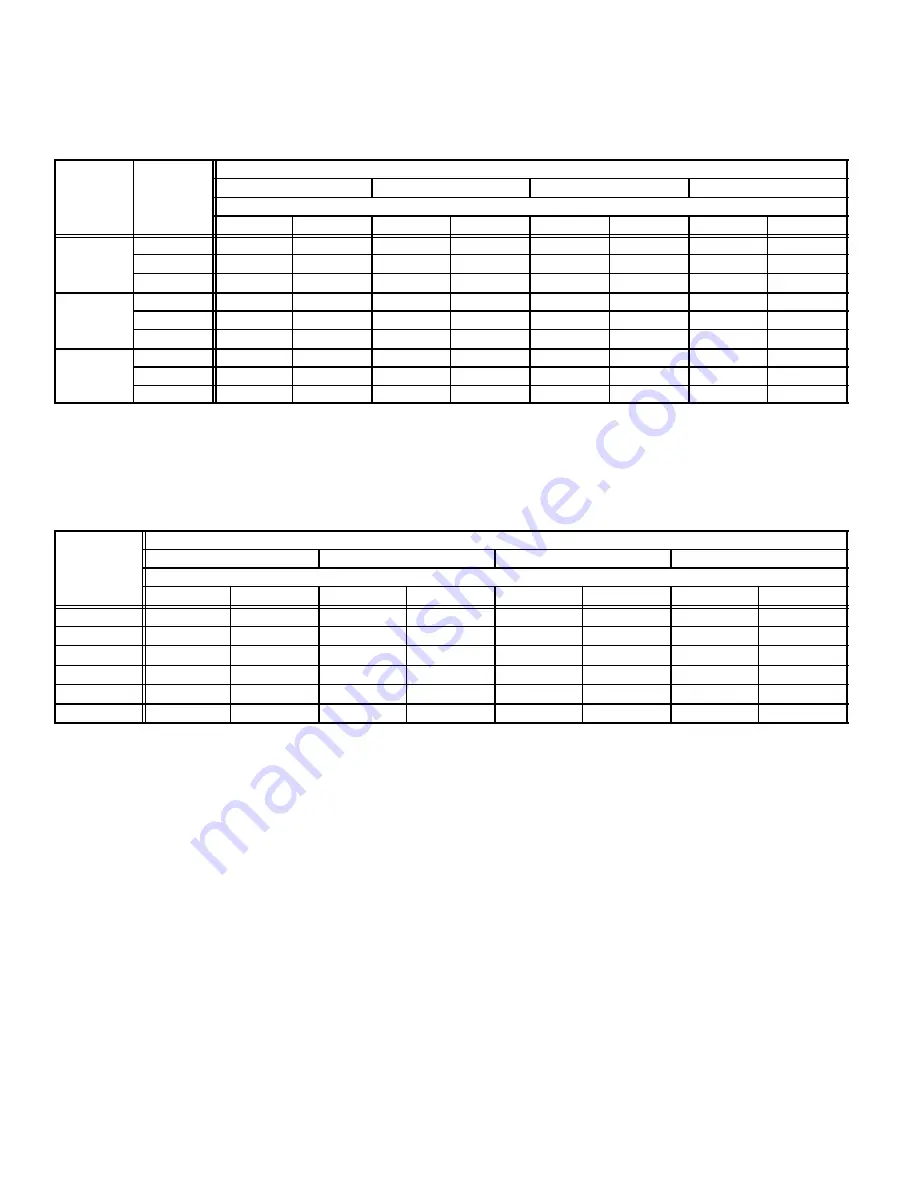
Page 18
TABLE 8
VENT CONNECTOR CAPACITY
TYPE B DOUBLE-WALL VENTS WITH SINGLE-WALL METAL CONNECTORS
SERVING TWO OR MORE CATEGORY I APPLIANCES
Vent
Connector
Vent and Connector Diameter - D (inches)
Vent
Height
Connector
Rise
3 Inch
4 Inch
5 Inch
6 Inch
Height
H
(feet)
Rise
R
(feet)
Appliance Input Rating in Thousands of Btu Per Hour
(feet)
(feet)
MIN
MAX
MIN
MAX
MIN
MAX
MIN
MAX
1
NR
NR
NR
NR
NR
NR
NR
NR
6
2
NR
NR
NR
NR
NR
NR
168
182
6
3
NR
NR
NR
NR
121
131
174
198
1
NR
NR
79
87
116
138
177
214
15
2
NR
NR
83
94
121
150
185
230
5
3
NR
NR
87
100
127
160
193
243
1
47
60
77
110
113
175
169
278
30
2
50
62
81
115
117
185
177
290
30
3
54
64
85
119
122
193
185
300
TABLE 9
COMMON VENT CAPACITY
TYPE B DOUBLE-WALL VENTS WITH SINGLE-WALL METAL CONNECTORS
SERVING TWO OR MORE CATEGORY I APPLIANCES
Vent
Common Vent Diameter - D (inches)
Vent
Height
4 Inch
5 Inch
6 Inch
7 Inch
Height
H
(feet)
Appliance Input Rating in Thousands of Btu Per Hour
(feet)
FAN + FAN
FAN + NAT
FAN + FAN
FAN + NAT
FAN + FAN
FAN + NAT
FAN + FAN
FAN + NAT
6
89
78
136
113
200
158
304
244
8
98
87
151
126
218
173
331
269
10
106
94
163
137
237
189
357
292
15
121
108
189
159
275
221
416
343
20
131
118
208
177
305
247
463
383
30
145
132
236
202
350
286
533
446
Removal of the Furnace from Common Vent
In the event that an existing furnace is removed from a
venting system commonly run with separate gas ap
pliances, the venting system is likely to be too large to
properly vent the remaining attached appliances. The fol
lowing test should be conducted while each appliance in
operation and the other appliances not in operation re
main connected to the common venting system. If the
venting system has been installed improperly, the system
must be corrected as indicated in the general venting re
quirements section.
1 - Seal any unused openings in the common venting
system.
2 - Visually inspect the venting system for proper size and
horizontal pitch. Determine there is no blockage or re
striction, leakage, corrosion, or other deficiencies which
could cause an unsafe condition.
3 - To the extent that it is practical, close all building doors
and windows and all doors between the space in
which the appliances remaining connected to the
common venting system are located and other spaces
of the building. Turn on clothes dryers and any ap
pliances not connected to the common venting sys
tem. Turn on any exhaust fans, such as range hoods
and bathroom exhausts, so they will operate at maxi
mum speed. Do not operate a summer exhaust fan.
Close fireplace dampers.
4 - Follow the lighting instructions. Place the appliance
being inspected in operation. Adjust thermostat so ap
pliance will operate continuously.
5 - Test for spillage of flue gases at the draft hood relief
opening after 5 minutes of main burner operation. Use
the flame of a match or candle, or smoke from a ciga
rette, cigar or pipe.