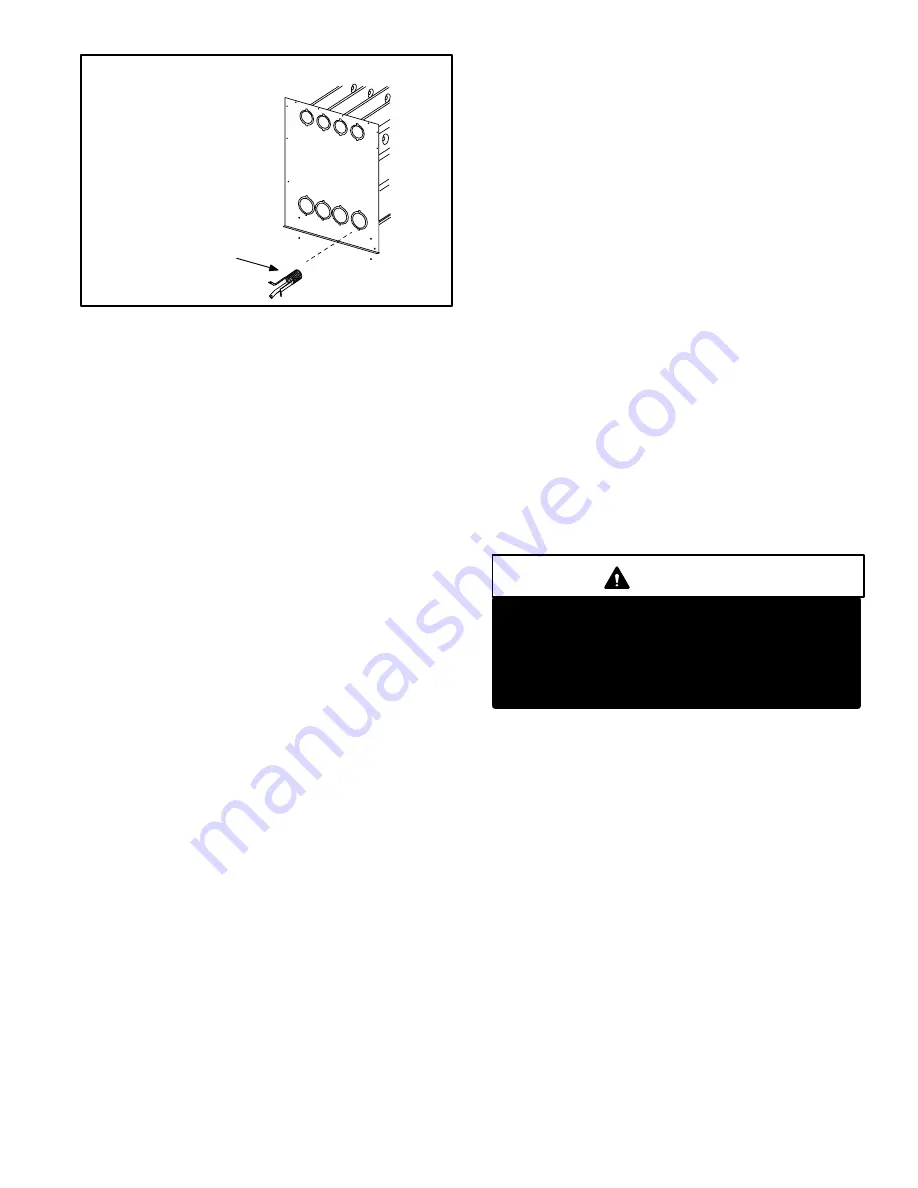
Page 31
FIGURE 23
NOx INSERTS
NOX UNITS ONLY
4 − Remove collector box located behind combustion air
inducer. Care must be taken to avoid damaging the
collector box gasket. If the gasket is damaged it must
be replaced to prevent leakage.
5 − Mark then disconnect wires from gas valve and rollout
switch.
6 − Disconnect gas supply piping. Remove six screws se-
curing the burner manifold assembly to the lower vesti-
bule panel and remove the assembly from the unit.
NO
x
units only: remove screws holding NO
x
inserts.
Carefully remove inserts from each heat exchanger
clam. See figure 23.
7 − Insert brush end of cable snake into top of one of the
heat exchanger openings. DO NOT FORCE CABLE
INTO HEAT EXCHANGER. Once the cable has been
inserted, operate drill on slow speed. Move the cable
in and out of the heat exchanger section three or four
times or until sufficient cleaning is accomplished. Re-
verse drill and slowly work cable out of opening.
8− Repeat procedure for each heat exchanger section.
9− When the top heat exchanger sections are complete,
place brush end of cable snake into the bottom openings
of each of the heat exchanger sections. Clean the bottom
opening as described in step 7.
10− Remove cable from heat exchanger. Use a vacuum to
remove debris knocked loose during cleaning from
each heat exchanger section.
11− Attach the exhaust end (positive pressure) of the
vacuum to the top of the heat exchanger sections.
Any loose debris will be forced to the bottom of the
heat exchanger section. Vacuum debris from bottom
openings.
12− Replace collector box and combustion air inducer/
prove switch combination. Check gaskets for damage.
Damaged seals must be replaced to avoid heat ex-
changer leaks. Replace all screws to the collector box
and combustion air inducer. Leaving off screws may
cause leaks.
13− Clean burner by running a vacuum with a soft brush at-
tachment over face of burners. Visually inspect inside of
burners and crossovers for any blockage caused by for-
eign matter. Remove any blockage.
14− For NOX units, replace inserts in each heat exchanger
section.
DO NOT BEND.
15− Replace burner / manifold assembly onto vestibule
panel.
16− Reconnect wires to pressure switch, roll−out switch, gas
valve and combustion air inducer. Refer to unit wiring
diagram.
17− Reconnect vent pipe to combustion blower outlet.
18− Reconnect gas supply piping.
19− Turn on power and gas supply to unit.
20− Set thermostat and check for proper operation.
21− Check all piping connections, factory and field, for gas
leaks. Use a leak detecting solution or other preferred
means.
Don not use matches, candles, flame or
other sources of ignition to check for gas leak.
22− If a leak is detected, shut gas and electricity off and
repair leak.
23− Repeat steps 21 and 22 until no leaks are detected.
24− Replace front access panel.
CAUTION
Potential for gas leaks, fire or explosion.
Some soaps used for leak detection are corrosive
to certain metals. Carefully clean piping thor-
oughly after leak detection has been completed.
Can cause damage to piping resulting in gas
leaks, fire or explosion.
C−Supply Air Blower
1 − Check and clean blower wheel.
2 − Motors used on the Lennox G50UH(X) series units
are permanently lubricated and need no further lu-
brication.
D−Flue and Chimney
Flue must conform to local codes. In the absence of local
codes, flue must meet the National Fuel Gas Code
ANSI−Z223.1 venting requirements. Flue pipe deteriorates
from the inside out and must be disconnected in order to
check thoroughly. Check flue pipe, chimney and all con-
nections for tightness and to make sure there is no block-
age or leaks.
E−Electrical
1 − Check all wiring for loose connections.
2 − Check for correct voltage.
3 − Check amp−draw on blower motor.