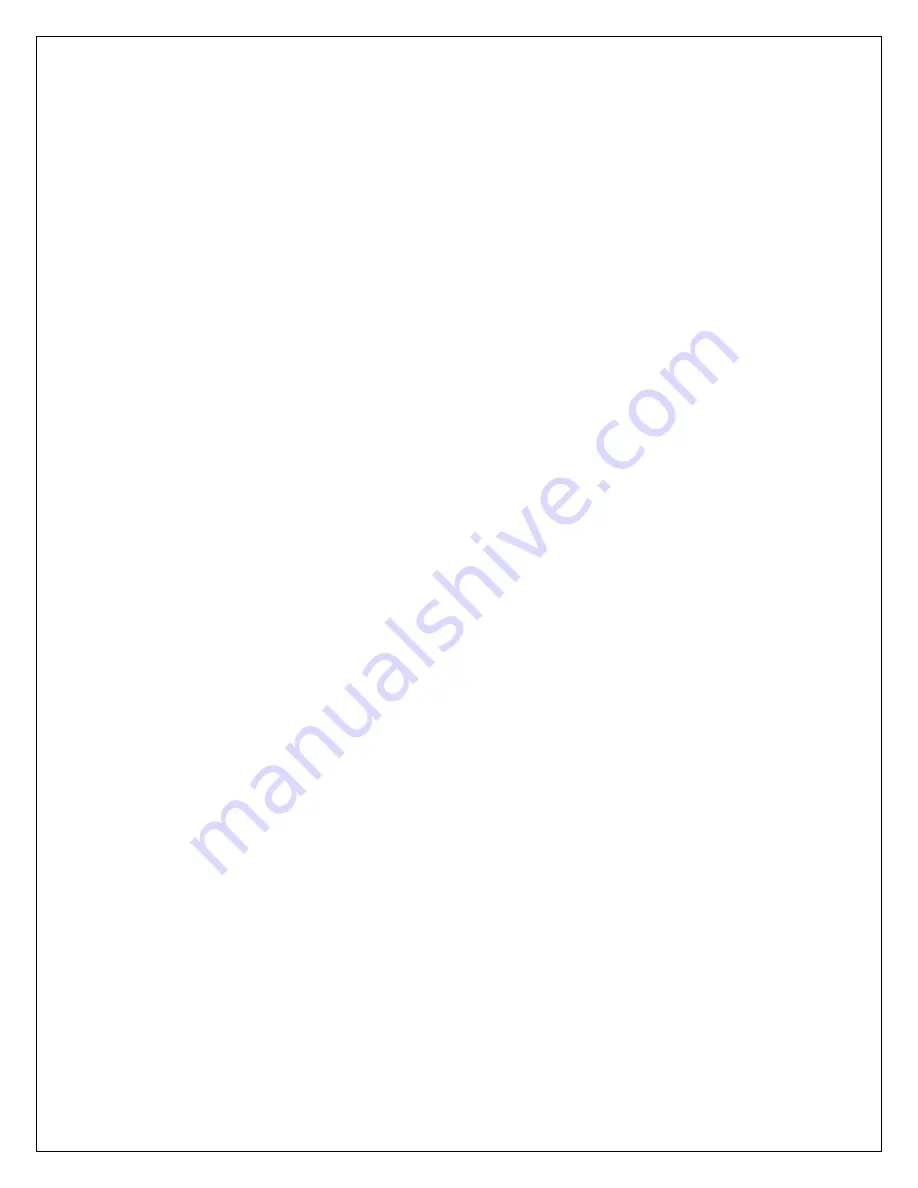
01.2009 v. 3.00
5-5 PREVENTING AND SOLVING PROBLEMS
WHEN USING HOT LAMINATES
Please read this section before you have a problem.
PROBLEM:
Wrinkling of the material as it goes into the laminating rollers.
This problem usually occurs when laminating an item that has been folded, rolled,
bent or wrinkled.
SOLUTION:
Make sure the leading edge of the item being laminated is lying flat
and is inserted parallel to the laminating rollers.
It is sometimes essential to smooth out an item as it passes over the feed table and
through the rollers to ensure an even lamination without wrinkles. Smooth from the
center of the item, back toward the trailing edges. Once the item starts to feed, you
may also pull back and to the sides on the corners of the trailing edge.
If material has been rolled up, take the curl out of it on a table edge before
laminating. If some curl remains, it may be helpful to insert the item with the curl
down so the leading edge is pressed against the feed tray until just before the nip.
PROBLEM:
Wrinkling of the film around the material being laminated.
SOLUTION:
This is normal and inevitable on any laminator, especially with thicker
material. These wrinkles will be trimmed away with the scrap, so they do not affect
appearance. Because the rollers are being held apart by the paper or cardboard,
they cannot pull equally on the plastic around the paper. This creates wrinkles that
tend to look like the bow waves of a boat, radiating out through the clear part of the
web from the sheet of material.
PROBLEM:
When two pieces of material are laminated side by side, the
plastic adheres to one piece but not the other.
SOLUTION:
To get maximum efficiency from the film rolls, you can feed several
items into the laminator side by side. However, wrinkling can occur if these items
are of unequal thickness, because the laminating rollers are lifted off the thinner
items by the thicker items. When laminating items side by side, it is important to
arrange them so that the thickness is the same.
PROBLEM:
Wrinkling of the plastic on a laminated piece of material.
SOLUTION:
Make sure you have enough film tension to take the wrinkles out of
the film before it gets past the heat rolls (see film tension, sections 5-2 and 5-4).
Make sure the film is threaded properly (see threading the laminator, section 3-2).
PROBLEM:
Film gets wrapped around the pull rollers.
SOLUTION:
While threading cold film, the loose ends of the unlaminated web are
particular
ly susceptible to “wrap-around.” To minimize this, always tape the top and
bottom films together in a couple of places to keep them attached to each other
while passing through the rollers. Pull the threading card after it emerges from the