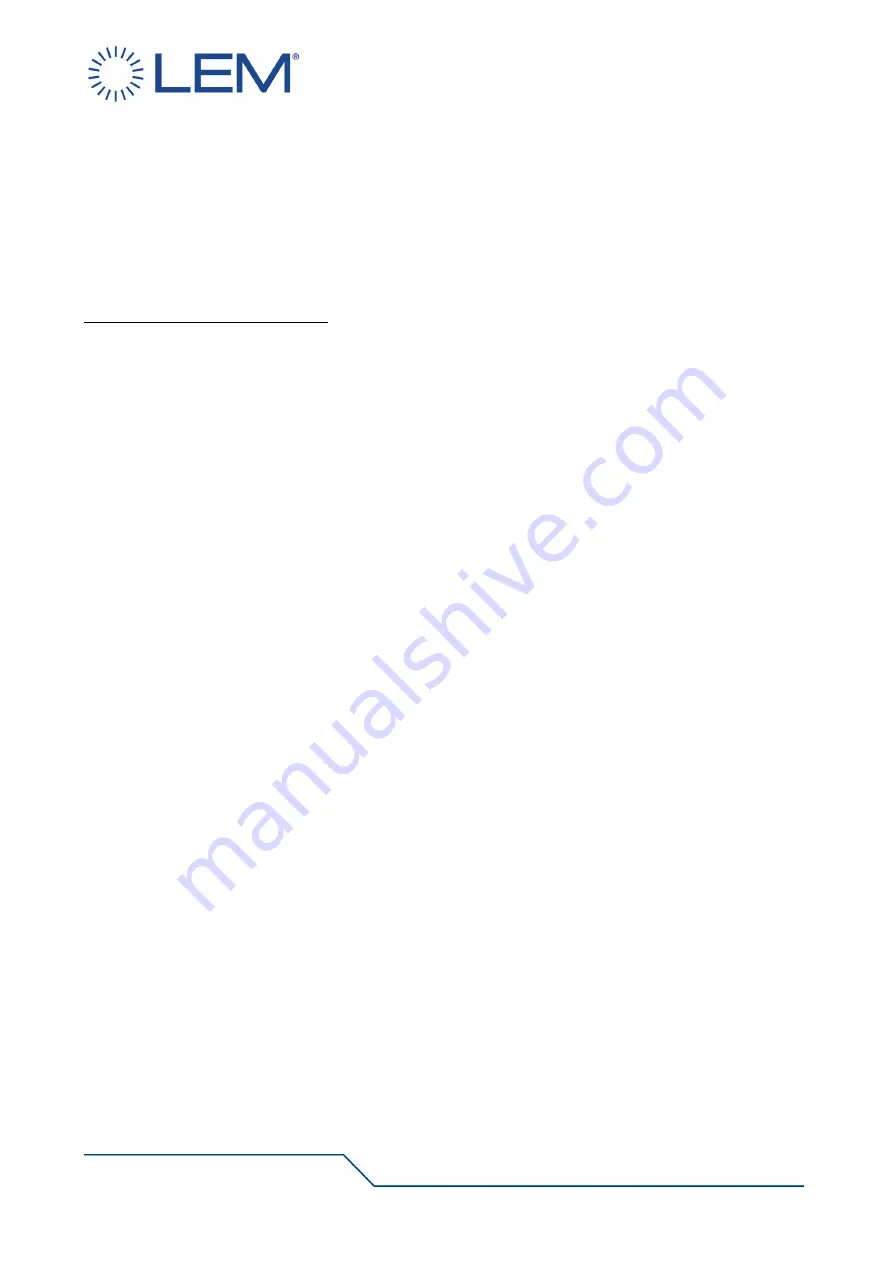
N°98.60.17.013.0
17/ 19
080424/1
4 INSTALLATION
Installation of this equipment must only be carried out by a qualified person.
4.1 System Connections
Connections to the battery blocs:
1. Secure the Kelvin washers to the bloc terminals. Be sure to position the washers such
that it will be possible to attach the power/sense cables.
2. Using the push-on connectors, attach the power/sense cables to the dual tabs on each of
the Kelvin washers.
Be sure to observe the correct polarity:
red wires to positive, black
wires to negative terminal.
3. Attach each Sentinel to the bloc thanks to its ‘double-sided’ tape on its back so that the
power/sense cables can easily reach power connector on Sentinel. Do
not
connect the
Sentinels to the power/sense cables at this time.
4. Using the S-Bus short communication cables, connect the Sentinels to each other in a
daisy-chain manner. It does not matter which port on the Sentinel is used (they are
internally connected in parallel). The vacant port on the first Sentinel should be linked to
the S-Bus converter port, using a shortest communication cable as possible. If the Control
system is quite long away from the battery, prefer to use a longer RS232 serial cable in
order to get the complete S-BUS link length in less than 20 m.
5. Install the LEM current transducer on the main positive cable from the battery. Observe
correct current flow: the arrow on top of the transducer indicates positive current, so it
must be pointed towards the +Ve post, if it is assumed that charge and float currents are
positive (flowing into battery) and discharge current is negative (flowing out of the
battery).
6. Connect the signal cable from the current transducer to the I-Link. Connect also power to
transducer from the specific I-Link cable. Do
not
apply power to the I-Link at this time.
7. If several I-Link modules are used, connect each together in daisy-chain via the I-Bus
communication cables (short ones). It does not matter which port on the I-Link is used.
Connect then the I-Bus cable end to another S-Bus converter, using a short
communication cable, whose serial 25-points connector is linked to any serial port on the
control system.