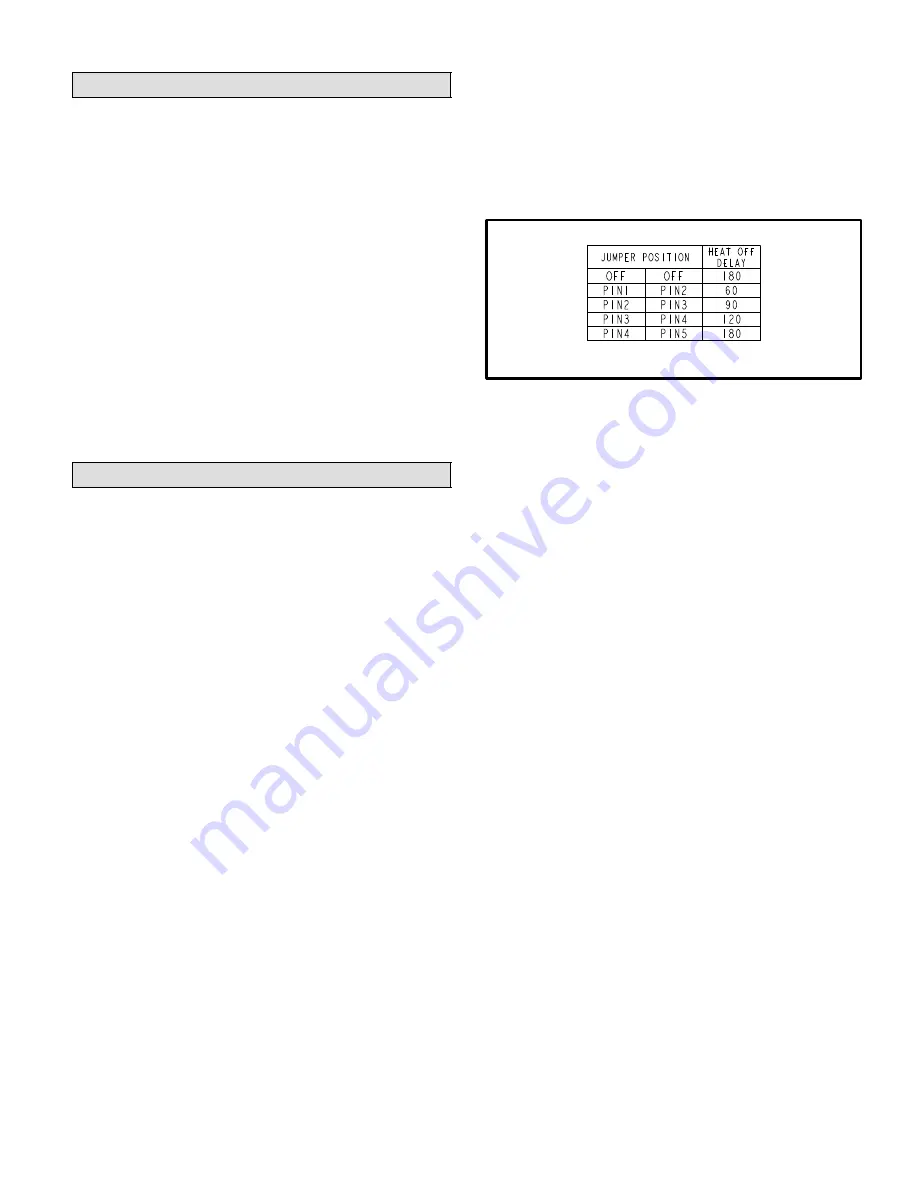
Page 25
High Altitude Information
NOTE − In Canada, certification for installations at eleva-
tions over 4500 feet (1372 m) is the jurisdiction of local au-
thorities.
Manifold pressure for all units fueled by natural gas at all
altitudes is 3.5" w.c. Manifold pressure for all units fueled
by L.P./propane gas at all altitudes is 10.0" w.c.
NOTE − A natural to L.P. propane gas changeover kit is
necessary to convert this unit. L.P. conversion kit 25W20
is used with all units installed at altitudes up to 7,500 feet.
L.P. conversion kit 25W21 is used with all units installed at
altitudes from 7,501 to 10,000 feet above sea level. Refer
to the changeover kit installation instruction for the
conversion procedure.
NOTE − Units fueled by natural gas and installed at alti-
tudes of 7501−10,000 feet above sea level require installa-
tion of a high altitude orifice kit (59M17).
The combustion air pressure switch is factory−set and re-
quires no adjustment. The factory−installed pressure
switch is acceptable for use in units installed at altitudes up
to 10,000 feet above sea level.
Other Unit Adjustments
Primary and Secondary Limits
The primary limit is located on the heating compartment
vestibule panel. The secondary limit is located in the blower
compartment, attached to the back side of the blower.
These limits are factory set and require no adjustment.
Flame Rollout Switches (Two)
These manually reset switches are located on the burner
box. If tripped, check for adequate combustion air before
resetting.
Pressure Switch
The pressure switch is located in the heating compartment
adjacent to the combustion air inducer. This switch checks
for proper combustion air inducer operation before allow-
ing ignition trial. The switch is factory−set and requires no
adjustment.
Temperature Rise
Place the unit into operation with a heating demand. After
supply and return air temperatures have stabilized, check
the temperature rise. If necessary, adjust the blower speed
to maintain the temperature rise within the range shown on
the unit nameplate. Increase the blower speed to decrease
the temperature. Decrease the blower speed to increase
the temperature rise. Failure to do adjust the temperature
rise may cause erratic limit operation.
Fan Control
There is no cooling mode fan on delay; however, there is a
cooling fan off delay of 45 seconds. This delay is not adjust-
able.
The heating mode fan on time of 45 seconds is not adjust-
able. The heating mode fan off delay(amount of time that
the blower operates after the heat demand has been satis-
fied) may be adjusted by changing the jumper position
across the five pins on the integrated control. The unit is
shipped with a factory fan off setting of 90 seconds. The fan
off delay affects comfort and is adjustable to satisfy individ-
ual applications. Adjust the fan off delay to achieve a supply
air temperature between 90° and 110°F at the exact mo-
ment that the blower is de−energized. Longer off delay set-
tings provide lower return air temperatures; shorter set-
tings provide higher return air temperatures. See figure 25.
FAN-OFF TIME ADJUSTMENT
To adjust fan−off timing, reposition jumper across pins to
achieve desired setting.
FIGURE 25
Thermostat Heat Anticipation
Set the heat anticipator setting (if adjustable) according to
the amp draw listed on the wiring diagram that is attached
to the unit.
Electrical
1 − Check all wiring for loose connections.
2 − Check for the correct voltage at the furnace (furnace
operating).
3 − Check amp-draw on the blower motor.
Motor Nameplate__________Actual__________
NOTE − Do not secure the electrical conduit directly to the
air ducts or structure.
Blower Speeds
NOTE − CFM readings are taken external to unit with a dry
evaporator coil and without accessories. See blower per-
formace data beginning on Page 26.
Turn off electrical power to furnace.
Remove blower access panel.
Disconnect existing speed tap at control board speed
terminal.
NOTE − Termination of any unused motor leads must be
connected to the park terminals on the control board.
Refer to blower speed selection chart on unit wiring dia-
gram for desired heating or cooling speed.
Connect selected speed tap at control board speed
terminal.
Resecure blower access panel.
Turn on electrical power to furnace.
Electronic Ignition
The integrated ignition control has an added feature of an
internal Watchguard control. The feature serves as an au-
tomatic reset device for ignition control lockout caused by
ignition failure. After one hour of continuous thermostat de-
mand for heat, the Watchguard will break and remake ther-
mostat demand to the furnace and automatically reset the
control to begin the ignition sequence.