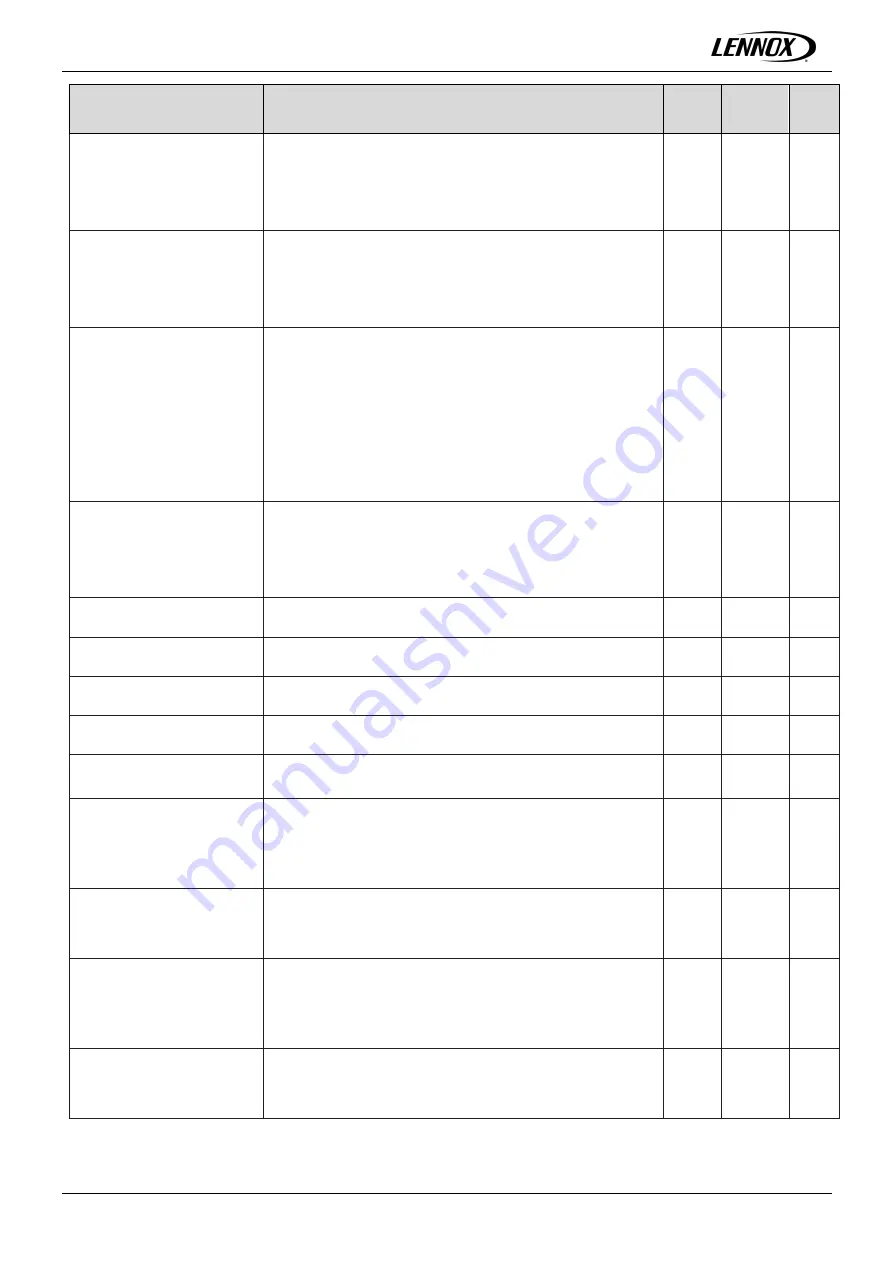
MAINTENANCE PLAN
e-BALTIC-IOM-2020.12-EN
84
Task
Operating mode
Monthly
+
Quarterly
+ Half
Yearly
Clean or replace filters:
Disposable, or metal frame.
Replace filters with new ones if disposable. Vacuum clean or
blow the dirt. Wash and dry carefully. Replace filter if necessary
by an original Lennox filter.
Blocked filter will reduce the performance of the unit.
THE UNIT SHOULD NEVER BE OPERATED WITHOUT FILTERS
•
Visual check of the oil level
(applicable for units equipped
with sight glass) and check
the oil for acidity on the
refrigerant circuits
Visually check the oil level through the sight glass on the side of
the compressor casing
Test the oil every 3 years and after each intervention on the
refrigerant circuit
•
Clean condensate drains,
indoor coils and outdoor coils
(following local regulations)
It's mandatory to clean the external coils, according to the
environment where the unit is located, the frequency of the
cleaning varies from once in a month to minimum twice in a
year
.
The performance and the sustainability of the machine is based
on the perfect heat exchange.
The use of a neutral pH cleaning product is mandatory.
(WARNING: Fins and copper tubes are very fragile! Any damage
WILL reduce the performances of the unit).
|
|
|
Check condenser fans
Check the rotation of the fan ( free rotation, detection of
vibrations or bearing noises)
Check for the Amps consumed on all three phases; compare it
with the nominal value given in the electrical wiring diagram.
Check the status of the fan blades and its protections.
|
Check for the Amps
consumed
Check for the Amps consumed on all three phases; compare
with the nominal value given in the electrical wiring diagram.
|
Check Smoke detector
Start the unit. Trigger the smoke detector with an aerosol
tester. Reset unit and control.
|
Check CLIMATIC™ control,
set-points and variables
Refer to the commissioning sheet; Check all set points are set
according to this document.
|
Check refrigeration system
for proper functioning
Retrieve/Check the values of Overheating and subcooling
|
Check clock settings
Check the time and date of the control
•
Check the position and
tightness
of refrigeration components
Check systematically all connections and fixings on the
refrigeration circuit. Check for oil traces, eventually a leak test
should be conducted. Check operating pressures correspond to
the ones, indicated on the commissioning sheet
|
Check three-way valve on
HWC (If applicable)
Increase room set-point 10°C above the actual room
temperature. Check operation of the piston. It must move away
from the valve head. Reset the control.
|
Check the position of the
crankcase heaters (around
the compressor) and the
proper functioning of it
Check the well fixation of the crankcase heaters, if it is tight
enough
And check the crankcase heaters overall working.
•
Check defrost cycle with 4-
way valve inversion.
Switch the unit to heat pump mode. Change the set point to
obtain the standard defrost mode and reduce the cycle time to
the min value. Check the operation of the defrost cycle.
|