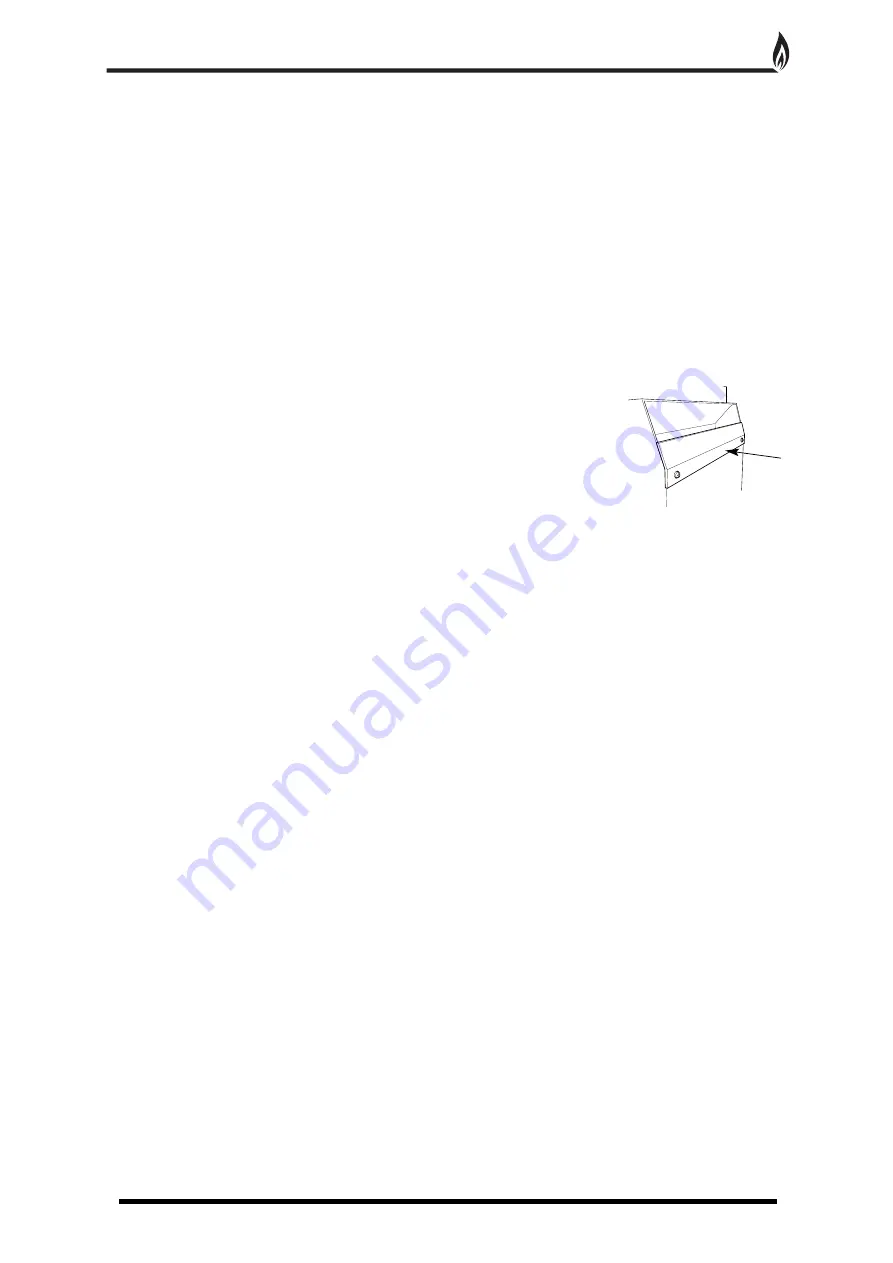
INSTALLATION REQUIREMENTS
4
This appliance must only be installed in Great Britain or Ireland.
1. This appliance is a natural gas appliance only and has been designed for use with the following applications:
a)
Class I
- Conventional brick or stone chimney as used for a solid fuel fire with a cross sectional dimension of
225mm x 225mm (9” x 9”) or a lined flue with a minimum diameter of 175mm (7”), with the fireplace components
conforming to BS1251, or a builders opening a minimum of 560mm high and 335mm wide with a minimum depth
of 110mm to allow sufficient volume for debris collection. To obtain this depth it would not normally be necessary
to remove the chair brick. Any permanent flue restrictions or variable dampers are to be removed or locked in the
fully open position. The chimney should also be swept prior to installation.
b)
Class II
- A double walled or insulated metal flue box built to the requirements of BS715 with an insulated flue
having a minimum diameter of 125mm (5”) and a minimum effective overall height of 3 metres (10’).
c)
Pre-cast Flue
conforming to BS 1289 Part 1 (It may be necessary to use a surround with a deeper rebate
than usual to accommodate a flush fit with certain starter blocks. Check the appliance dimensions against
individual applications. Pre-cast flue block systems should comply with BS EN 1806 (clay/ceramic) or BS EN
1858 (concrete). The flue area measurement is taken on the rectangular section above the gather block (length
x depth). The cross sectional area on post 1986 systems should not be less than 16500mm sq with a minimum
internal dimension 90mm. Gas operatives need to be aware that before 1986 the cross sectional area
specification was 13000mm sq with the minimum dimension of 63mm. In the case of the smaller flue the outlet
restrictor plate
MUST
be fitted (see Fig. 2a).
2. A non-combustible hearth must be provided to comply with current building
regulations. Care should be taken to prevent any damage being caused to
surrounding soft furnishings or decoration, e.g. many embossed vinyl wall coverings
may become discoloured if placed too close to the appliance.
3. A suitable proprietary fire surround with 100
0
c rating may be used with a minimum
clearance from hearth to underside of shelf of 830mm, providing that the depth of shelf is 150mm or less.
4. Where the shelf depth is greater than 150mm, the minimum height clearance should be increased by 25mm
increments for each additional 12.5mm of shelf depth.
5. Minimum width between vertical sides of combustible surround should not be less than 800mm provided the
appliance is central to the surround and the surround legs do not exceed a 150mm profile.
6. If the 150mm profile is exceeded, the width of the surround (and the back panel) should be increased by
25mm for each additional 12.5mm of profile depth.
FLUE FLOW TEST
A flue flow test (smoke test) is carried out to check the effectiveness of the flue and to ensure that there is no
leakage into another part of the premises (including any loft), or as appropriate other adjoining premises (this is
particularly important where a number of chimneys combine into a multiple stack).
The flue flow test should be carried out using a suitable smoke pellet which the pellet manufacturer claims to
generate 5m
3
of smoke in 30 seconds burn time.
These gas fires should have the flue flow test carried out with the appliance in position but not connected to the
gas supply so that the smoke test can be carried out with representative flue flow conditions.
A warm flue will be more effective than a cold flue. If the flue is reluctant to draw, which can be initially assessed
by lighting a smoke match at the intended position of the appliance flue connection, introduce some heat into the
flue for a minimum of 10 minutes using a blow torch or other means.
Other factors, such as weather conditions and a combination of materials used to construct the flue can all
influence the flue draught. The pre-heating process may require as much as half an hour before the flue behaves
satisfactory as a blow torch does not represent the volume of heat consistent with the normal appliance
operation. A Flue Flow Test should be checked as follows:
1. Carry out those visual checks as indicated previously, and continue only if satisfactory.
2. Establish that an adequate air supply is available for the combustion of the appliance
3. Close all doors and windows in the room that the appliance is to be installed.
4. Light a smoke pellet at the intended position for the appliance. Place the inset fire case into position.
5. The test is satisfactory if: - there is no significant escape of smoke from the appliance position.
- there is no seepage of smoke over the length of the flue.
- smoke is discharged only from the correct terminal.
VENTILATION
No special ventilation bricks or vents are required in the room containing the appliance, providing that normal
adventitious room ventilation exists. The installer must determine this by carrying out a spillage test.
SPILLAGE TEST
To check for satisfactory clearance of products of combustion, close all doors and windows and leave the fire
burning for five minutes. Insert a lit smoke match on a vertical plane 50mm down, 50mm inside the canopy
opening. All the smoke must be drawn into the flue. If spillage occurs, allow a further ten minutes and repeat the
test. Should spillage still occur turn the appliance off and seek expert advice.
To continue the test: If an extractor fan is situated in the room the test should be repeated with the fan running. If
there is a connecting room with an extractor fan the test should be repeated with all the doors to that room open
and the extractor fan running.
Fig. 2a
Restrictor