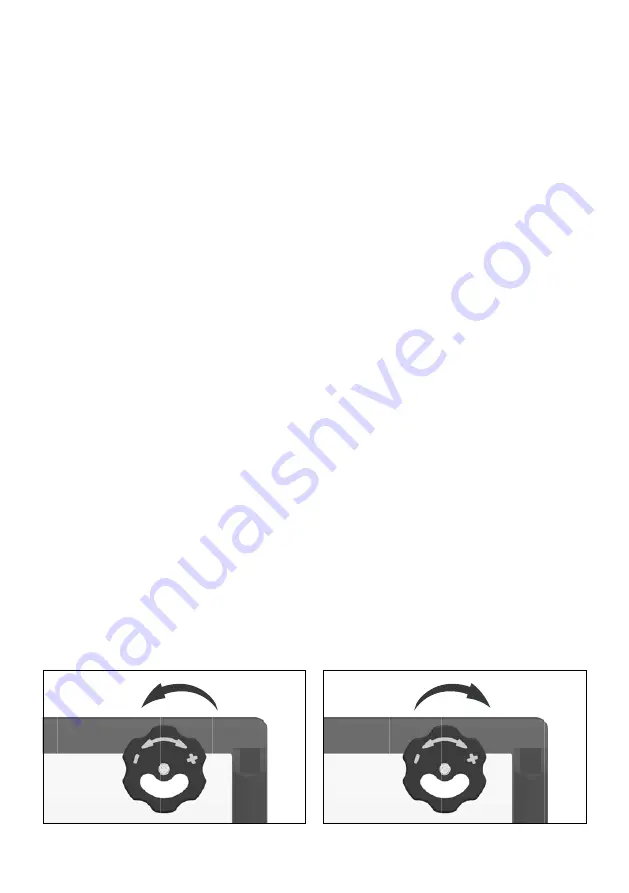
11
6.3. Test with VACUUM PLATE
6.2. Preparation and operation
Turn clockwise (+)
pressure setting valve closed/maximum pressure
Turn anti-clockwise (-)
pressure setting valve open/minimum pressure
• The welding area must be dry and free of contamination. Dirt particles may compromise the test.
• The seam area to be inspected must be sprayed with a liquid forming bubbles (e.g. soapy water) directly
before the inspection. The liquid must not damage the seam and the weld material.
•
Set the pressure setting valve (Vari-Flow Valve) (9)
to minimum pressure before the test. Turn counter-
clockwise until stop (-).
• Position the VACUUM PLATE on the location to be tested
• Place the VACUUM PLATE so that the seam to be tested is approximately in the middle of the longitudinal axis
of the testing device. For longer test sections, the VACUUM PLATE needs to be repositioned accordingly. When
moving the VACUUM PLATE, the test areas must be overlapped.
• In order to generate a negative pressure, the VACUUM PLATE must be pressed lightly on the location to be
tested with both
handles (8).
•
Turn on the main switch (2)
on the VACUUM PLATE
• Turn the
pressure setting valve (Vari-Flow Valve) (9)
clockwise (+) until the desired or specified test
pressure is set.
• The existing negative pressure can be read on the
manometer (5)
.
• Visual inspection of the weld seam for leaks
• The seam is sealed if there are no bubbles in the test liquid.
•
Switch off the main switch (2)
of the VACUUM PLATE, let the device cool down
• Then disconnect the
power cord (1)
from the electrical mains.
• Mark and repairany leaks
• Before each start, check the VACUUM PLATE for faults and damage, e.g. cracks, splits or scratches; a defec-
tive VACUUM PLATE can implode
• Visually inspect that the
filter plate (4)
is present and whether it is clean.
•
Check the power supply line and plug (1)
as well as the extension cable for electrical and mechanical
damage.
•
Check the cooling air openings (11)
must be open at all times and air must be able to be suctioned and
purged unhindered
• Ensure the
sealing lip (7)
is not damaged
•
Warning:
Excessive damage to the sealing
lip (7)
may prevent the required test pressure from being reached.
• Connect the VACUUM PLATE
to the nominal voltage
. The
nominal voltage
specified on the device must
match the
supply voltage
.