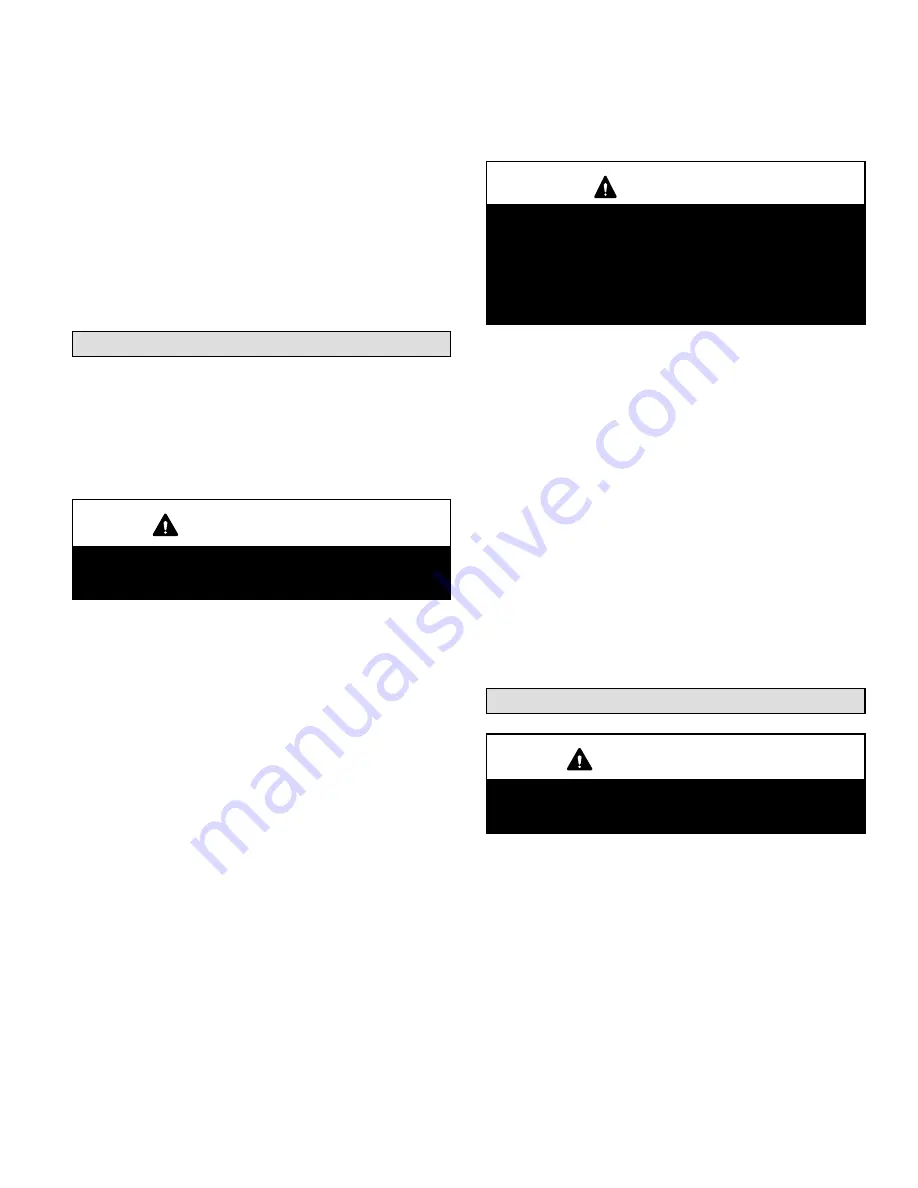
Page 13
5 − Connect the manifold gauge set high pressure hose to
the vapor valve service port.
(Normally, the high pres-
sure hose is connected to the liquid line port; however,
connecting it to the vapor port better protects the man-
ifold gauge set from high pressure damage.)
6 − Adjust the nitrogen pressure to 150 psig (1034 kPa).
Open the valve on the high side of the manifold gauge
set which will pressurize line set and indoor unit.
7 − After a few minutes, open a refrigerant port to ensure
the refrigerant you added is adequate to be detected.
(Amounts of refrigerant will vary with line lengths.)
Check all joints for leaks. Purge nitrogen and HCFC-22
mixture. Correct any leaks and recheck.
Evacuation
Evacuating the system of noncondensables is critical for
proper operation of the unit. Noncondensables are defined
as any gas that will not condense under temperatures and
pressures present during operation of an air conditioning
system. Noncondensables and water vapor combine with
refrigerant to produce substances that corrode copper pip-
ing and compressor parts.
IMPORTANT
Use a thermocouple or thermistor electronic vacuum
gauge that is calibrated in microns. Use an instrument
that reads from 50 microns to at least 10,000 microns.
1 − Connect the manifold gauge set to the service valve
ports as follows:
low pressure gauge to
vapor
line service valve
high pressure gauge to
liquid
line service valve
2 − Connect micron gauge.
3 − Connect the vacuum pump (with vacuum gauge) to the
center port of the manifold gauge set.
4 − Open both manifold valves and start the vacuum
pump.
5 − Evacuate the line set and indoor unit to an
absolute
pressure
of 23,000 microns (29.01 inches of mercu-
ry). During the early stages of evacuation, it is desir-
able to close the manifold gauge valve at least once to
determine if there is a rapid rise in
absolute pressure
.
A rapid rise in pressure indicates a relatively large leak.
If this occurs, repeat the leak testing procedure.
NOTE − The term
absolute pressure
means the total
actual pressure within a given volume or system,
above the absolute zero of pressure. Absolute pres-
sure in a vacuum is equal to atmospheric pressure mi-
nus vacuum pressure.
6 − When the absolute pressure reaches 23,000 microns
(29.01 inches of mercury), close the manifold gauge
valves, turn off the vacuum pump and disconnect the
manifold gauge center port hose from vacuum pump.
Attach the manifold center port hose to a nitrogen cylin-
der with pressure regulator set to 150 psig (1034 kPa)
and purge the hose. Open the manifold gauge valves
to break the vacuum in the line set and indoor unit.
Close the manifold gauge valves.
CAUTION
Danger of Equipment Damage.
Avoid deep vacuum operation. Do not use compres-
sors to evacuate a system.
Extremely low vacuums can cause internal arcing
and compressor failure.
Damage caused by deep vacuum operation will void
warranty.
7 − Shut off the nitrogen cylinder and remove the manifold
gauge hose from the cylinder. Open the manifold
gauge valves to release the nitrogen from the line set
and indoor unit.
8 − Reconnect the manifold gauge to the vacuum pump,
turn the pump on, and continue to evacuate the line set
and indoor unit until the absolute pressure does not
rise above 500 microns (29.9 inches of mercury) within
a 20−minute period after shutting off the vacuum pump
and closing the manifold gauge valves.
9 − When the absolute pressure requirement above has
been met, disconnect the manifold hose from the vacu-
um pump and connect it to an upright cylinder of
HCFC-22 refrigerant. Open the manifold gauge valves
to break the vacuum from 1 to 2 psig positive pressure in
the line set and indoor unit. Close manifold gauge
valves and shut off the HCFC-22 cylinder and remove
the manifold gauge set.
Start−Up
IMPORTANT
If unit is equipped with crankcase heater, it should be
energized 24 hours before unit start−up to prevent
compressor damage as a result of slugging.
1 − Rotate fan to check for frozen bearings or binding.
2 − Inspect all factory and field-installed wiring for loose
connections.
3 − After evacuation is complete, open the liquid line and
vapor line service valves (counterclockwise) to release
refrigerant charge (contained in outdoor unit) into the
system.
4 − Replace stem caps and secure finger tight, then tight-
en an additional (1/6) one-sixth of a turn.
5 − Check voltage supply at the disconnect switch. The
voltage must be within the range listed on the unit
nameplate. If not, do not start the equipment until the
power company has been consulted and the voltage
condition has been corrected.