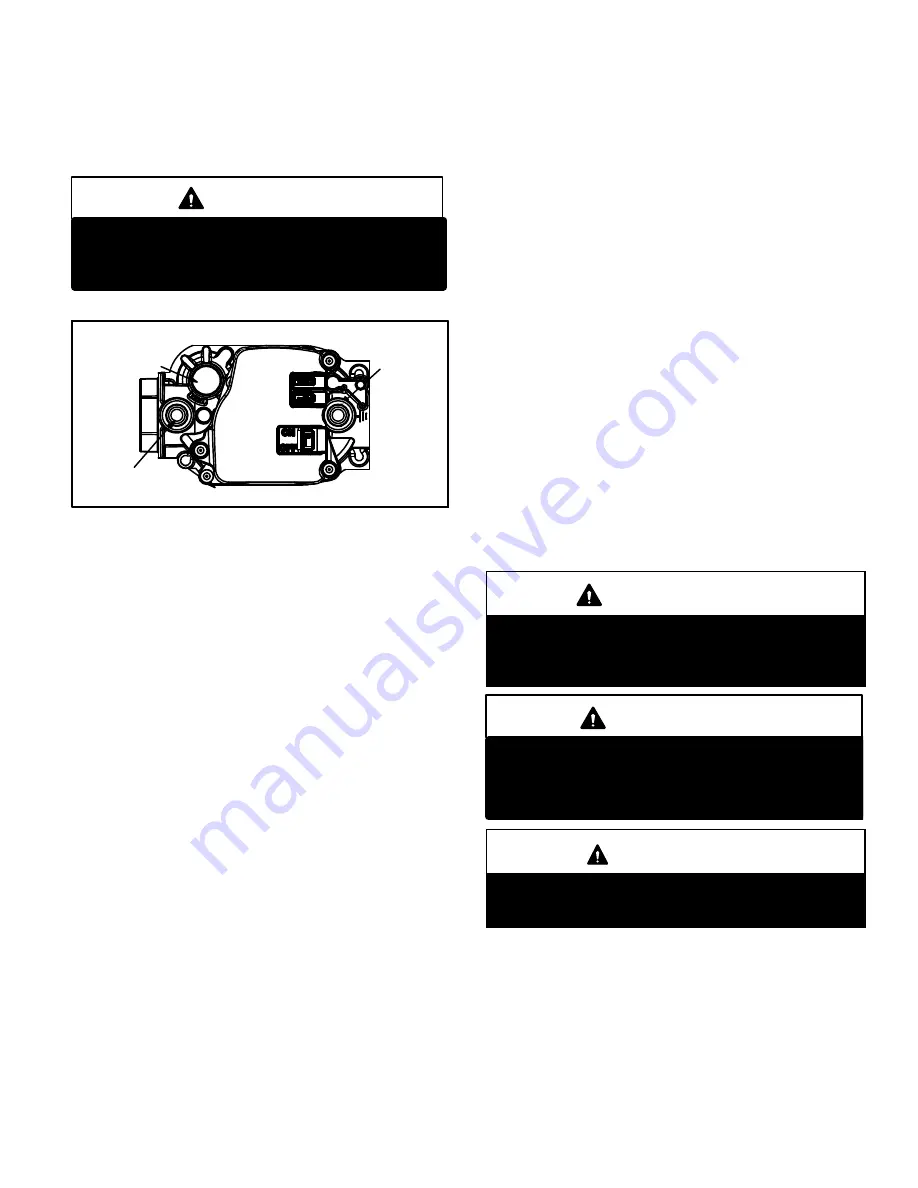
Page 17
II- PLACEMENT AND INSTALLATION
Make sure unit is installed in accordance with installation
instructions and applicable codes.
III- START‐UP
A- Heating Start‐Up
WARNING
Shock and burn hazard.
EL180DFE units are equipped with a hot surface
ignition system. Do not attempt to light manually.
Gas Valve Operation
FIGURE 18
GAS VALVE SHOWN IN ON POSITION
MANIFOLD
PRESSURE
OUTLET
PORT
INLET
PRESSURE
PORT
MANIFOLD
PRESSURE
ADJUSTMENT
SCREW
1 -
STOP
! Read the safety information at the beginning of
this section.
2 - Set the thermostat to the lowest setting.
3 - Turn off all electrical power to the unit.
4 - This furnace is equipped with an ignition device which
automatically lights the burners. Do
not
try to light the
burners by hand.
5 - Remove the heating compartment access panel.
6 - Move gas valve switch to
OFF position
. Do not
force. See figure 18.
7 - Wait five minutes to clear out any gas. If you then smell
gas, STOP! Immediately call your gas supplier from a
neighbor's phone. Follow the gas supplier's instruc
tions. If you do not smell gas go to next step.
8 - Move gas valve switch to
ON position
. Do not force.
See figure 18.
9 - Replace the heating compartment access panel.
10- Turn on all electrical power to to the unit.
11- Set the thermostat to desired setting.
NOTE - When unit is initially started, steps 1 through 11
may need to be repeated to purge air from gas line.
12- If the appliance will not operate, follow the instructions
“Turning Off Gas to Unit” and call the gas supplier.
Turning Off Gas to Unit
1 - Set the thermostat to the lowest setting.
2 - Turn off all electrical power to the unit if service is to be
performed.
3 - Remove the heating compartment access panel.
4 - Move gas valve switch to
OFF position
. Do not
force. See figure 18.
5 - Replace the heating compartment access panel.
B- Safety or Emergency Shutdown
Disconnect main power to unit. Close manual and main gas
valves.
C- Extended Period Shutdown
Turn off thermostat or set to “UNOCCUPIED” mode. Close
all gas valves (both internal and external to unit) to guaran
tee no gas leaks into combustion chamber. Turn off power
to unit. All access panels and covers must be in place and
secured.
IV-HEATING SYSTEM SERVICE CHECKS
A- C.S.A. Certification
All units are C.S.A. design certified without modifications.
Refer to the EL180DFE Installation Instruction.
B- Gas Piping
Gas supply piping should not allow more than 0.5”W.C. drop
in pressure between gas meter and unit. Supply gas pipe
must not be smaller than unit gas connection.
Compounds used on gas piping threaded joints should be
resistant to action of liquefied petroleum gases.
C- Testing Gas Piping
CAUTION
If a flexible gas connector is required or allowed by
the authority that has jurisdiction, black iron pipe
shall be installed at the gas valve and extend outside
the furnace cabinet.
IMPORTANT
In case emergency shutdown is required, turn off
the main shut‐off valve and disconnect the main
power to unit. These controls should be properly
labeled by the installer.
WARNING
Do not over torque (800 in-lbs) or under torque (350
in-lbs) when attaching the gas piping to the gas
valve.
When pressure testing gas lines, the gas valve must be dis
connected and isolated. Gas valves can be damaged if
subjected to more than 0.5 psig (14” W.C.). See figure 19
.
If
the pressure is equal to or greater than 0.5 psig (14”W.C.),
close the manual shut-off valve before pressure testing to
isolate furnace from gas supply.