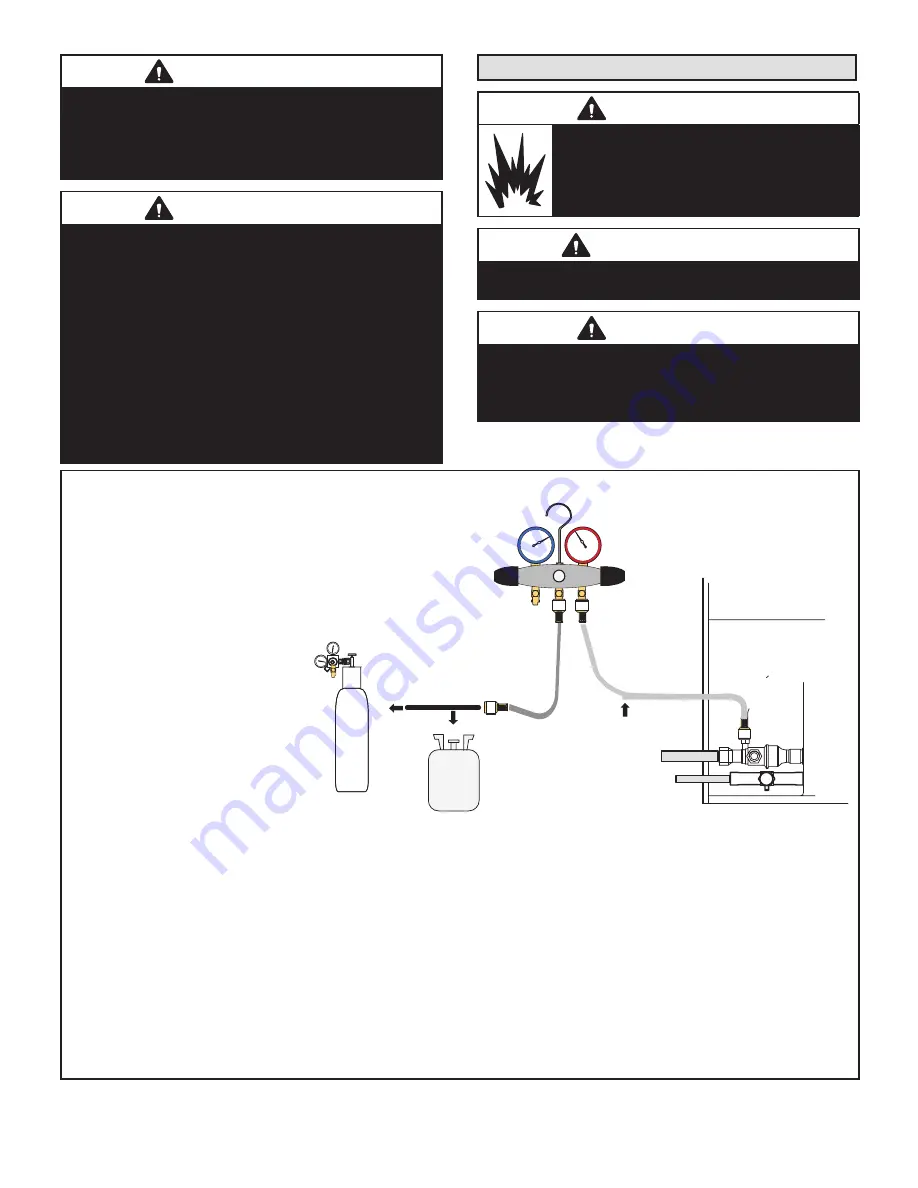
Page 16
IMPORTANT
The Clean Air Act of 1990 bans the intentional venting
of refrigerant (CFC’s and HCFC’s) as of July 1, 1992.
Approved methods of recovery, recycling or reclaiming
must be followed. Fines and/or incarceration may be
levied for non-compliance.
IMPORTANT
If this unit is being matched with an approved line set
or indoor unit coil that was previously charged with
mineral oil, or if it is being matched with a coil which
was manufactured before January of 1999, the coil and
line set must be flushed prior to installation. Take care to
empty all existing traps. Polyol ester (POE) oils are used
in Lennox units charged with HFC-410A refrigerant.
Residual mineral oil can act as an insulator, preventing
proper heat transfer. It can also clog the expansion
device and reduce system performance and capacity.
Failure to properly flush the system, per this instruction
and the detailed Installation and Service Procedures
manual will void the warranty.
Leak Test Line Set and Indoor Coil
WARNING
When using a high pressure gas such as
nitrogen to pressurize a refrigeration or air
conditioning system, use a regulator that can
control the pressure down to 1 or 2 psig (6.9
to 13.8 kPa).
IMPORTANT
Leak detector must be capable of sensing HFC
refrigerant.
WARNING
Refrigerant can be harmful if it is inhaled. Refrigerant
must be used and recovered responsibly.
Failure to follow this warning may result in personal
injury or death.
TO VAPOR
SERVICE VALVE
HFC-410A
MANIFOLD GAUGE SET
OUTDOOR UNIT
HIGH
LOW
NITROGEN
A
With both manifold valves closed, connect the cylinder of HFC-410A refrigerant to the center port of the manifold gauge set. Open the valve
on the HFC-410A cylinder (vapor only).
B
Open the high pressure side of the manifold to allow HFC-410A into the line set and indoor unit. Weigh in a trace amount of HFC-410A.
[A
trace amount is a maximum of two ounces (57 g) refrigerant or three pounds (31 kPa) pressure].
Close the valve on the HFC-410A cylinder
and the valve on the high pressure side of the manifold gauge set. Disconnect the HFC-410A cylinder.
C
Connect a cylinder of dry nitrogen with a pressure regulating valve to the center port of the manifold gauge set.
D
Adjust dry nitrogen pressure to 150 psig (1034 kPa). Open the valve on the high side of the manifold gauge set in order to pressurize the line set
and the indoor unit.
E
After a few minutes, open one of the service valve ports and verify that the refrigerant added to the system earlier is measurable with a leak
detector
.
F
After leak testing disconnect gauges from service ports.
After the line set has been connected to the indoor and outdoor units, check the line set connections and indoor unit for leaks. Use the
following procedure to test for leaks:
A
Connect an HFC-410A manifold gauge set high pressure
hose to the vapor valve service port.
NOTE
— Normally, the high pressure hose is connected to
the liquid line port. However, connecting it to the vapor port
better protects the manifold gauge set from high pressure
damage.
B
With both manifold valves closed, connect the cylinder of
HFC-410A refrigerant to the center port of the manifold gauge
set.
NOTE — Later in the procedure,
the HFC-410A container will be
replaced by the nitrogen
container.
1
CONNECT GAUGE SET
2
TEST FOR LEAKS
A
B
FIGURE 10. Leak Test