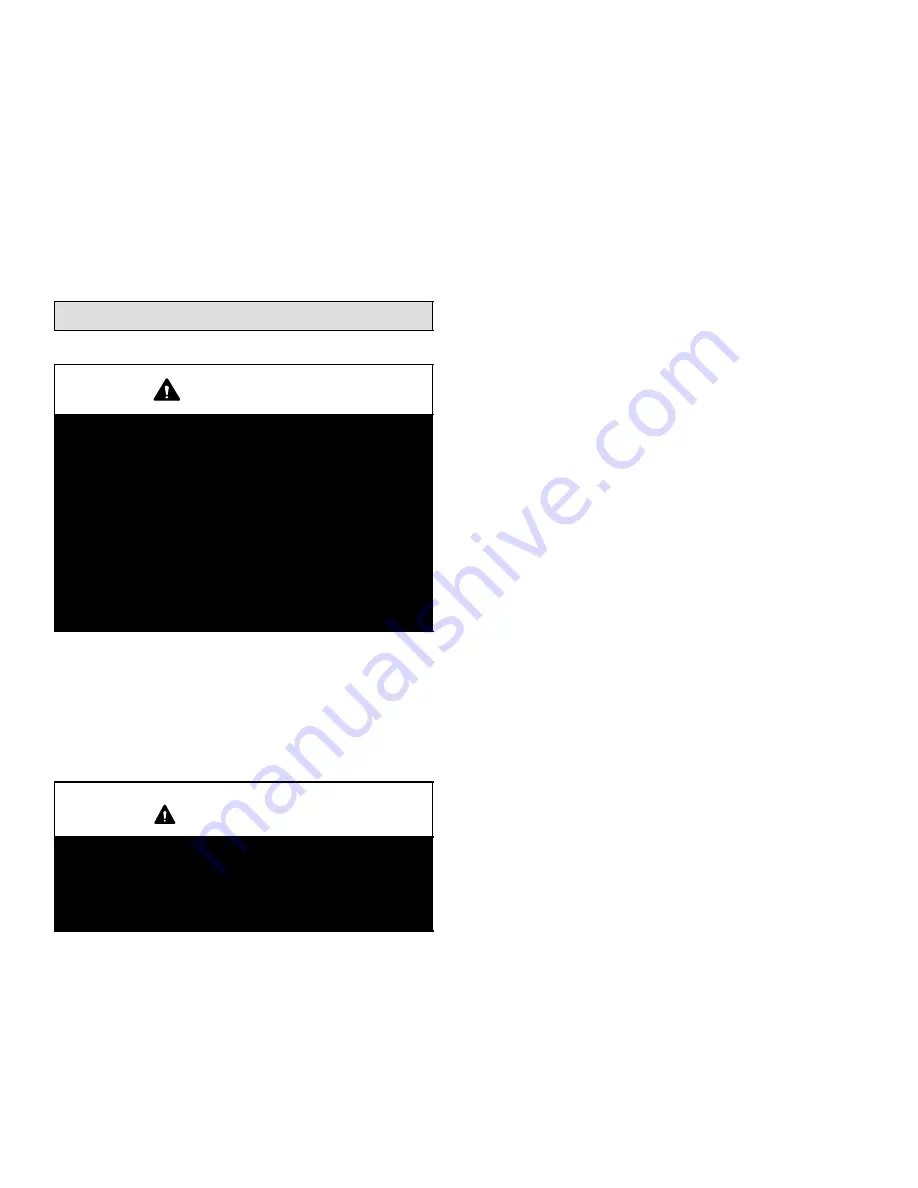
Page 54
6 − If the heating demand continues beyond the third−
stage on delay, the integrated control energizes the in-
ducer at high speed. The indoor blower motor is ad-
justed to a speed which is appropriate for the target
rate.
7 −When the thermostat heating demand is satisfied, the
gas valve is de−energized and the combustion air in-
ducer begins a 20−second post−purge. The field−se-
lected indoor blower off delay begins.
8 − When the combustion air post−purge period is com-
plete, the inducer is de−energized. The indoor blower
is de−energized at the end of the off delay.
Service
WARNING
ELECTRICAL SHOCK, FIRE,
OR EXPLOSION HAZARD.
Failure to follow safety warnings exactly could result
in dangerous operation, serious injury, death or
property damage.
Improper servicing could result in dangerous opera-
tion, serious injury, death, or property damage.
Before servicing, disconnect all electrical power to
furnace.
When servicing controls, label all wires prior to dis-
connecting. Take care to reconnect wires correctly.
Verify proper operation after servicing.
At the beginning of each heating season, system should be
checked as follows by a qualified service technician:
Blower
Check the blower wheel for debris and clean if necessary.
The blower motors are prelubricated for extended bearing
life. No further lubrication is needed.
WARNING
The blower access panel must be securely in place
when the blower and burners are operating. Gas
fumes, which could contain carbon monoxide, can
be drawn into living space resulting in personal inju-
ry or death.
Filters
All SLP98UHV filters are installed external to the unit. Fil-
ters should be inspected monthly. Clean or replace the fil-
ters when necessary to ensure proper furnace operation.
Table 1 lists recommended filter sizes.
Exhaust and air intake pipes
Check the exhaust and air intake pipes and all connections
for tightness and to make sure there is no blockage.
NOTE − After any heavy snow, ice or frozen fog event, the
furnace vent pipes may become restricted. Always check
the vent system and remove any snow or ice that may be
obstructing the plastic intake or exhaust pipes.
Electrical
1 − Check all wiring for loose connections.
2 − Check for the correct voltage at the furnace (furnace
operating).Correct voltage is 10%.
3 − Check amp−draw on the blower motor with inner blow-
er panel in place.
Motor Nameplate__________Actual__________
Winterizing and Condensate Trap Care
1 − Turn off power to the unit.
2 − Have a shallow pan ready to empty condensate water.
3 − Remove the drain plug from the condensate trap and
empty water. Inspect the trap then reinstall the drain
plug and refill trap with water.
Cleaning the Burner Assembly
1 − Turn off electrical and gas power supplies to furnace.
Remove upper and lower furnace access panels.
2 − Disconnect the 2−pin plug from the gas valve.
3 − Remove the burner box cover.
4 − Disconnect the gas supply line from the gas valve. Re-
move gas valve/manifold assembly.
5 − Mark and disconnect sensor wire from the sensor. Dis-
connect wires from flame rollout switches.
6 − Remove four screws which secure burner box assem-
bly to vest panel. Remove burner box from the unit.
7 − Use the soft brush attachment on a vacuum cleaner to
gently clean the face of the burners. Visually inspect
the inside of the burners and crossovers for any block-
age caused by foreign matter. Remove any blockage.
8 − Reinstall the burner box assembly using the existing
four screws. Make sure that the burners line up in the
center of the burner ports.
9 − Reconnect the sensor wire and reconnect the 2−pin
plug to the ignitor wiring harness. Reconnect wires to
flame rollout switches.
10 − Reinstall the gas valve manifold assembly. Reconnect
the gas supply line to the gas valve. Reinstall the burn-
er box cover.
11 − Reconnect 2−pin plug to gas valve.
12 − Replace the blower compartment access panel.
13 − Refer to instruction on verifying gas and electrical con-
nections when re−establishing supplies.
14 − Follow lighting instructions to light and operate fur-
nace for 5 minutes to ensure that heat exchanger is
clean and dry and that furnace is operating properly.
15 − Replace heating compartment access panel.