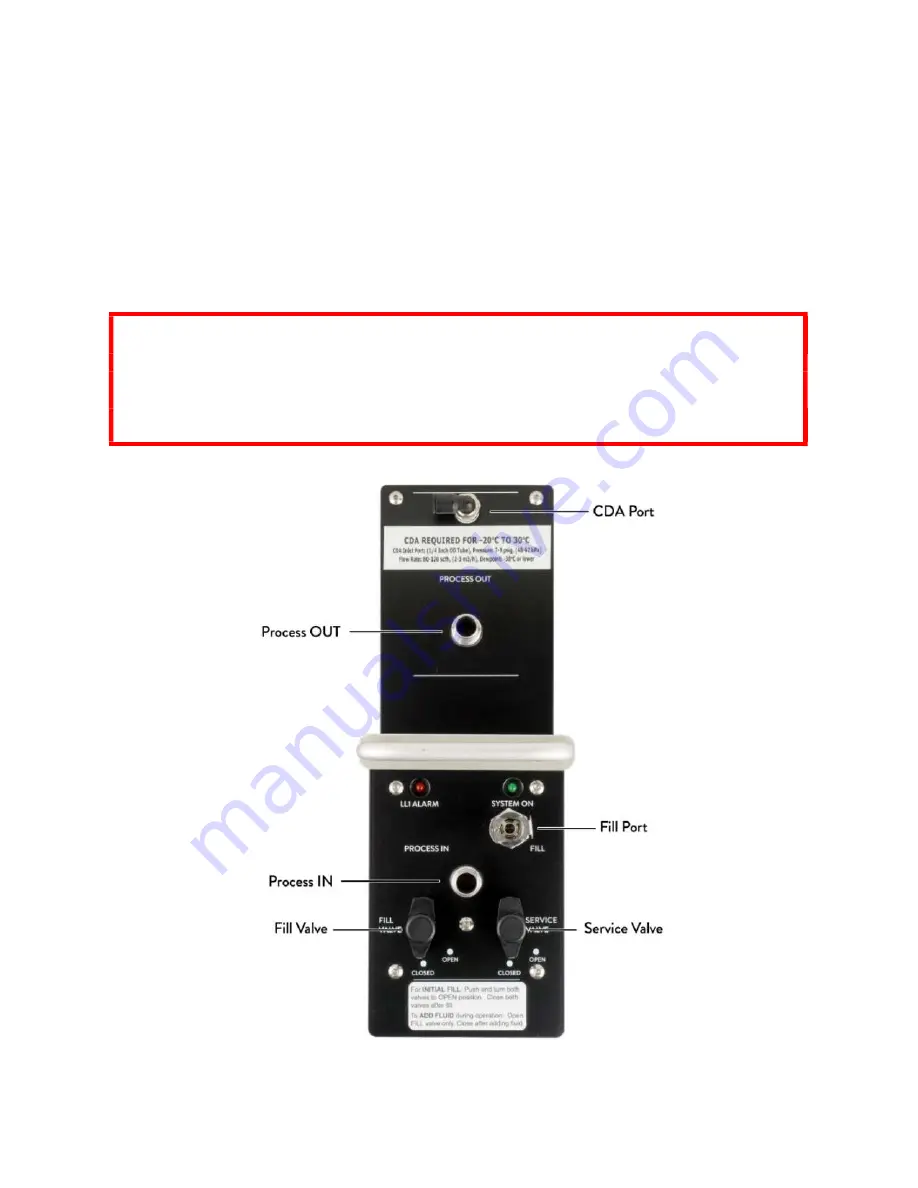
Models S 1200, S 2400, S 4400, POU 3300, POU 3500
-
10
-
2.5.
Fluid Connections
Process Side
The following pictures depict the top view of the unit. The Process OUT and Process IN ports
have a LAUDA-Noah proprietary connector that can be adapted to either a barb fitting or a ½
Swagelok® compression/tube adapter.
WARNING:
For applications where the temperature set point of the unit is less than the dew point of the
environment, CDA (Clean Dry Air) must be used to protect the unit from condensation. Be sure to
supply this port with the recommended CDA flow rate. CDA specifications are listed in a label on the
unit.
POU 3300/S 2400