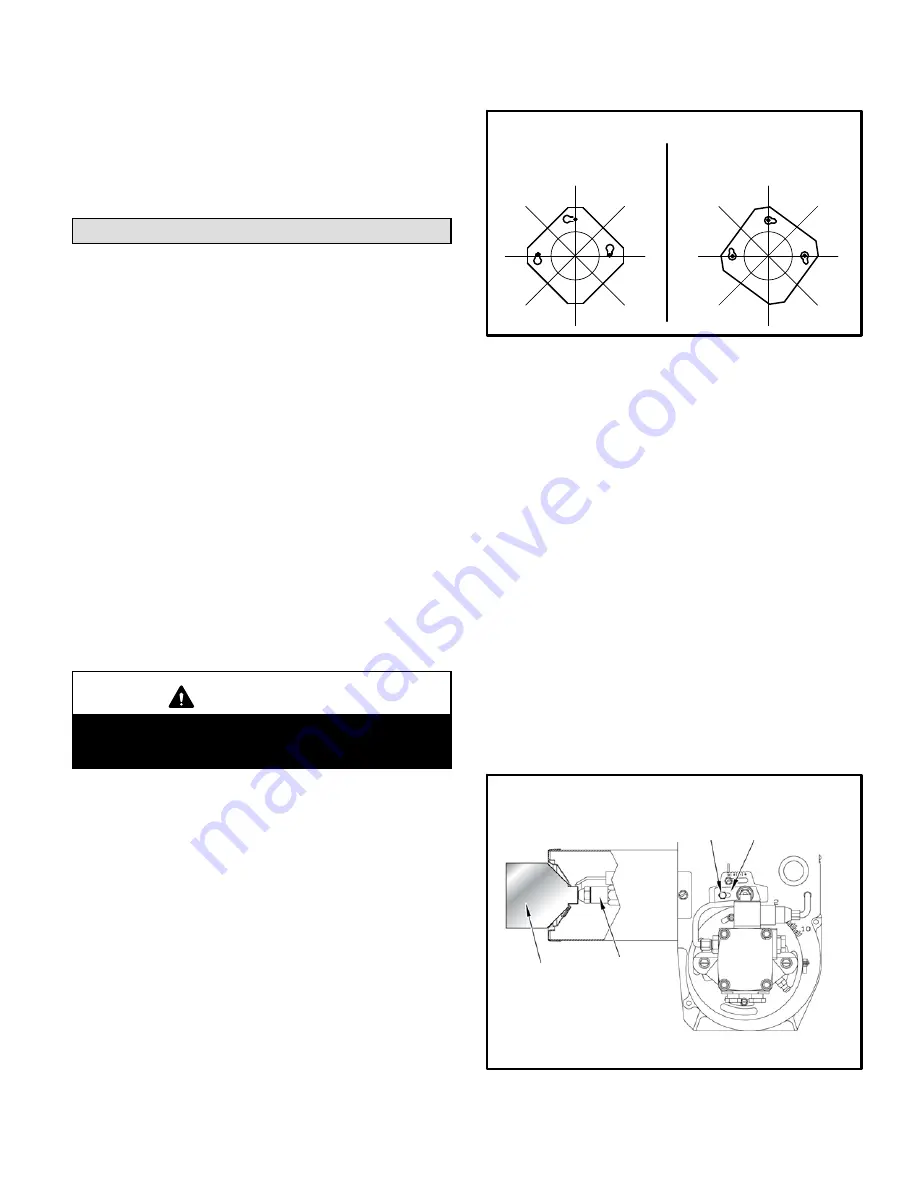
Page 7
2 − Level the unit from side to side and from front to rear. If
the furnace is not level, place fireproof wedges or
shims between the low side of the furnace and the
floor. Make sure the weight of the furnace is distributed
evenly on all four corners. Strain on sides of cabinet
causing cracking and popping noises may occur if
weight of furnace is not evenly distributed.
Adjustments
Neither the nozzle setting nor the air adjustments are facto-
ry set. The furnace is fire−tested and the limit control is
checked to make sure it functions properly; no factory set-
tings are made. During installation, the furnace must be ad-
justed to ensure proper operation. The installing dealer/
contractor must have and use proper test equipment in
order to correctly adjust the oil furnace. Proper testing
equipment is required to ensure correct operation of the
unit. The use of test equipment is more critical than ever
due to tighter tolerances needed to keep the furnace oper-
ating efficiently.
Among the test equipment for an oil furnace, the proper
combustion test kit should contain the following:
D
Draft gauge
D
CO
2
or O
2
analyzer
D
Smoke tester
D
Pressure gauge
D
High temperature thermometer
D
Oil vacuum gauge
D
Beckett T−501 or Z−2000 nozzle gauge
D
Knowledge of proper test equipment operation
CAUTION
Improper nozzle and/or air adjustment of this unit
may result in sooting problems. Refer to the follow-
ing section for correct adjustment procedures.
Nozzle Adjustment
Proper adjustment of the nozzle assembly is critical. Before
the flue pipe and oil lines are installed, the nozzle assembly
must be checked for proper depth and alignment. You must
remove the entire burner assembly (not just the nozzle) from
the furnace to check the nozzle depth and alignment. The
smaller sized firing nozzle has been factory−installed. This
should be verified by the installer. A larger nozzle has been
provided in the bag assembly for use with ELO183UF86, 114
and 150 units. Inspect the spark transformer leads also to en-
sure they are still attached to the electrodes.
The burner assembly is attached to the vestibule panel by
three nuts. Slots are provided in the mounting flange for re-
moving the burner assembly from the vestibule. Loosen the
nuts and turn the whole burner assembly clockwise (figure
6) to remove the entire burner assembly from the furnace.
There is adequate wire to remove the burner without discon-
necting wires. Once removed, turn the burner around in the
vest panel area.
Figure 6
ELO183UF Series Burner Removal
First, loosen three nuts which
attach burner to vest panel.
Next, rotate burner clockwise
on slots then pull toward you.
To correctly check and adjust the nozzle depth and align-
ment, use the Beckett T−501 or Z−2000 gauge.
To check the oil nozzle depth, insert the small end of the
gauge into the end of the cone and measure from the flat of
the end cone to the face of the nozzle. When nozzle depth
is correct, the tip of the nozzle should just touch the end of
the gauge. Refer to the illustration sheet provided with the
gauge. Note that the scale side of the gauge is not used for
this purpose. If necessary, loosen the escutcheon plate se-
curing screw and slide the entire nozzle assembly forward
or backward within the air tube (figure 7). Re−secure es-
cutcheon plate screw when adjustment is completed.
To check nozzle alignment, again insert the small end of
gauge into the end cone and measure the nozzle and
electrode alignment against the center lines marked on
the gauge (again refer to enclosed illustration sheet). If
the nozzle is not centered, but found to be too far left or
right, a new nozzle assembly will need to be ordered. Do
not attempt to adjust by bending the 90 degree elbow in
the oil line.
Take care to properly re−install burner assembly when
nozzle adjustment has been completed.
Figure 7
Beckett Oil Burner Nozzle Adjustment
Burner must be removed from
furnace for this procedure.
1
2
T−501 Gauge
Escutcheon Plate
To Adjust Nozzle
1−Loosen escutcheon plate screw.
2−Slide entire nozzle/electrode assembly back and forth inside air
tube until nozzle just touches gauge.