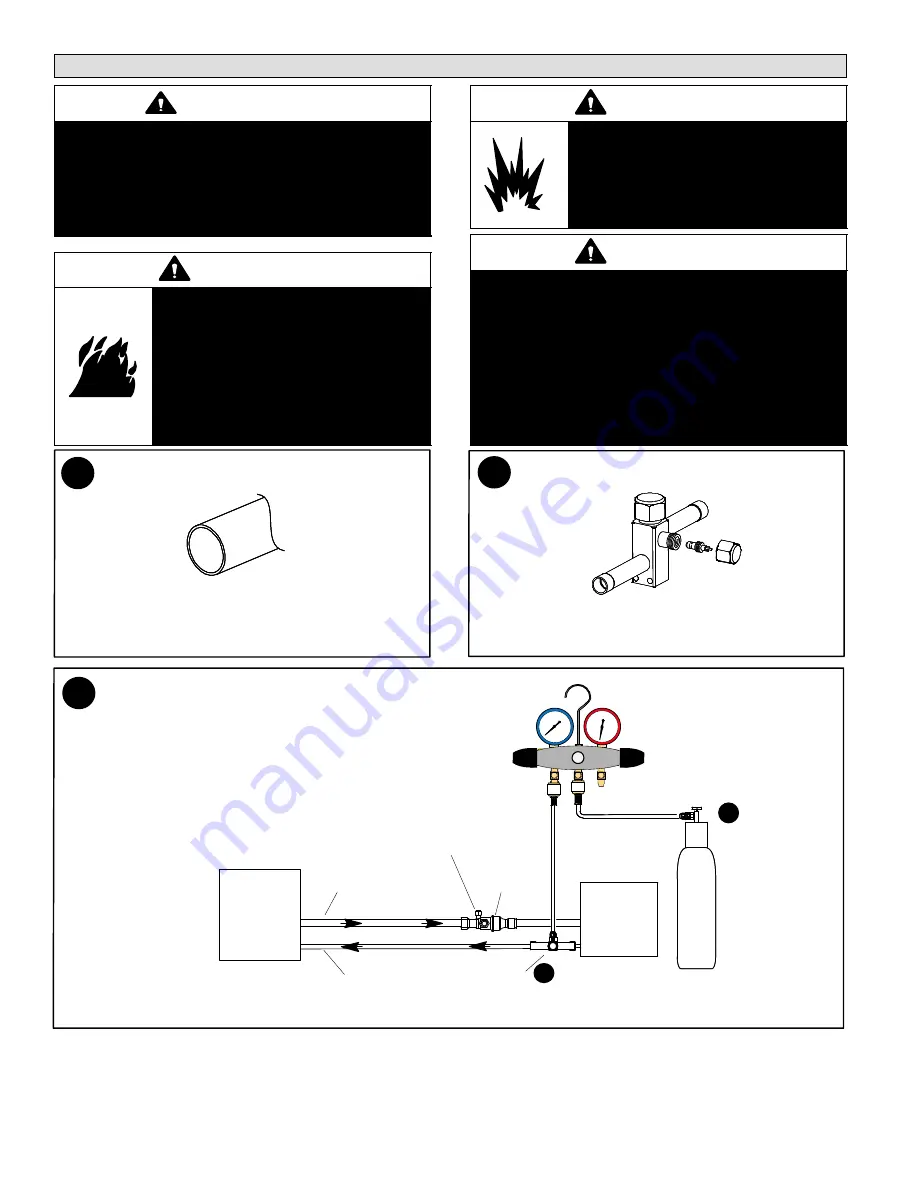
Page 10
506120−01 03/10
Brazing Connections
WARNING
Polyol ester (POE) oils used with HFC−410A
refrigerant absorb moisture very quickly. It is very
important that the refrigerant system be kept
closed as much as possible. DO NOT remove line
set caps or service valve stub caps until you are
ready to make connections.
WARNING
Danger of fire. Bleeding the
refrigerant charge from only the high
side may result in the low side shell
and suction tubing being
pressurized. Application of a brazing
torch while pressurized may result in
ignition of the refrigerant and oil
mixture − check the high and low
pressures before unbrazing.
WARNING
When using a high pressure gas such
as dry nitrogen to pressurize a
refrigeration or air conditioning
system, use a regulator that can
control the pressure down to 1 or 2
psig (6.9 to 13.8 kPa).
CAUTION
Brazing alloys and flux contain materials which are
hazardous to your health.
Avoid breathing vapors or fumes from brazing
operations. Perform operations only in well
ventilated areas.
Wear gloves and protective goggles or face shield
to protect against burns.
Wash hands with soap and water after handling
brazing alloys and flux.
1
2
CUT AND DEBUR
CAP AND CORE REMOVAL
Cut ends of the refrigerant lines square (free from nicks or
dents). Debur the ends. The pipe must remain round, do not
pinch end of the line.
Remove service cap and core from both the suction and liquid
line service ports.
3
ATTACHED GAUGES
OUTDOOR
UNIT
LIQUID LINE
SUCTION LINE
LIQUID LINE
SERVICE
VALVE
SUCTION LINE
SERVICE
VALVE
ATTACH
GAUGES
INDOOR UNIT
SERVICE PORT MUST BE
OPEN TO ALLOW EXIT
POINT FOR NITROGEN
A
Connect gauge set low pressure side to liquid line service valve.
B
Connect gauge set center port to bottle of nitrogen.
NITROGEN
A
B