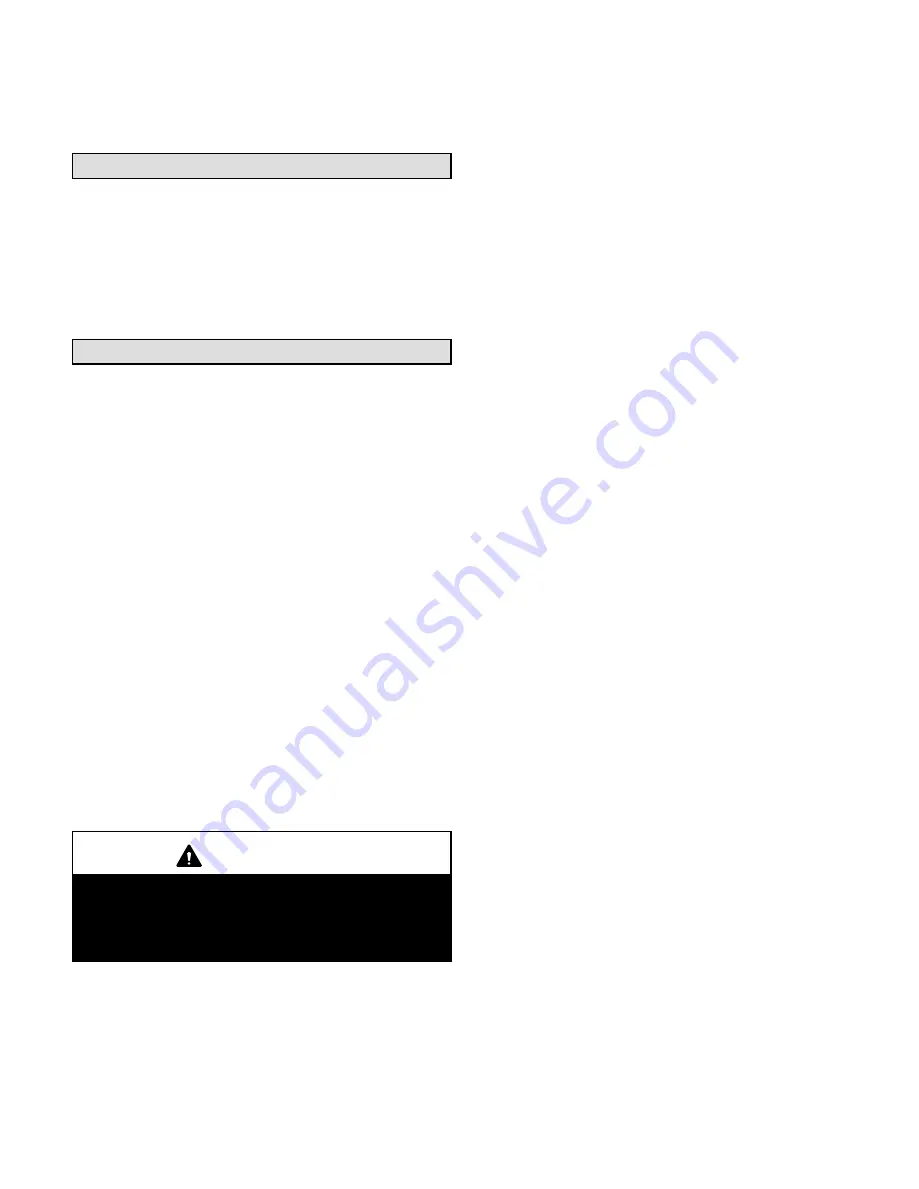
Page 5
trol the flow of air) shall be adequate to prevent chilled air from
entering the furnace and, if manually operated, must be
equipped with means to prevent operation of either unit, un-
less damper is in the full heat" or cool" position.
Notice to Home Owner
This furnace is equipped with safety devices that protect
you and your property. If one or more of these devices is
activated, furnace operation will stop. If your home is left
unattended for an extended period of time, equipment op-
eration must be checked periodically. If this is not possible,
the water supply to the house should be shut off and the
pipes should be drained. This will prevent problems associ-
ated with a NO HEAT condition (frozen pipes, etc.)
Combustion and Ventilation Air
Homes built with energy conservation in mind use tight
construction practices. These houses are sealed so well
that it becomes necessary to provide a means of bringing in
air from outside for combustion. Also, exhaust fans, ap-
pliance vents, chimneys and fireplaces force additional air
that could be used for combustion out of the house. Unless
outside air is brought into the home for combustion, nega-
tive pressure (pressure outside is greater than inside pres-
sure) will build to the point that a down draft can occur in the
furnace vent pipe or chimney. Combustion gases enter the
living space creating a potentially dangerous situation. Ne-
gative pressure may also interfere with proper combustion,
causing sooting within the heat exchanger.
The importance of the previous paragraph cannot be over-
stated. Users may inadvertently block fresh air intakes after
installation.
In the absence of local codes concerning air for combus-
tion and ventilation, the following section outlines guide-
lines and recommends procedures for operating oil fur-
naces in a manner that ensures efficient and safe
operation. Special consideration must be given to combus-
tion air needs as well as requirements for exhaust vents
and oil piping.
Combustion Air Requirements
CAUTION
Insufficient combustion air can cause headaches,
nausea, dizziness or asphyxiation. It will also cause
excess water in the heat exchanger resulting in rust-
ing and premature heat exchanger failure. It can also
cause property damage.
All oil-fired appliances require air to be used for the com-
bustion process. If sufficient amounts of combustion air are
not available, the furnace or other appliance will operate in
an inefficient and unsafe manner. Enough air must be pro-
vided to meet the needs of all fuel-burning appliances, as
well as appliances such as exhaust fans which force air out
of the home. When fireplaces, exhaust fans, or clothes dry-
ers are used at the same time as the furnace, much more
air is required to ensure proper combustion and to prevent
a down-draft situation. Insufficient amounts of air also
cause incomplete combustion which can result in sooting.
Requirements for providing air for combustion and ventila-
tion depend largely on whether the furnace is installed in an
unconfined or confined space.
Unconfined Space
An unconfined space is an area such as a basement or
large equipment room with a volume greater than 50 cubic
feet (1.4 cubic meters) per 1,000 Btu (293 W) per hour of
the combined input rating of all appliances installed in that
space. This space also includes adjacent rooms which are
not separated by a door. Though an area may appear to be
unconfined, it might be necessary to bring in outdoor air for
combustion if the structure does not provide enough air by
infiltration. If the furnace is located in a building of tight
construction with weather stripping and caulking around
the windows and doors, follow the procedures outlined for
using air from the outside for combustion and ventilation.
Confined Space
A confined space is an area with volume less than 50 cubic
feet (1.4 cubic meters) per 1,000 Btu (293 W) per hour of
the combined input rating of all appliances installed in that
space. This definition includes furnace closets or small
equipment rooms.
When the furnace is installed so that supply ducts carry air
circulated by the furnace to areas outside the space con-
taining the furnace, the return air must be handled by ducts
which are sealed to the furnace casing and which terminate
outside the space containing the furnace. This is especially
important when the furnace is mounted on a platform in a
confined space such as a closet or small equipment room.
Even a small leak around the base of the unit at the platform
or at the return air duct connection can cause a potentially
dangerous negative pressure condition. Air for combustion
and ventilation can be brought into the confined space ei-
ther from inside the building or from outside.
Air from an Adjacent Space
If the confined space housing the furnace adjoins space
categorized as unconfined, air can be brought in by provid-
ing two permanent openings between the two spaces.
Each opening must have a minimum free area of 1 square
inch
(6.4 square centimeters) per 1,000 Btu (293 W) per
hour of the total input rating of all fuel-fired equipment in the
confined space. Each opening must be at least 100 square
inches (614.5 square centimeters). One opening shall be
within 12" (305 mm) of the top of the enclosure and one
opening within 12" (305 mm) of the bottom (See figure 3).