the unit. Non–condensables are
defined as any gas that will not condense under temper-
atures and pressures present during operation of an air
conditioning system. Non–condensable such as water
vapor, combines with refrigerant to produce substances
that corrode copper piping and compressor parts.
1– Attach gauge manifold and connect vacuum
pump (with vacuum gauge) to center port of
gauge manifold. With both gauge manifold ser-
vice valves open, start pump and evacuate evapo-
rator and refrigerant lines.
IMPORTANT
A temperature vacuum gauge, mercury vacuum
(U–tube), or thermocouple gauge should be used.
The usual Bourdon tube gauges are not accurate
enough in the vacuum range.
IMPORTANT
The compressor should never be used to evacuate
a refrigeration or air conditioning system.
CAUTION
Danger of Equipment Damage. Avoid deep vacu-
um operation. Do not use compressors to evacuate
a system. Extremely low vacuums can cause inter-
nal arcing and compressor failure. Damage caused
by deep vacuum operation will void warranty.
2– Evacuate system to
absolute
pressure of .92 inches
of mercury, 23 mm of mercury, or 23,000 microns.
3– After system has been evacuated to an absolute
pressure of .92 inches mercury, 23 mm mercury, or
23,000 microns, close manifold valve to center port.
4– Stop vacuum pump and disconnect from gauge
manifold. Attach a drum of dry nitrogen to center
port of gauge manifold, open drum valve slightly
to purge line, then break vacuum in system to 3
psig (20.7 kPa) pressure by opening manifold high
pressure valve to center port.
5– Close nitrogen valve, disconnect drum from man-
ifold center port and release nitrogen from system.
6– Reconnect vacuum pump to manifold center port
hose. Evacuate the system to an absolute pressure
less than .197 inches of mercury, 5 mm of mercury,
or 5000 microns, then turn off vacuum pump. If the
absolute pressure rises above .197 inches of mer-
cury, 5 mm of mercury, or 5000 microns within a
20–minute period after stopping vacuum pump,
repeat step 6. If not, evacuation is complete.
This evacuation procedure is adequate for a new
installation with clean and dry lines. If excessive
moisture is present, the evacuation process may
be required more than once.
7– After evacuation has been completed, close gauge
manifold service valves. Disconnect vacuum
pump from manifold center port and connect re-
frigerant drum. Pressurize system slightly with re-
frigerant to break vacuum.
C–Charging
If the system is completely void of refrigerant, the rec-
ommended and most accurate method of charging is
to weigh the refrigerant into the unit according to the
total amount shown on the unit nameplate. Also refer
to the SPECIFICATIONS tables on page 2.