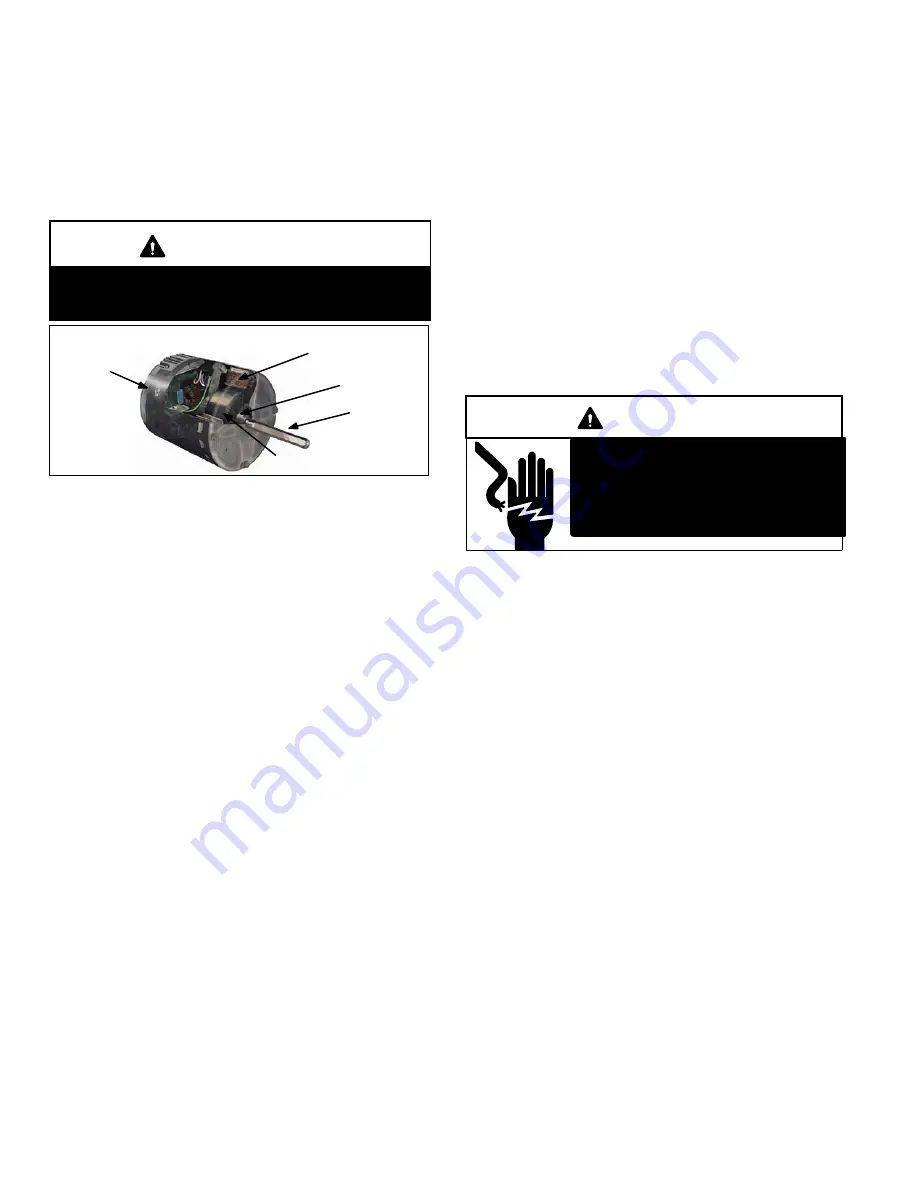
Page 62
CBX32MV
primarily an AC to DC converter. Converted DC power is
used to drive the motor. The controller contains a
microprocessor which monitors varying conditions
inside the motor (such as motor workload). Because this
motor has a permanent magnet rotor it does not need
brushes like conventional DC motors.
Internal components are shown in figure 29. The stator
windings are split into three poles which are electrically
connected to the controller. This arrangement allows motor
windings to turn on and off in sequence by the controller.
IMPORTANT
Earlier ECM motors used on other Lennox air handler
models are not interchangeable with motors used on the
CBX32MV line.
STATOR
(WINDINGS)
OUTPUT
SHAFT
BEARING
ROTOR
CONTROLLER
Figure 29. Blower Motor Components
The controller uses sensing devices to sense what position
the rotor is in at any given time. By sensing the position of the
rotor and then switching the motor windings on and off in
sequence, the rotor shaft turns the blower.
All CBX32MV blower motors use single phase power. An
external run capacitor is not used. The motor uses
permanently lubricated ball‐type bearings.
Internal Operation
The motor is controlled via serial communication between
the integrated control and the controller permanently
attached to the motor shell. The messages sent back and
forth between the two controls serve to communicate
rotational direction, demand, motor size, current draw,
torque, and RPM, among other variables.
Motor RPM is continually adjusted internally to maintain
constant static pressure against the blower wheel. The
controller monitors the static work load on the motor and motor
amp‐draw to determine the amount of RPM adjustment.
Blower RPM may be adjusted any amount in order to maintain
a constant cfm as shown in Blower Ratings Tables. The cfm
remains relatively stable over a broad range of static pressure.
Since the blower constantly adjusts RPM to maintain a
specified cfm, motor RPM is not rated. Hence, the terms “cool
speed”, “heat speed ” or “speed tap” in this manual, on the unit
wiring diagram and on blower B3, refer to blower cfm
regardless of motor RPM.
Initial Power Up
When line voltage is applied to B3, there will be a large inrush
of power lasting less than 1/4 second. This inrush charges a
bank of DC filter capacitors inside the controller. If the
disconnect switch is bounced when the disconnect is closed,
the disconnect contacts may become welded. Try not to
bounce the disconnect switch when applying power to the unit.
Motor Start‐Up
When B3 begins start‐up, the motor gently vibrates back and
forth for a moment. This is normal. During this time the
electronic controller is determining the exact position of the
rotor. Once the motor begins turning, the controller slowly
eases the motor up to speed (this is called “soft‐start”). The
motor may take as long as 60 seconds to reach full speed. If
the motor does not reach 200RPM within 13 seconds, the
motor shuts down. Then the motor will immediately attempt a
restart. The shutdown feature provides protection in case of a
frozen bearing or blocked blower wheel. The motor may
attempt to start eight times. If the motor does not start after the
eighth try, the controller locks out. Reset controller by
momentarily turning off power to unit.
The DC filter capacitors inside the controller are connected
electrically to the motor supply wires. The capacitors take
approximately 5 minutes to discharge when the disconnect
is opened. For this reason it is necessary to wait at least 5
minutes after turning off power to the unit before
attempting to service motor.
DANGER
Disconnect power from unit and wait
at least five minutes to allow capaci
tors to discharge before attempting to
service motor. Failure to wait may
cause personal injury or death.
INDOOR BLOWER MOTOR (B3) CONTROL
TROUBLESHOOTING (REGAL-BELOIT)
NOTE -
If the communication channel is disrupted (loss of
communication and of 24VAC) to the air handler control,
the motor will continue to operate at its current mode. This
means, if the motor is currently in idle, it will stay in idle
mode; if it is currently running, it will stay running at the
current operating point.
To verify motor operation see steps below and figure 30.
CHECK POWER TO MOTOR
1.
Remove J48 (5-pin power plug) from P48 on the motor.
2.
With the power on at the air handler, use a test meter to
verify 240V between pins 4 and 5 on J48.
3.
Reconnect J48 to P48 on the motor.
APPLY TEST SIGNAL FOR MOTOR OPERATION
1.
Remove J49 (4-pin low voltage connector) from P49 on
the motor.
2.
Using test jumpers, apply 24V to pins 3 and 4 on P49 on
the motor.
Note: Do not apply 24V to pins 2 and 4 on P49. Doing so
will cause permanent damage to the motor.
3.
Motor should run at 75%.
4.
Test is complete. Remove jumpers and reconnect
plugs.
Another option is to use the TECMate PRO with the 16 to
4 pin adaptor. The use of the TECMate PRO isolates the
motor from the integrated control. Follow the instructions
provided with the kit. If the motor runs do not replace.